Top sheet metal joining in China introduce,list main products and website if have
1. Welding: Welding is a common method used to join sheet metal together by melting and fusing the edges. This process is used in various industries such as automotive, construction, and manufacturing. Some popular welding techniques include MIG welding, TIG welding, and spot welding. Website: (www.china-welding.com)
2. Adhesives: Adhesives are another effective way to join sheet metal together without the need for heat. Structural adhesives can bond metal surfaces together, providing a strong and durable connection. This method is ideal for joining dissimilar materials or when welding is not feasible. Website: (www.china-adhesives.com)
3. Riveting: Riveting involves using a rivet to secure two or more pieces of metal together. This method is popular in the aerospace industry for its high strength and durability. Riveting can be done manually or using automated systems for efficiency. Website: (www.china-riveting.com)
4. Clinching: Clinching is a fast and cost-effective way to join sheet metal without heat or additional materials. The process involves deforming metal sheets using a die and punch, which creates a strong mechanical connection. Clinching is commonly used in the automotive and HVAC industries. Website: (www.china-clinching.com)
5. Soldering: Soldering is a method of joining metals using a filler material (solder) that melts at a lower temperature than the base metals. This process is widely used in electronics and plumbing applications. Soldered joints are strong and provide good electrical conductivity. Website: (www.china-soldering.com)
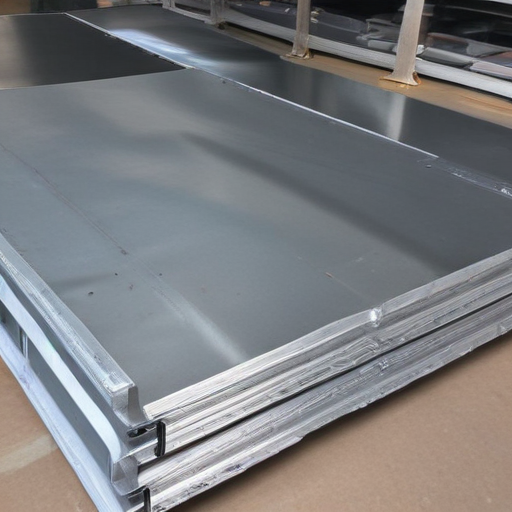
Types of sheet metal joining
There are several common methods for joining sheet metal, each with their own advantages and disadvantages based on the specific application and the materials being used.
1. Welding: Welding is a popular method for joining sheet metal due to its strength and permanence. Common types of welding used for sheet metal include MIG (metal inert gas) welding, TIG (tungsten inert gas) welding, and spot welding. Welding requires specialized equipment and skilled labor but can produce high-quality joints.
2. Riveting: Riveting involves using metal fasteners called rivets to join two pieces of sheet metal together. Rivets are typically inserted through pre-drilled holes in the metal and then deformed to hold the pieces together. Riveting is a quick and cost-effective joining method, but it can also add weight and reduce the aesthetic appeal of the final product.
3. Screws and Bolts: Screws and bolts are commonly used to join sheet metal parts together. This method allows for disassembly and reassembly of the parts, making it ideal for applications where maintenance or repair may be required. However, screws and bolts can create stress points in the sheet metal and may not provide as strong of a joint as welding or riveting.
4. Adhesive Bonding: Adhesive bonding involves using specialized adhesives to join sheet metal parts together. This method can provide a clean and aesthetically pleasing joint, as well as distribute stress across the entire bonded area. However, adhesive bonding may not be as strong as other joining methods and can be sensitive to environmental factors such as temperature and moisture.
5. Clinching: Clinching is a method that involves deforming the sheet metal to create a mechanical joint. This can be done using a clinching machine or a press tool to fold or interlock the metal sheets together. Clinching is a fast and cost-effective joining method but may not provide as strong of a joint as welding or riveting.
Overall, the choice of sheet metal joining method will depend on factors such as the materials being used, the required strength of the joint, and the desired aesthetics of the final product. It is important to consider all of these factors when selecting the most appropriate joining method for a specific application.
Pros and Cons of Using sheet metal joining
Sheet metal joining techniques offer several advantages, such as:
1. Strength: Sheet metal joining methods like welding, riveting, and clinching create strong bonds that can withstand high loads and stresses.
2. Versatility: Sheet metal joining can be used to connect a wide range of materials, including steel, aluminum, and copper.
3. Cost-effectiveness: Sheet metal joining techniques are often more cost-effective than other assembly methods, making them a popular choice for manufacturers.
4. Speed: Sheet metal joining processes are generally fast and efficient, allowing for quick production turnaround times.
5. Design flexibility: Sheet metal joining allows for complex geometries and intricate designs to be achieved, making it a versatile option for a variety of applications.
However, there are also some drawbacks to using sheet metal joining methods:
1. Potential for distortion: Some sheet metal joining techniques, such as welding, can cause distortion or warping of the metal, which may require additional processing to correct.
2. Limited joint strength: While sheet metal joining techniques can create strong bonds, they may not be as strong as other joining methods like welding or adhesive bonding.
3. Complexity: Sheet metal joining methods can be complex and require specialized equipment and expertise, which may increase the overall cost of production.
4. Material limitations: Some sheet metal joining techniques are only suitable for certain materials or thicknesses, limiting their applicability in certain situations.
Overall, sheet metal joining techniques offer a range of benefits but also come with some limitations that should be considered when selecting the most appropriate method for a specific application.
sheet metal joining Reference Specifications (varies for different product)
Sheet metal joining is a commonly used method in various industries to combine individual sheet metal pieces to create a larger and more complex structure. There are different methods of joining sheet metal, each with its own advantages and limitations. Some of the most commonly used joining methods include welding, riveting, and bonding.
Welding is a popular method of joining sheet metal that involves using heat to melt the edges of the metal pieces and fusing them together. Different types of welding techniques can be used, such as gas metal arc welding (GMAW) or spot welding, depending on the specific requirements of the project.
Riveting is another commonly used method of joining sheet metal, which involves using solid rivets or blind rivets to secure the metal pieces together. This method is preferred for applications requiring a strong and durable joint, such as in the aerospace industry.
Bonding is an alternative method of joining sheet metal without the need for heat or mechanical fasteners. Adhesives or tapes are used to bond the metal pieces together, providing a clean and aesthetically pleasing finish. This method is ideal for joining dissimilar materials or when heat cannot be used.
Reference specifications for sheet metal joining may vary depending on the specific product or industry requirements. It is important to consider factors such as material properties, joint strength, corrosion resistance, and cost when selecting the appropriate joining method.
In conclusion, sheet metal joining is a vital process in the manufacturing industry, with different methods available to suit various applications. Understanding the reference specifications and selecting the right joining method is crucial to ensure the quality and performance of the final product.
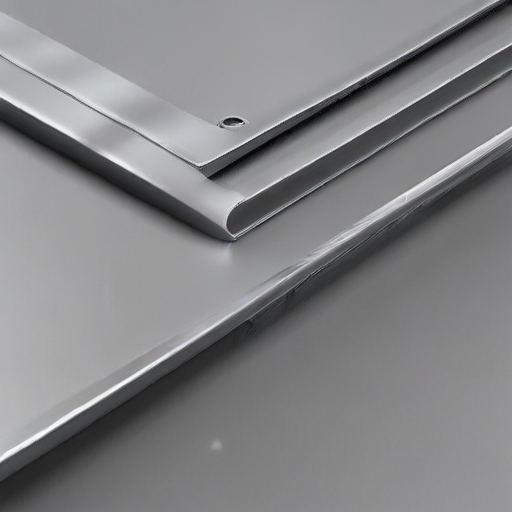
Applications of sheet metal joining
Sheet metal joining is an essential process in various industries such as automotive, aerospace, construction, and manufacturing. Some common applications of sheet metal joining include:
1. Vehicle manufacturing: Sheet metal joining is widely used in the automotive industry for assembling body panels, chassis components, and various structural components. Techniques such as welding, riveting, and adhesive bonding are commonly used to join sheet metal parts in the production of cars, trucks, and other vehicles.
2. HVAC systems: Sheet metal joining is also used in the manufacturing of heating, ventilation, and air conditioning (HVAC) systems. HVAC ducts and components are typically made of sheet metal and are joined together using methods such as spot welding, seam welding, or riveting to create airtight and efficient systems for heating and cooling buildings.
3. Household appliances: Sheet metal joining is commonly used in the production of household appliances such as refrigerators, ovens, and washing machines. Various joining techniques are employed to assemble the sheet metal parts of these appliances, ensuring durability, reliability, and performance.
4. Aerospace industry: Sheet metal joining plays a crucial role in the manufacturing of aircraft components, including fuselage panels, wing sections, and structural elements. Advanced joining techniques such as friction stir welding, laser welding, and diffusion bonding are used to ensure the integrity and safety of aircraft structures.
5. Construction: Sheet metal joining is also used in the construction industry for fabricating building components such as roofing systems, wall panels, and structural frames. Joining methods such as soldering, brazing, and mechanical fastening are employed to create durable and weather-resistant structures for residential, commercial, and industrial buildings.
In conclusion, sheet metal joining is a versatile and essential process in various industries, enabling the fabrication of complex and durable products and structures. Different joining techniques are used based on the specific requirements of the application, ensuring quality, reliability, and efficiency in sheet metal assemblies.
Material of sheet metal joining
There are several methods for joining sheet metal, each with its own advantages and applications. Some common methods include welding, riveting, bolting, and adhesive bonding.
Welding is a popular method for joining sheet metal because it provides a strong, durable bond. There are several types of welding processes that can be used, including MIG (metal inert gas) welding, TIG (tungsten inert gas) welding, and spot welding. Welding works by melting the edges of the two pieces of sheet metal and then allowing them to cool and solidify, creating a solid bond.
Riveting involves using a rivet, a small metal fastener, to join two pieces of sheet metal together. Rivets are typically inserted through pre-drilled holes in the metal and then deformed to secure them in place, creating a tight and secure bond. Riveting is often used in situations where welding may not be feasible or practical.
Bolting is another common method for joining sheet metal. Bolts are inserted through pre-drilled holes in the metal and secured in place with nuts, creating a strong and easily reversible bond. Bolting is often used in situations where the sheet metal pieces may need to be disassembled and reassembled.
Adhesive bonding involves using an adhesive to bond two pieces of sheet metal together. The adhesive is applied to the surfaces of the metal pieces and then allowed to cure, creating a strong and durable bond. Adhesive bonding is often used in situations where welding or other methods may not be feasible or practical, or where a clean and seamless appearance is desired.
Overall, there are several methods for joining sheet metal, each with its own advantages and applications. The choice of joining method will depend on factors such as the materials being joined, the type of bond required, and the specific application.
Quality Testing Methods for sheet metal joining and how to control the quality
Some common quality testing methods for sheet metal joining include:
1. Visual inspection: Inspect the joints for any visible defects such as gaps, cracks, or uneven welds.
2. Dye penetrant testing: This method involves applying a colored dye to the joint and then wiping it off to reveal any cracks or defects that may not be visible to the naked eye.
3. Ultrasonic testing: This method uses high-frequency sound waves to detect any internal defects in the joint.
4. X-ray inspection: This method uses X-rays to create detailed images of the joint, allowing for the detection of any internal defects.
To control the quality of sheet metal joining, it is important to implement the following steps:
1. Ensure proper training: Ensure that workers are properly trained in the welding and joining processes to avoid common mistakes and defects.
2. Establish quality control procedures: Implement specific procedures for inspecting and testing the joints at various stages of production.
3. Use high-quality materials: Use high-quality sheet metal and welding materials to ensure the durability and strength of the joints.
4. Regular maintenance: Regularly inspect and maintain welding equipment to ensure accurate and consistent joining.
By implementing these quality control measures and using appropriate testing methods, you can ensure the quality of sheet metal joining while minimizing defects and ensuring the reliability and strength of the finished product.
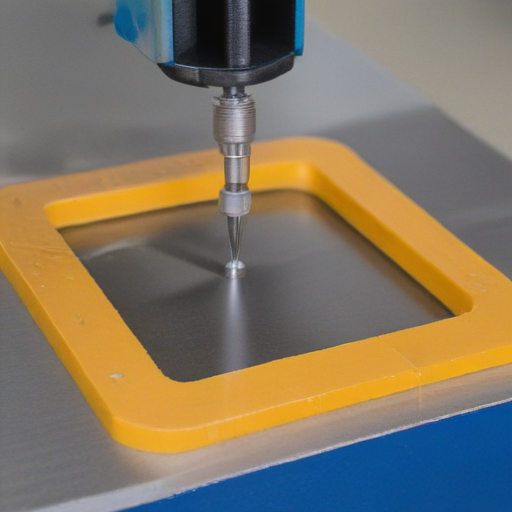
The Work Process and how to use sheet metal joining
Sheet metal joining is a common practice in metal fabrication, used to connect two or more pieces of sheet metal together. There are several methods of sheet metal joining, each with its own unique benefits and drawbacks. Some of the most common methods include welding, soldering, riveting, and fastening.
Welding is a highly effective method of joining sheet metal, where the two pieces are heated to melting point and fused together. This results in a strong, permanent bond that is ideal for structural applications. Soldering is a similar process, but uses a lower heat to join the metal pieces. This is commonly used for joining electronics and thin metal sheets.
Riveting involves using a rivet, a metal pin with a head on one end, to hold two pieces of metal together. The rivet is inserted through pre-drilled holes in the metal sheets, and then the end is deformed to secure the pieces in place. This method is quick and easy to use, but not as strong as welding.
Fastening is another common method of sheet metal joining, using screws, bolts, or other fasteners to hold the pieces together. This method is versatile and can be easily disassembled if needed, making it ideal for applications where maintenance or repair may be required.
In conclusion, sheet metal joining is an essential process in metal fabrication, with various methods available depending on the specific requirements of the project. It is important to carefully consider the desired strength, durability, and disassembly requirements when selecting a joining method for sheet metal. By choosing the appropriate joining method, you can ensure a strong and durable finished product.
sheet metal joining Importing questions including Cost,Supplier,Sample,Certification and Market
1. Cost: What is the cost of importing sheet metal joining equipment or materials? Are there any additional fees or charges to consider, such as customs duties or shipping costs?
2. Supplier: Who are the potential suppliers for sheet metal joining equipment or materials? What is their reputation in the industry and do they have a track record of delivering high-quality products?
3. Sample: Can we request a sample of the sheet metal joining equipment or materials before placing a bulk order? Is there a process for evaluating the sample for quality and reliability?
4. Certification: Are the sheet metal joining equipment or materials certified to meet specific industry standards or regulations? Can the supplier provide documentation or certification to verify the quality and safety of the products?
5. Market: What is the market demand for sheet metal joining equipment or materials in our target region? Are there any trends or developments in the industry that could impact the availability or pricing of these products?
In conclusion, importing sheet metal joining equipment or materials involves considerations such as cost, supplier reputation, sample evaluation, certification requirements, and market demand. It is important to conduct thorough research and due diligence to ensure the successful procurement of high-quality products at competitive prices.
How to find and select check reliable sheet metal joining manufacturers in China
1. Conduct thorough research online to find reputable sheet metal joining manufacturers in China. Look for companies with positive reviews, a strong track record of quality products, and certifications such as ISO 9001.
2. Reach out to industry contacts or trade associations for recommendations on reliable manufacturers in China for sheet metal joining.
3. Request quotes and samples from multiple manufacturers to compare pricing, lead times, and quality of work. Ensure that the manufacturers have experience in the type of sheet metal joining techniques you require.
4. Verify the manufacturers’ credentials, such as business licenses and certifications, to ensure they are reputable and comply with industry standards.
5. Visit the facilities of the shortlisted manufacturers to assess their production capabilities, equipment, and quality control processes.
6. Communicate clearly with the manufacturers regarding your requirements, specifications, and expectations for the sheet metal joining project.
7. Consider factors such as the manufacturer’s communication skills, responsiveness, and customer service when making your final selection.
Choosing a reliable sheet metal joining manufacturer in China requires thorough research, meticulous evaluation of options, and clear communication to ensure a successful partnership.
Background Research for sheet metal joining manufacturers Companies in China, use qcc.com archive.org importyeti.com
Sheet metal joining manufacturers in China are businesses that specialize in assembling and connecting metal parts to create various products and components. These manufacturers use a variety of techniques such as welding, soldering, riveting, and adhesive bonding to join sheet metal pieces together.
One way to find information on sheet metal joining manufacturers in China is to use qcc.com. This website provides listings of companies operating in China, including those involved in sheet metal fabrication and assembly. By searching on qcc.com, you can find contact information, company profiles, and customer reviews for different manufacturers in the sheet metal joining industry.
Another useful resource for researching sheet metal joining manufacturers in China is archive.org. This website archives old versions of websites, which can be helpful in tracking the history and evolution of different manufacturers in the industry. By looking at past versions of manufacturer websites, you can gain insight into their capabilities, services, and experience in sheet metal joining.
Importyeti.com is also a valuable tool for researching sheet metal joining manufacturers in China. This website provides data on import and export activities, allowing you to identify manufacturers that have a track record of supplying sheet metal products to international markets. By analyzing import data on importyeti.com, you can assess the reputation and reliability of different manufacturers in the sheet metal joining industry.
In conclusion, by utilizing resources such as qcc.com, archive.org, and importyeti.com, you can gather valuable information on sheet metal joining manufacturers in China. These websites offer insights into the capabilities, history, and reputation of different manufacturers, helping you make informed decisions when selecting a supplier for your sheet metal joining needs.
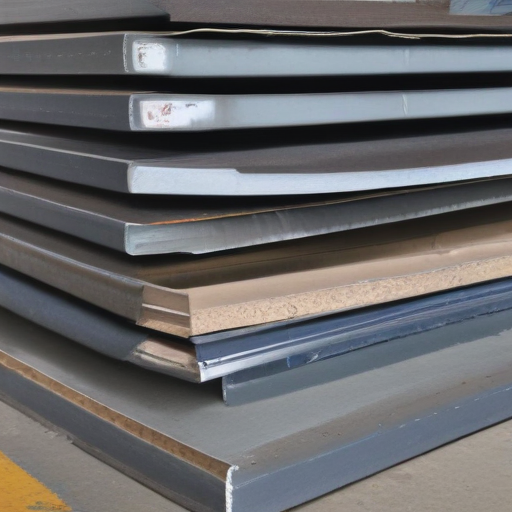
Price Cost Research for sheet metal joining manufacturers Companies in China, use temu.com and 1688.com
When researching prices and costs for sheet metal joining manufacturers in China, two popular websites to consider are temu.com and 1688.com. These platforms offer a wide range of suppliers and manufacturers specializing in sheet metal joining services.
On temu.com, you can find a variety of sheet metal joining manufacturers with detailed profiles, including information on their capabilities, certifications, and customer reviews. This allows you to compare different companies and their pricing structures to determine the most cost-effective option for your needs.
1688.com is a popular sourcing platform in China, offering a vast selection of sheet metal joining manufacturers and suppliers. You can search for specific products or services, compare prices, and negotiate directly with suppliers to get the best possible deal.
When conducting your research on these platforms, it’s essential to consider factors such as the type of sheet metal joining services offered, the quality of workmanship, turnaround times, and shipping costs. By exploring multiple options and gathering quotes from different manufacturers, you can make a well-informed decision to find the best price and cost for your sheet metal joining needs in China.
Shipping Cost for sheet metal joining import from China
When importing sheet metal joining products from China, the shipping cost can vary depending on several factors such as the weight and dimensions of the items, the shipping method chosen, and the location of the destination.
For smaller quantities of sheet metal joining products, air freight is a popular choice due to its speed and efficiency. The cost of air freight can range from $3 to $8 per kilogram, with a minimum charge typically applying for smaller shipments. It is important to note that air freight costs can increase significantly for larger or heavier items.
For larger quantities of sheet metal joining products, sea freight is a more cost-effective option. The cost of sea freight is typically calculated based on the volume of the shipment in cubic meters, with rates starting at around $300 per cubic meter. However, the transit time for sea freight can be longer compared to air freight.
It is also important to consider additional costs such as customs duties, taxes, and handling fees when calculating the total shipping cost. These charges vary depending on the value of the goods and the destination country.
To ensure a smooth and cost-effective shipping process, it is recommended to work with a reliable freight forwarder or shipping company that has experience in importing goods from China. They can provide guidance on the best shipping method for your specific needs and help navigate any customs requirements or regulations. Additionally, negotiating bulk discounts with shipping providers or consolidating shipments can help reduce shipping costs.
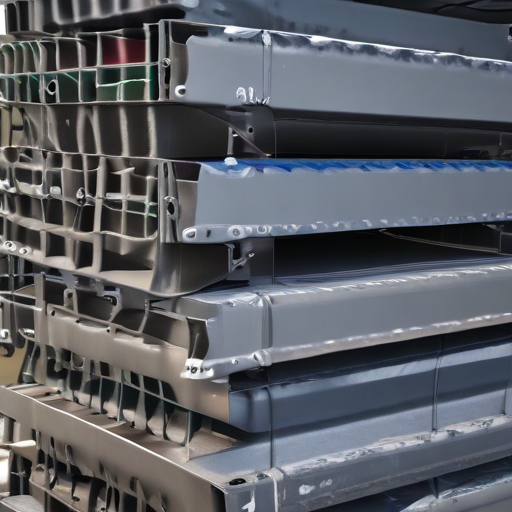
Compare China and Other sheet metal joining Markets: Products Quality and Price,Visible and Hidden Costs
China is the world’s largest producer of sheet metal joining products, offering a wide range of quality options at competitive prices. The sheer size of China’s manufacturing industry allows for economies of scale, leading to lower production costs and ultimately lower prices for consumers. However, there are concerns about the quality of Chinese-made products, with reports of substandard materials and workmanship.
On the other hand, other sheet metal joining markets, such as those in Europe or the United States, are known for their higher quality products. These markets often prioritize craftsmanship and precision, resulting in products that are more reliable and durable. This commitment to quality typically comes with a higher price tag, as the cost of labor and materials is generally higher in these regions.
In terms of visible costs, Chinese products often have a lower price point, making them more accessible to a wider range of consumers. However, hidden costs such as potential repairs or replacements due to lower quality could end up outweighing any initial savings. In contrast, while products from other markets may come with a higher upfront cost, their superior quality can lead to fewer maintenance issues and a longer lifespan, ultimately providing better value in the long run.
Overall, the decision between choosing sheet metal joining products from China or other markets will depend on the balance between quality and price that fits your specific needs. While Chinese products may offer affordability, it’s important to consider the potential hidden costs associated with lower quality. Meanwhile, products from other markets may be more expensive upfront but provide better long-term value through their superior craftsmanship and durability.
Custom Private Labeling and Branding Opportunities with Chinese sheet metal joining Manufacturers
Chinese sheet metal joining manufacturers offer custom private labeling and branding opportunities for businesses looking to expand their product line. By partnering with these manufacturers, companies can create unique products with their own branding, logo, and packaging.
With private labeling, businesses can customize sheet metal joining products to meet their specific needs and branding requirements. This includes choosing the material, finish, size, and color of the products, as well as adding their own logos and labels. This gives companies the flexibility to create products that align with their brand image and target market.
In addition, Chinese manufacturers can also provide branding opportunities for businesses looking to establish their own brand in the sheet metal joining industry. This includes developing a comprehensive branding strategy, creating marketing materials, and implementing branding initiatives to help businesses stand out in the market.
Overall, working with Chinese sheet metal joining manufacturers provides companies with the opportunity to create unique, high-quality products that are tailored to their brand and market. By leveraging private labeling and branding opportunities, businesses can differentiate themselves from competitors, increase brand recognition, and drive sales growth.
Tips for Procurement and Considerations when Purchasing sheet metal joining
When purchasing sheet metal joining materials, there are several important considerations to keep in mind to ensure a successful procurement process and high-quality end product. Here are some tips and considerations:
1. Material selection: The type of sheet metal joining method will dictate the material needed. Common materials for sheet metal joining include welding rods, rivets, screws, and adhesive bonding materials.
2. Budget: Consider your budget constraints when selecting sheet metal joining materials. Different options have different costs associated with them, so be sure to choose a material that fits within your budget without compromising on quality.
3. Strength requirements: Determine the required strength of the sheet metal joint based on the application and load-bearing requirements. Different joining methods offer varying levels of strength, so be sure to select a method that meets your specific needs.
4. Compatibility: Ensure that the sheet metal joining materials are compatible with the materials being joined. Some materials may react with each other, leading to corrosion or structural issues.
5. Ease of use: Consider the ease of use of the sheet metal joining method, especially if you will be performing the joining process in-house. Some methods require specialized equipment or training, so be sure to factor this into your decision-making process.
6. Environmental considerations: Consider the environmental impact of the sheet metal joining materials, such as the use of toxic chemicals or the generation of hazardous waste. Choose materials that are environmentally friendly and compliant with regulations.
7. Supplier reliability: Choose a reputable supplier for your sheet metal joining materials to ensure quality and reliability. Consider factors such as lead times, shipping costs, and customer service when selecting a supplier.
By keeping these tips and considerations in mind when purchasing sheet metal joining materials, you can ensure a successful procurement process and high-quality end product for your project.
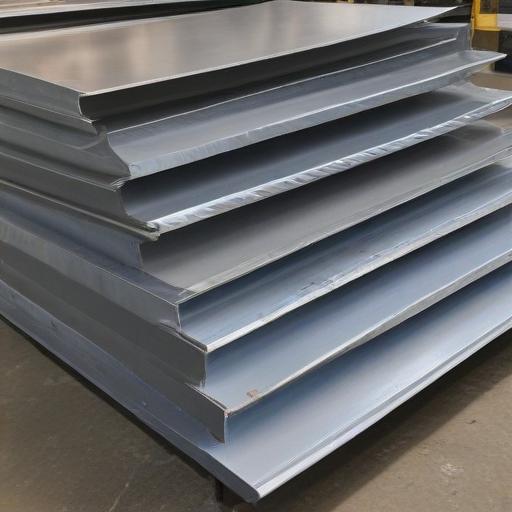
FAQs on Sourcing and Manufacturing sheet metal joining in China
Q: Why should I consider sourcing and manufacturing sheet metal joining in China?
A: China is known for its expertise in metal fabrication and large-scale manufacturing capabilities, offering competitive pricing and high-quality products. By sourcing sheet metal joining in China, you can benefit from cost savings, access to advanced technology, and streamlined production processes.
Q: How can I find a reliable manufacturer for sheet metal joining in China?
A: It is essential to conduct thorough research, request for quotations from multiple suppliers, and visit their facilities to assess their capabilities and quality control measures. Additionally, working with a sourcing agent or consulting firm with experience in the Chinese market can help you identify reputable manufacturers.
Q: What is the typical lead time for manufacturing sheet metal joining in China?
A: Lead times can vary depending on the complexity of the project, quantity ordered, and production capacity of the manufacturer. Generally, you can expect lead times to range from a few weeks to a few months. It is crucial to establish clear communication with your manufacturer to ensure timely delivery.
Q: What quality control measures are in place for sheet metal joining in China?
A: Reputable manufacturers in China often have stringent quality control processes in place, including material inspections, in-process inspections, and final inspections before shipment. Many manufacturers are also certified to international quality standards such as ISO 9001 to ensure consistently high-quality products.
Q: How can I ensure intellectual property protection when sourcing sheet metal joining in China?
A: It is essential to have a robust contract in place that includes confidentiality clauses, non-disclosure agreements, and intellectual property rights protection. Working with reputable manufacturers and utilizing legal resources such as patents or trademarks can also help safeguard your intellectual property rights.
Why contact sourcifychina.com get free quota from reliable sheet metal joining suppliers?
Sourcifychina.com provides a platform for businesses looking to connect with reliable sheet metal joining suppliers in China. By contacting Sourcifychina.com, businesses can easily get a free quota from these suppliers, saving time and effort in the sourcing process.
Using Sourcifychina.com to connect with sheet metal joining suppliers offers several benefits. Firstly, businesses can access a wide network of reputable suppliers, ensuring high-quality products and competitive pricing. This helps businesses find the best fit for their specific needs and requirements.
Additionally, Sourcifychina.com streamlines the sourcing process, making it faster and more efficient. Through the platform, businesses can easily communicate with suppliers, request quotes, and compare options, all in one convenient place. This saves time and eliminates the hassle of individually reaching out to multiple suppliers.
Overall, utilizing Sourcifychina.com to connect with reliable sheet metal joining suppliers is a smart choice for businesses looking to source products from China. By taking advantage of the free quota offer, businesses can quickly and easily find the right supplier for their needs, ultimately saving time and money in the sourcing process.