Top bracket manufacturing in China introduce,list main products and website if have
Top bracket manufacturing companies in China offer a wide range of high-quality brackets for various applications. Some of the main products that these companies produce include shelf brackets, support brackets, wall brackets, angle brackets, corner brackets, and L brackets.
One of the leading bracket manufacturing companies in China is Shanghai Baily Metal Products Co., Ltd. They specialize in producing a variety of brackets for different industries such as construction, furniture, and automotive. Some of their main products include metal angle brackets, decorative shelf brackets, and heavy-duty support brackets. To learn more about their products, you can visit their website at www.bailymetal.com.
Another top bracket manufacturing company in China is Ningbo Dasheng Metal Products Co., Ltd. They have been providing high-quality brackets for over 20 years and offer a wide range of products including adjustable brackets, square brackets, and pipe brackets. You can find more information about their products by visiting their website at www.dsmetal.com.
Both Shanghai Baily Metal Products Co., Ltd. and Ningbo Dasheng Metal Products Co., Ltd. are known for their reliable products, competitive pricing, and excellent customer service. If you are looking for top-quality brackets for your next project, consider reaching out to these trusted manufacturers in China.
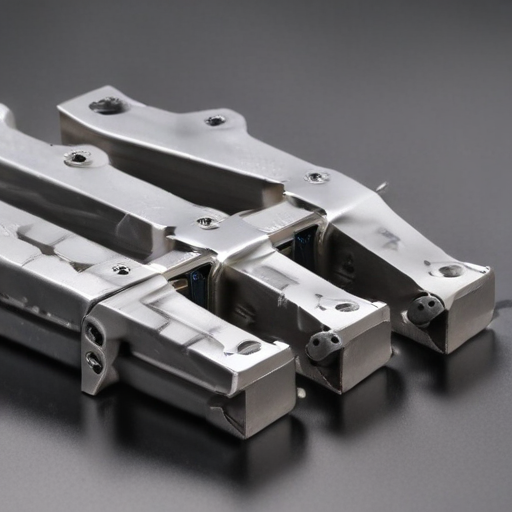
Types of bracket manufacturing
There are several different types of bracket manufacturing processes that can be used depending on the specific requirements of the project. Some common techniques include:
1. Stamping: This process involves using a machine to cut and shape sheet metal into the desired bracket shape. Stamping is a cost-effective and efficient manufacturing method that is well-suited for producing large quantities of brackets with a consistent shape and size.
2. Laser cutting: Laser cutting is a precise and efficient manufacturing process that uses a high-powered laser to cut through sheet metal with great accuracy. This method is ideal for producing brackets with intricate designs or precise dimensions.
3. CNC machining: Computer Numerical Control (CNC) machining involves using computer-controlled machines to shape metal into the desired bracket design. This method is highly versatile and can be used to produce brackets of almost any shape or size.
4. Welding: Welding is a common manufacturing process used to join metal pieces together to create brackets with complex shapes or structures. This method is ideal for producing brackets that require a high degree of strength and durability.
5. Extrusion: Extrusion involves forcing metal through a die to create brackets with a uniform cross-sectional shape. This method is often used to produce brackets with a consistent profile and is well-suited for high-volume manufacturing.
Overall, the choice of bracket manufacturing technique will depend on factors such as the desired bracket design, material type, production volume, and budget constraints. By selecting the right manufacturing process, companies can ensure that their brackets are produced to the highest quality standards and meet the specific requirements of their application.
Pros and Cons of Using bracket manufacturing
Bracket manufacturing has both pros and cons for businesses looking to produce brackets for various industries.
One of the main advantages of using bracket manufacturing is the ability to mass-produce durable and precise brackets. With advanced machinery and technology, manufacturers can ensure that each bracket is identical and meets the exact specifications required by the customer. This can help to increase efficiency and reduce costs for businesses that rely on brackets for their products.
Additionally, bracket manufacturing can also offer a wide range of customization options for businesses looking to create unique brackets for their specific applications. This flexibility allows companies to design brackets that are tailored to their exact needs, which can help to improve the performance and functionality of their products.
However, there are also some drawbacks to using bracket manufacturing. One potential disadvantage is the initial cost of setting up a manufacturing operation, which can be substantial. This may be a barrier for smaller businesses or startups looking to produce brackets in smaller quantities.
Another potential downside is the need for skilled labor and expertise to operate the machinery and ensure that the brackets are produced to high standards. This can add to the overall cost of manufacturing brackets and may require businesses to invest in training or hiring skilled workers.
In conclusion, while there are clear benefits to using bracket manufacturing such as efficiency and customization options, there are also potential drawbacks to consider. Businesses should weigh these factors carefully when deciding whether to pursue bracket manufacturing as part of their production process.
bracket manufacturing Reference Specifications (varies for different product)
Bracket manufacturing reference specifications can vary based on the specific product being produced. In general, these specifications outline the materials, design, dimensions, and testing requirements for the bracket to ensure it meets the necessary standards and functions correctly.
Materials used in bracket manufacturing can include various metals such as steel, aluminum, or stainless steel, depending on the strength and corrosion resistance needed for the application. The design of the bracket must take into account factors such as load capacity, stress distribution, and compatibility with other components it will be attached to.
Dimensions for the bracket will typically be specified in terms of length, width, thickness, and hole spacing to ensure proper fit and alignment in the assembly. Manufacturing processes such as cutting, bending, welding, and finishing may be outlined to achieve the desired shape and surface finish.
Testing requirements for brackets may involve load testing, impact testing, corrosion resistance testing, or other performance evaluations to verify that the bracket meets the necessary standards for its intended use. These tests help ensure the bracket will perform safely and reliably in its application.
Overall, following the reference specifications for bracket manufacturing is essential to produce high-quality brackets that meet the required performance and safety standards for their intended use. Adhering to these specifications helps ensure consistency in manufacturing and helps to meet customer expectations for the product.
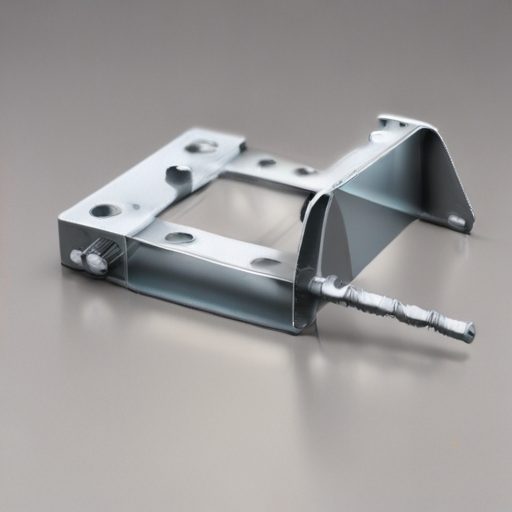
Applications of bracket manufacturing
Bracket manufacturing involves the production of various types of brackets that serve as supports or connections in a wide range of applications. One common application of bracket manufacturing is in the construction industry. Brackets are essential components in building structures, providing support for beams, shelves, and other load-bearing elements. They are used in both residential and commercial construction projects to ensure the stability and strength of the overall structure.
In the automotive industry, brackets play a crucial role in securing various components and parts of vehicles, such as exhaust systems, suspension systems, and engine mounts. These brackets are designed to withstand the rigors of everyday driving and ensure the proper functioning of the vehicle. They are also used in the manufacturing of heavy machinery and equipment to provide support and stability for moving parts and mechanical components.
In the furniture industry, brackets are used to connect different parts of furniture pieces, such as chairs, tables, and shelves. They help to hold the structure together and ensure the durability and stability of the furniture. Brackets are also utilized in the aerospace industry to secure components in aircraft and spacecraft, providing support and structural integrity in extreme conditions.
Overall, bracket manufacturing has a wide range of applications across various industries, including construction, automotive, furniture, and aerospace. The production of high-quality brackets is essential to ensure the safety, durability, and efficiency of the products and structures in which they are used.Manufacturers continue to innovate and develop new bracket designs to meet the evolving needs of different industries and applications.
Material of bracket manufacturing
Brackets are typically manufactured from a variety of materials, each offering their own set of advantages and disadvantages. Some of the most common materials used in bracket manufacturing include:
1. Steel: Steel is a strong and durable material that is commonly used in the manufacturing of brackets. It is capable of withstanding heavy loads and is resistant to corrosion, making it ideal for use in outdoor or industrial settings. However, steel brackets can be heavy and may require additional support structures.
2. Aluminum: Aluminum is a lightweight material that is often used in the manufacture of brackets for applications where weight is a concern. It is also corrosion-resistant and easy to work with, making it a popular choice for brackets used in construction, automotive, and aerospace industries.
3. Stainless steel: Stainless steel is a highly durable and corrosion-resistant material that is often chosen for brackets used in harsh environments or where hygiene is a concern. It is easy to clean and maintain, making it suitable for use in kitchens, hospitals, and laboratories.
4. Plastic: Plastic brackets are lightweight, inexpensive, and resistant to corrosion, making them ideal for use in a wide range of applications. They are often used in furniture manufacturing, consumer electronics, and automotive industries.
5. Composite materials: Composite materials, such as fiberglass or carbon fiber, offer the strength and durability of traditional materials like steel or aluminum, but with the added benefit of being lightweight and rust-resistant. These materials are often used in high-performance applications where weight savings are critical.
In conclusion, bracket manufacturers have a variety of materials to choose from, each with its own unique properties and benefits. The choice of material will depend on the specific requirements of the application, including weight, strength, corrosion resistance, and cost considerations.
Quality Testing Methods for bracket manufacturing and how to control the quality
When it comes to testing the quality of bracket manufacturing, there are several methods that can be utilized to ensure that each bracket meets the necessary standards. These methods typically include visual inspection, dimensional measurement, material composition analysis, and physical testing.
Visual inspection is one of the most common quality testing methods for bracket manufacturing. This involves examining each bracket for any visible defects, such as cracks, dents, or surface irregularities. Visual inspection can be done manually or with the help of automated systems to ensure thoroughness and accuracy.
Dimensional measurement is another important quality testing method for bracket manufacturing. This involves using precision tools, such as calipers or coordinate measuring machines, to verify that each bracket’s dimensions meet the specifications outlined in the design drawings. This helps ensure that the brackets will fit properly and function as intended.
Material composition analysis is also crucial in testing the quality of bracket manufacturing. This involves analyzing the material used to make the brackets to ensure it meets the required specifications for strength, durability, and corrosion resistance. This can be done through various methods, such as chemical analysis or mechanical testing.
Physical testing is another key method for ensuring the quality of bracket manufacturing. This involves subjecting the brackets to various tests, such as load testing, fatigue testing, or environmental testing, to evaluate their performance under different conditions. This helps ensure that the brackets can withstand the demands placed on them in real-world applications.
To control the quality of bracket manufacturing, it is important to establish clear quality control procedures and standards, conduct regular inspections and testing throughout the manufacturing process, and address any issues or defects promptly. By following these steps, manufacturers can ensure that each bracket meets the necessary standards for quality and reliability.
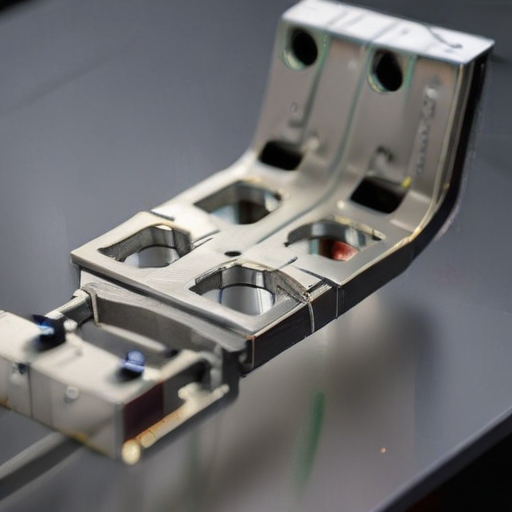
The Work Process and how to use bracket manufacturing
The work process for bracket manufacturing involves several steps to produce high-quality brackets that are used in various industries such as construction, automotive, and aerospace.
The first step is to design the bracket using computer-aided design (CAD) software. This allows the engineer to create a precise and detailed design that specifies the dimensions, materials, and any additional features required for the bracket.
Once the design is finalized, the next step is to select the appropriate material for the bracket. Common materials used for bracket manufacturing include aluminum, steel, and plastic. The material is chosen based on the application and requirements of the bracket.
After selecting the material, the manufacturing process begins. This typically involves cutting the material into the desired shape using a laser cutter, water jet, or other cutting methods. The next step is to bend the material into the correct shape using a press brake or other bending equipment.
Following the bending process, any additional features such as holes or threads are added to the bracket through drilling, tapping, or welding. Finally, the bracket is finished with surface treatments such as painting, powder coating, or anodizing to protect it from corrosion and enhance its appearance.
In conclusion, bracket manufacturing involves designing, selecting materials, cutting, bending, adding features, and finishing the bracket to meet the requirements of the application. By following these steps, manufacturers can produce high-quality brackets that are essential components in various industries.
bracket manufacturing Importing questions including Cost,Supplier,Sample,Certification and Market
Cost is an important factor to consider when importing brackets for manufacturing. It is essential to compare prices from different suppliers to ensure you are getting the best deal. In addition to the initial cost of the brackets, you should also factor in shipping, customs duties, and any other potential fees.
When sourcing a supplier for brackets, it is crucial to find one that is reliable and offers high-quality products. Look for suppliers with a strong track record of delivering goods on time and meeting quality standards. Requesting samples from potential suppliers is a good way to evaluate the quality of their products before making a larger purchase.
Certification is another important consideration when importing brackets for manufacturing. Make sure that the brackets meet industry standards and regulations to avoid any potential issues down the line. Look for suppliers that have the necessary certifications for the products they are selling.
Understanding the market for brackets in your industry is key to making informed decisions about importing. Research market trends, demand for brackets, and potential competitors to ensure that there is a viable market for your products.
Overall, when importing brackets for manufacturing, it is important to carefully consider cost, supplier reliability, product samples, certification, and market conditions to ensure a successful and profitable import process.
How to find and select check reliable bracket manufacturing manufacturers in China
When looking for a reliable bracket manufacturing manufacturer in China, it is important to research and evaluate potential suppliers to ensure they meet your quality and cost requirements.
One way to find manufacturers is through online sourcing platforms such as Alibaba or Made in China, where you can search for suppliers based on specific criteria such as location, production capacity, and certifications. You can also attend trade fairs and exhibitions in China to meet potential suppliers in person and discuss your requirements.
To ensure the reliability of a manufacturer, it is important to conduct thorough due diligence. This can include checking the manufacturer’s business license, certifications, and quality control processes. You can also ask for references and customer testimonials to gauge their reputation and track record.
When selecting a manufacturer, consider factors such as production capacity, lead times, and pricing. It is also important to communicate your requirements clearly and establish a strong relationship with the manufacturer to ensure smooth production and timely delivery of your bracket components.
Overall, by conducting thorough research, due diligence, and communication with potential manufacturers, you can find a reliable bracket manufacturing partner in China that meets your quality and cost requirements.
Background Research for bracket manufacturing manufacturers Companies in China, use qcc.com archive.org importyeti.com
When looking for bracket manufacturing manufacturers in China, QCC.com is a valuable resource to consider. This website provides a platform for companies to showcase their manufacturing capabilities, certifications, and products. By browsing through the listings on QCC.com, businesses can identify potential bracket manufacturing manufacturers based on their expertise and experience in the industry.
Another useful tool for researching bracket manufacturing manufacturers in China is Archive.org. This website allows users to access archived versions of websites, which can be helpful in determining a company’s history and track record. By reviewing a manufacturer’s website on Archive.org, businesses can gain insights into their longevity in the industry, their past projects, and any customer testimonials or reviews.
ImportYeti.com is also a valuable resource for researching bracket manufacturing manufacturers in China. This platform provides information on companies that export products to the United States, including details on their products, shipment volumes, and trade patterns. By searching for bracket manufacturing manufacturers on ImportYeti.com, businesses can gain valuable insights into the scale of their operations and their export capabilities.
Overall, by using these resources, businesses can easily identify and evaluate bracket manufacturing manufacturers in China based on their capabilities, track record, and export activities. This enables businesses to make informed decisions when selecting a manufacturer that meets their specific requirements and standards.
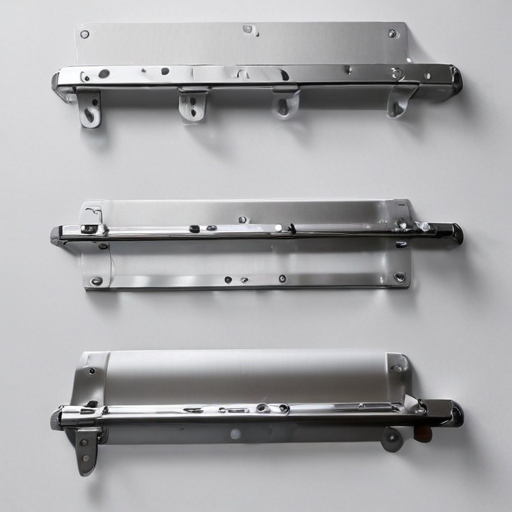
Price Cost Research for bracket manufacturing manufacturers Companies in China, use temu.com and 1688.com
Bracket manufacturing is a specialized industry that requires precision engineering and high-quality materials. In order to find the best price and cost options for bracket manufacturing in China, two popular websites that can be utilized are temu.com and 1688.com.
Temu.com is a comprehensive online marketplace that connects buyers with manufacturers and suppliers in China. By searching for bracket manufacturing companies on Temu, users can compare prices, specifications, and customer reviews to find the most suitable supplier for their needs. Additionally, Temu offers a secure payment system and buyer protection policies to ensure a smooth and reliable purchasing experience.
1688.com is another popular platform for sourcing manufacturers in China. As a subsidiary of Alibaba Group, 1688 specializes in connecting international buyers with Chinese suppliers for a wide range of products, including bracket manufacturing. Users can search for specific products, compare prices, negotiate with suppliers, and place orders directly through the website. With millions of suppliers listed on 1688, buyers can find competitive pricing and a wide selection of bracket manufacturing companies to choose from.
By using these two websites, buyers can conduct comprehensive research on price and costs for bracket manufacturing in China. They can compare quotes, evaluate suppliers, and make informed decisions based on their specific requirements and budget constraints. Overall, Temu.com and 1688.com are valuable resources for connecting with reliable bracket manufacturing companies in China at competitive prices.
Shipping Cost for bracket manufacturing import from China
When importing bracket manufacturing products from China, the shipping cost will depend on various factors such as the size and weight of the shipment, the shipping method chosen, and the destination country.
One of the most common shipping methods for importing products from China is sea freight. The cost of sea freight can vary depending on the volume of the shipment and the shipping route. On average, the cost of shipping a standard 20-foot container from China to the United States can range from $1,500 to $3,000. For larger shipments, a 40-foot container may be required, which can cost between $2,000 to $4,000.
Another shipping method is air freight, which is faster but more expensive than sea freight. The cost of air freight is calculated based on the weight and dimensions of the shipment, as well as the destination. On average, the cost of shipping a 100kg package from China to the United States can range from $600 to $1,200.
It is important to also consider additional costs such as customs duties, taxes, and handling fees when calculating the total shipping cost. Working with a freight forwarder or shipping agent can help navigate the logistics of importing products from China and ensure a smooth delivery process.
In conclusion, when importing bracket manufacturing products from China, it is essential to factor in shipping costs as they can significantly impact the overall cost of the imported goods. By carefully considering shipping methods and costs, importers can optimize their supply chain and ensure timely delivery of products.
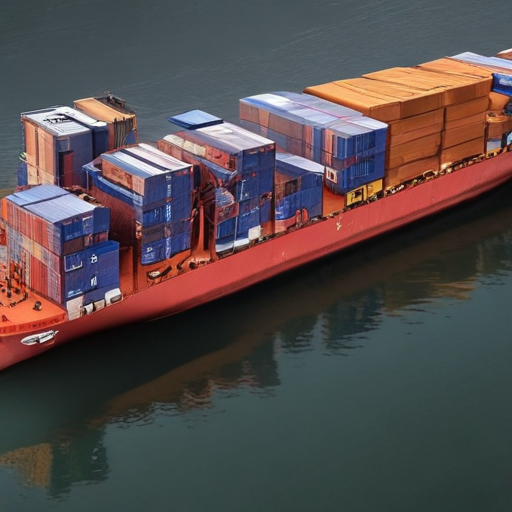
Compare China and Other bracket manufacturing Markets: Products Quality and Price,Visible and Hidden Costs
China is known for its competitive pricing in the bracket manufacturing market, offering products at lower costs compared to other markets. However, the quality of brackets produced in China can vary significantly. Some manufacturers in China may offer lower-quality products to meet demanding price points, while others may focus on producing higher-quality brackets.
In comparison, other bracket manufacturing markets such as the United States or Europe generally offer higher quality products with stricter regulations and standards in place. This often results in more reliable and durable brackets but at a higher price point.
When considering visible costs, China may initially appear to have the advantage due to its lower price tags. However, hidden costs such as shipping, import duties, and communication barriers can add up and impact the overall cost of sourcing brackets from China. On the other hand, sourcing brackets from other markets may have higher upfront costs but may offer more transparency and easier communication, resulting in lower hidden costs in the long run.
In conclusion, while China may offer competitive pricing in the bracket manufacturing market, the quality of products may vary, and hidden costs can impact the overall cost of sourcing brackets. Other markets may offer higher quality products at a higher price point but with potentially lower hidden costs and more transparent communication channels. It is essential for buyers to carefully consider their priorities and budget constraints when sourcing brackets from different markets.
Custom Private Labeling and Branding Opportunities with Chinese bracket manufacturing Manufacturers
Chinese bracket manufacturing manufacturers offer custom private labeling and branding opportunities for businesses looking to establish their own brand in the market. With the ability to customize product designs and packaging, businesses can create a unique and distinctive product that sets them apart from competitors.
By partnering with a Chinese bracket manufacturing manufacturer, businesses can benefit from their expertise in producing high-quality brackets at competitive prices. The manufacturer can work closely with businesses to understand their specific requirements and deliver customized solutions that meet their branding and marketing needs.
Additionally, businesses can take advantage of the manufacturer’s industry knowledge and experience to create products that are in line with market trends and consumer preferences. This can help businesses stay ahead of the competition and attract more customers to their brand.
Overall, working with a Chinese bracket manufacturing manufacturer offers businesses a cost-effective and efficient way to produce custom-branded products that meet their unique specifications. By leveraging the manufacturer’s capabilities and resources, businesses can create a strong brand identity and grow their market presence.
Tips for Procurement and Considerations when Purchasing bracket manufacturing
When purchasing bracket manufacturing services, there are several factors to consider to ensure you are making the best decision for your procurement needs. Here are some tips and considerations to keep in mind:
1. Quality: Make sure to evaluate the quality of the brackets being manufactured. Look for a supplier with a proven track record of producing high-quality, reliable products.
2. Price: While cost is an important factor, it should not be the sole determining factor. Consider the overall value that the supplier provides in terms of quality, lead times, and customer service.
3. Lead times: Consider the lead times offered by the supplier. Make sure they can meet your project deadlines without compromising on quality.
4. Customization: If you require customized brackets, make sure the supplier has the capabilities to meet your specific requirements.
5. Certification: Check if the supplier is certified and compliant with relevant industry standards and regulations. This ensures that the brackets meet the necessary quality and safety requirements.
6. Supplier reputation: Research the supplier’s reputation in the industry. Look for reviews and testimonials from other customers to gauge their reliability and customer service.
7. Communication: Effective communication with the supplier is key to a successful procurement process. Make sure they are responsive and transparent in their communication.
8. Scalability: Consider the scalability of the supplier’s production capabilities. Can they accommodate your future needs and potential growth?
By taking these factors into consideration, you can make an informed decision when selecting a supplier for bracket manufacturing services. Remember to prioritize quality and reliability to ensure the success of your procurement process.
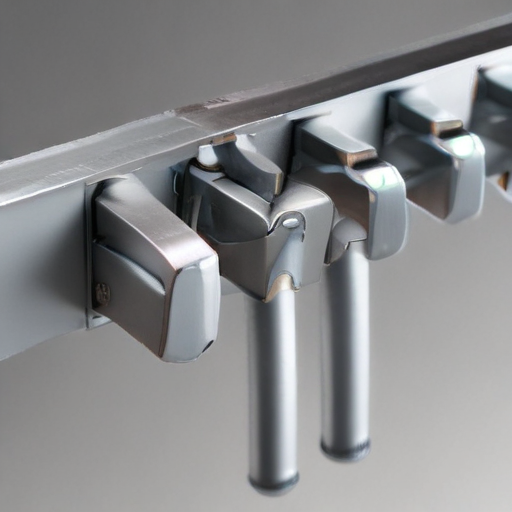
FAQs on Sourcing and Manufacturing bracket manufacturing in China
1. Why should I consider sourcing bracket manufacturing in China?
Sourcing bracket manufacturing in China can be cost-effective due to lower labor costs and a well-established manufacturing infrastructure. Additionally, China has a large pool of skilled labor and advanced technologies, which can result in high-quality products.
2. How can I find a reliable manufacturer for bracket manufacturing in China?
You can find a reliable manufacturer through industry trade shows, online sourcing platforms, and referrals from other businesses. It is important to conduct thorough research, visit the manufacturer’s facilities, and request samples before placing a bulk order.
3. What are the common challenges when sourcing bracket manufacturing in China?
Common challenges when sourcing bracket manufacturing in China include language barriers, cultural differences, quality control issues, intellectual property protection, and long lead times. It is important to work with a reputable sourcing agent or partner to navigate these challenges effectively.
4. How can I ensure product quality when manufacturing brackets in China?
To ensure product quality when manufacturing brackets in China, you can conduct regular inspections, implement quality control measures, and provide detailed specifications to the manufacturer. Building a strong relationship with the manufacturer and maintaining open communication can also help address any quality concerns.
5. What are the shipping and logistics considerations when sourcing bracket manufacturing in China?
When sourcing bracket manufacturing in China, it is important to consider shipping costs, lead times, import regulations, and customs clearance procedures. Working with a reputable freight forwarder or logistics provider can help streamline the shipping process and ensure timely delivery of your products.
Why contact sourcifychina.com get free quota from reliable bracket manufacturing suppliers?
Sourcifychina.com is a reputable platform that connects businesses with reliable bracket manufacturing suppliers in China. By contacting Sourcifychina.com, you can get a free quota from these suppliers, which allows you to easily compare pricing, quality, and other factors before making a decision.
Working with reliable bracket manufacturing suppliers through Sourcifychina.com ensures that you receive high-quality products at competitive prices. These suppliers have been vetted for their manufacturing capabilities, experience, and track record of delivering on time and meeting quality standards.
Getting a free quota from reliable bracket manufacturing suppliers through Sourcifychina.com also saves you time and effort in sourcing suppliers on your own. The platform streamlines the process by providing you with a selection of pre-qualified suppliers, making it easy to find the right match for your project.
Overall, contacting Sourcifychina.com for a free quota from reliable bracket manufacturing suppliers is a smart choice for businesses looking to streamline their manufacturing sourcing process and ensure quality and cost-effectiveness.