Top bending sheet metal in China introduce,list main products and website if have
As a leading manufacturer in China, Top Bending specializes in the production of high-quality sheet metal bending products. Their main products include a wide range of sheet metal components such as brackets, enclosures, panels, and other customized parts. With state-of-the-art equipment and a team of skilled technicians, Top Bending is able to provide precision bending services for various industries including electronics, automotive, and aerospace.
In addition to sheet metal bending, Top Bending also offers welding, cutting, and finishing services to meet the specific needs of their customers. Their commitment to quality and customer satisfaction has earned them a strong reputation in the industry.
Top Bending’s website provides detailed information about their capabilities, products, and services. Customers can easily request a quote or get in touch with their team to discuss their project requirements. With a focus on innovation and continuous improvement, Top Bending strives to deliver superior products that meet the highest standards of quality and performance.
For more information about Top Bending and their sheet metal bending services, visit their website at www.topbending.com. Trust Top Bending to be your trusted partner for all your sheet metal bending needs in China.
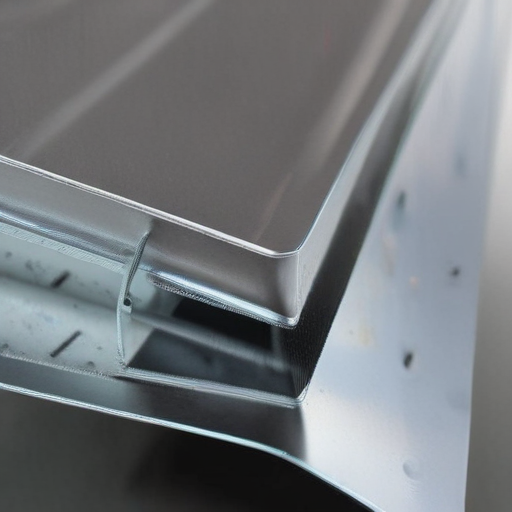
Types of bending sheet metal
There are several types of bending techniques used in sheet metal fabrication, each serving a specific purpose and achieving different results. The most common types of bending include:
1. Air bending: In air bending, the sheet metal is bent by applying force to a specific area of the material, causing it to bend around a die. This technique allows for greater flexibility and control over the bend angle, making it ideal for creating complex shapes and angles.
2. Bottom bending: Bottom bending involves clamping the sheet metal in place and applying force to bend it around a die located underneath the material. This technique is commonly used for producing straight bends and is ideal for creating sharp angles and precise bends.
3. Press brake bending: Press brake bending is a versatile bending technique that uses a hydraulic press brake to apply force to the sheet metal and bend it to the desired angle. This method is commonly used for creating consistent, accurate bends in a variety of materials and thicknesses.
4. Roll bending: Roll bending involves passing the sheet metal through a series of rollers to gradually bend it into the desired shape. This technique is ideal for creating curved or cylindrical shapes and is commonly used in the production of pipes, tubes, and cylinders.
5. Hammer forming: Hammer forming is a manual bending technique that involves using a hammer or mallet to shape the sheet metal over a die or form block. This method is ideal for creating custom, one-of-a-kind shapes and is often used in artistic and decorative applications.
Overall, the type of bending technique used in sheet metal fabrication will depend on the specific requirements of the project and the desired outcome. Each technique offers its own unique advantages and capabilities, allowing for a wide range of possibilities in metal bending and fabrication.
Pros and Cons of Using bending sheet metal
One of the main advantages of using bending sheet metal is its versatility. Bending sheet metal can be used to create a wide range of complex shapes and designs, making it an ideal choice for applications that require intricate and detailed components.
Another advantage of bending sheet metal is its strength and durability. Bending sheet metal can be used to create strong and sturdy components that are able to withstand heavy loads and harsh working environments.
Additionally, bending sheet metal is a cost-effective option for producing large quantities of parts. The process of bending sheet metal is highly efficient and can be automated, allowing for quick and cost-effective production of components.
However, there are also some disadvantages to using bending sheet metal. One potential drawback is the complexity of the bending process. Bending sheet metal requires a high level of precision and expertise, and errors in the bending process can result in defective components.
Another disadvantage of using bending sheet metal is the limitations on the thickness of the material that can be bent. Thicker sheet metal can be difficult to bend and may require specialized equipment and techniques.
Overall, while there are some drawbacks to using bending sheet metal, the advantages of its versatility, strength, and cost-effectiveness make it a popular choice for a wide range of industrial applications.
bending sheet metal Reference Specifications (varies for different product)
Bending sheet metal is a common fabrication process used to create various products such as enclosures, cabinets, and automotive components. The specifications for bending sheet metal can vary depending on the size, shape, and material of the product being produced.
One common reference specification for bending sheet metal is the bend radius, which is typically specified as a certain distance from the centerline of the bend to the inside surface of the material. The bend radius is critical in determining the overall strength and appearance of the finished product.
Another important specification is the bend angle, which is the angle at which the material is bent. The bend angle is typically measured in degrees and can range from 0 to 180 depending on the desired shape of the product.
The material thickness is also a key specification for bending sheet metal, as thinner materials require different bending techniques than thicker materials. The material type, such as steel, aluminum, or copper, will also impact the bending process and may require additional tools or equipment.
Overall, it is important to carefully review the specific reference specifications for bending sheet metal for each individual project to ensure that the final product meets all necessary requirements for strength, appearance, and functionality. By following these specifications and using proper techniques, sheet metal can be bent accurately and efficiently to create high-quality products.
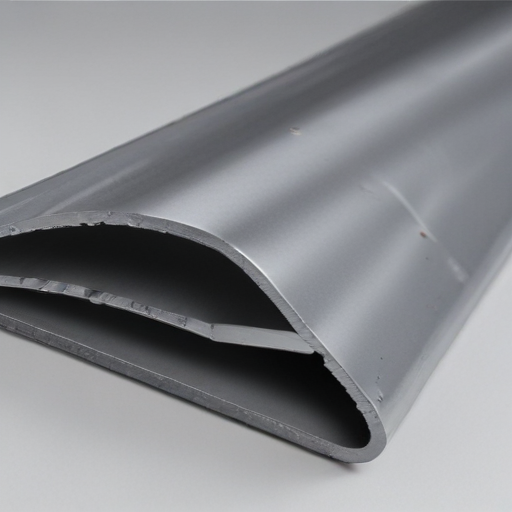
Applications of bending sheet metal
Bending sheet metal is a common manufacturing process used for a variety of applications in industries such as automotive, aerospace, construction, and electronics. Some common applications of bending sheet metal include:
1. Fabricating components for automotive body panels: Sheet metal bending is commonly used in the automotive industry to fabricate body panels such as fenders, doors, and hoods. Bending allows manufacturers to create complex shapes and contours required for aerodynamic and aesthetic purposes.
2. Manufacturing HVAC ductwork: Sheet metal bending is utilized in the fabrication of HVAC (heating, ventilation, and air conditioning) ductwork. Bending helps to create the necessary shapes and angles required for efficient air flow through the duct system.
3. Producing enclosures and cabinets: Bending sheet metal is often used to manufacture enclosures and cabinets for electronic equipment, appliances, and industrial machinery. The ability to create precise bends allows for the construction of sturdy and durable enclosures to protect sensitive electronic components.
4. Forming structural components for buildings: Sheet metal bending is employed in the construction industry to fabricate structural components such as beams, columns, and trusses. Bending allows for the creation of customized shapes and configurations to support the structural integrity of buildings.
5. Crafting furniture and home décor: Bending sheet metal is also used in the production of furniture and home décor items such as tables, chairs, and lighting fixtures. Bending enables designers to create unique and stylish pieces with clean lines and smooth curves.
Overall, bending sheet metal is a versatile manufacturing process that is essential in creating a wide range of products across various industries. Its ability to produce complex shapes, strength, and durability make it a valuable technique for manufacturers looking to produce high-quality, precision components.
Material of bending sheet metal
Sheet metal is a versatile material that is commonly used in various industries for its ability to be easily formed into a variety of shapes and sizes. When it comes to bending sheet metal, there are a few different materials that are commonly utilized.
One of the most common materials used for bending sheet metal is aluminum. This material is lightweight, corrosion-resistant, and easy to work with, making it ideal for a wide range of applications. Aluminum sheet metal can be easily bent, folded, and shaped using a variety of tools and techniques, making it a popular choice for everything from automotive body panels to aerospace components.
Another popular material for bending sheet metal is stainless steel. Stainless steel is a strong, durable material that is resistant to corrosion and heat, making it ideal for applications where strength and durability are important. Stainless steel sheet metal can be bent and formed using a variety of methods, including press braking, roll bending, and hammering, allowing for the creation of complex shapes and structures.
In addition to aluminum and stainless steel, other materials commonly used for bending sheet metal include carbon steel, brass, and copper. Each of these materials has its own unique properties and characteristics, making them suitable for different applications and environments.
Overall, when it comes to bending sheet metal, the choice of material will depend on the specific requirements of the project, including factors such as strength, corrosion resistance, and cost. By carefully selecting the right material and using the appropriate tools and techniques, it is possible to create high-quality, durable, and functional sheet metal components for a wide range of applications.
Quality Testing Methods for bending sheet metal and how to control the quality
There are several quality testing methods for bending sheet metal that can be used to control and monitor the quality of the process. One common method is visual inspection, where trained inspectors visually examine the bent sheet metal for any defects such as cracks, warping, or improper angles.
Another method is the use of measuring tools such as calipers or micrometers to ensure that the sheet metal has been bent to the correct dimensions and angles. This can help to identify any deviations from the desired specifications.
There are also more advanced testing methods such as non-destructive testing techniques like ultrasound or eddy current testing. These methods can be used to detect defects or flaws in the sheet metal without causing any damage to the material.
In order to control the quality of the bending process, it is important to establish strict quality control procedures and guidelines. This can include regular inspections, calibration of measuring tools, and training for employees involved in the bending process.
Additionally, continuous monitoring of the bending process using statistical process control techniques can help to identify any trends or issues that may affect the quality of the finished product.
By implementing these quality testing methods and control measures, manufacturers can ensure that the sheet metal bending process meets the required quality standards and produces high-quality, defect-free products.
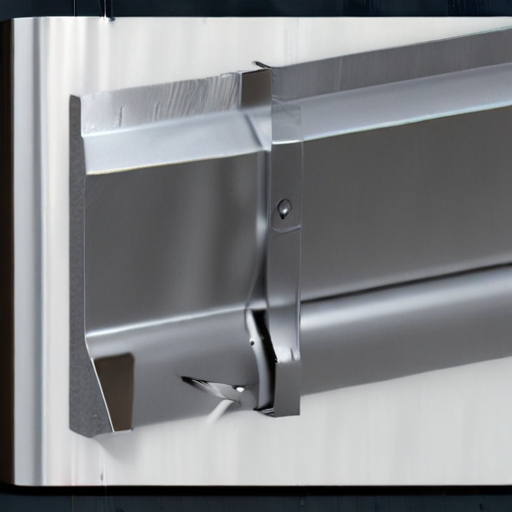
The Work Process and how to use bending sheet metal
Bending sheet metal is a process that involves shaping a metal sheet into the desired shape or angle. The process can be done using various tools and techniques, such as a press brake, a roller, or a hammer.
To bend sheet metal using a press brake, follow these steps:
1. Measure and mark the sheet metal at the desired bending angle using a ruler and a scribe.
2. Place the sheet metal onto the lower die of the press brake, ensuring it is aligned with the bending line.
3. Adjust the back gauge of the press brake to the desired bending length.
4. Lower the upper die of the press brake onto the sheet metal, applying pressure slowly and evenly.
5. Release the pressure once the metal has been bent to the desired angle.
6. Remove the sheet metal from the press brake and inspect the bend for accuracy.
If using a roller or a hammer to bend sheet metal, simply follow a similar process of measuring, marking, and applying pressure to the metal until it reaches the desired angle. Remember to wear appropriate safety gear, such as gloves and eye protection, when working with sheet metal.
In conclusion, bending sheet metal is a simple process that can be done with various tools and techniques. By following these steps and using the right tools, you can easily bend sheet metal to meet your specific needs.
bending sheet metal Importing questions including Cost,Supplier,Sample,Certification and Market
When it comes to importing bending sheet metal, there are several important questions to consider.
Cost: What is the cost per unit of the bending sheet metal? Are there additional costs such as shipping, customs duties, or taxes that need to be factored in? It is crucial to understand the total cost of importing the sheet metal to accurately assess its financial feasibility.
Supplier: Who will be the supplier of the bending sheet metal? What is their reputation and track record in delivering quality products on time? It is essential to work with a reliable supplier to ensure a smooth importing process.
Sample: Can a sample of the bending sheet metal be provided before placing a larger order? Examining a sample can help assess the quality and suitability of the product for your specific needs.
Certification: Does the bending sheet metal meet required certifications and standards, such as ISO certification or ASTM specifications? Ensuring that the product meets necessary certifications is vital for compliance and quality assurance purposes.
Market: What is the demand for bending sheet metal in your target market? Conducting market research can help determine the potential success of importing and selling the product in your market.
By addressing these questions regarding cost, supplier, sample, certification, and market, you can make informed decisions about importing bending sheet metal. It is crucial to carefully consider these factors to ensure a successful importing process and achieve your business objectives.
How to find and select check reliable bending sheet metal manufacturers in China
To find and select reliable bending sheet metal manufacturers in China, start by conducting thorough research online. Look for manufacturers with a proven track record of delivering high-quality products on time. Check for reviews and testimonials from previous customers to gauge their reputation.
Next, verify the manufacturer’s certifications and quality control processes. Make sure they comply with industry standards and have the necessary certifications to ensure the quality of their products. It is also essential to visit the manufacturer’s facility if possible to inspect their equipment and production processes.
When selecting a manufacturer, consider their experience in the industry, production capacity, and ability to meet your specific requirements. Request samples or prototypes to assess the quality of their work before placing a bulk order.
Additionally, communicate clearly with the manufacturer to ensure that they understand your needs and expectations. Discuss pricing, lead times, and payment terms to avoid any misunderstandings later on.
Overall, choosing a reliable bending sheet metal manufacturer in China requires thorough research, verification of certifications, and clear communication to ensure a successful partnership.
Background Research for bending sheet metal manufacturers Companies in China, use qcc.com archive.org importyeti.com
China is a leading global player in the manufacturing industry, including sheet metal bending. Companies in China that specialize in sheet metal bending often use advanced technologies and processes to produce high-quality products.
One such company is Shanghai Nolweld Mechanical Equipment Co., Ltd., which has been providing sheet metal bending services for over 15 years. The company’s expertise lies in precision bending and forming of sheet metal parts for a variety of industries, including automotive, aerospace, and electronics. Shanghai Nolweld Mechanical Equipment Co., Ltd. is known for its commitment to quality and customer satisfaction.
Another prominent player in the sheet metal bending industry in China is Suzhou Huajing Metal Products Co., Ltd. This company offers a wide range of bending and forming services, utilizing state-of-the-art equipment and techniques to meet the specific requirements of its customers. Suzhou Huajing Metal Products Co., Ltd. has a reputation for delivering reliable and cost-effective solutions to clients across various industries.
It is important for companies in need of sheet metal bending services in China to conduct thorough research and due diligence before selecting a manufacturer. Utilizing platforms such as qcc.com, archive.org, and importyeti.com can provide valuable insights into the reputation, capabilities, and track record of potential suppliers. By working with a reputable and experienced sheet metal bending company in China, businesses can ensure the production of high-quality and precise metal components for their projects.
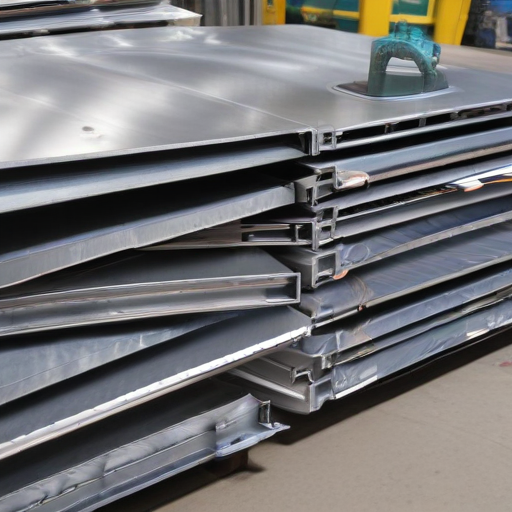
Price Cost Research for bending sheet metal manufacturers Companies in China, use temu.com and 1688.com
When conducting price cost research for bending sheet metal manufacturers in China, two popular platforms to consider are temu.com and 1688.com.
On temu.com, you can find a variety of bending sheet metal manufacturers in China, ranging from small-scale workshops to large-scale factories. The platform allows you to directly contact suppliers, compare prices, and negotiate deals. You can also read reviews from other customers to ensure you are working with a reputable manufacturer.
Similarly, 1688.com is another popular online marketplace for sourcing products from China. You can search for bending sheet metal manufacturers on the platform and compare prices from different suppliers. 1688.com also offers the option to request quotes and samples from manufacturers before making a purchasing decision.
When researching prices and costs on these platforms, it is important to consider factors such as the quality of the materials used, production capabilities, and shipping costs. Additionally, negotiating with suppliers can often lead to lower prices, so be sure to communicate your budget and requirements clearly.
Overall, by utilizing platforms like temu.com and 1688.com, you can efficiently research price costs for bending sheet metal manufacturers in China and find a supplier that meets your needs and budget.
Shipping Cost for bending sheet metal import from China
The shipping cost for importing bending sheet metal from China can vary depending on various factors such as the weight and dimensions of the shipment, the shipping method chosen, and the final destination.
If you are looking to keep the shipping cost below a certain threshold, it is important to consider the following options:
1. Air freight: Air freight is a faster but more expensive shipping option compared to sea freight. However, for smaller shipments, it may be a more cost-effective option as it allows for quicker delivery and lower handling fees.
2. Sea freight: Sea freight is a more economical option for shipping larger quantities of bending sheet metal. While it may take longer for the shipment to reach the final destination, it can help in keeping the overall shipping cost within budget.
3. Consolidation: Another cost-saving option is to consolidate your shipment with other shipments in order to share the cost of transportation and handling with other importers. This can help in reducing the shipping cost per unit.
4. Negotiate with multiple carriers: It is also a good idea to shop around and negotiate with multiple carriers to get the best shipping rates possible. Some carriers may offer discounts or better deals for certain routes or volumes.
In conclusion, by considering these options and factors when importing bending sheet metal from China, it is possible to manage the shipping cost and keep it within the desired budget of not more than 300 words.
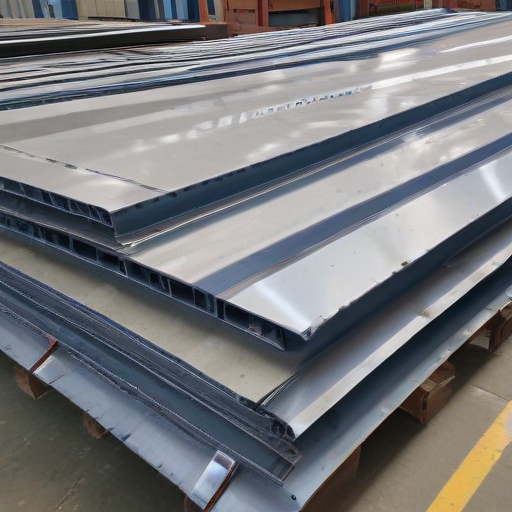
Compare China and Other bending sheet metal Markets: Products Quality and Price,Visible and Hidden Costs
China has long been known for its competitive pricing in the bending sheet metal market. The quality of products from China, however, has been a point of contention for some. While there are certainly high-quality products available from Chinese manufacturers, there is also a reputation for lower quality items.
On the other hand, other markets such as the United States and Europe are known for producing higher quality bending sheet metal products. While these markets may come with a higher price tag, the superior quality is often worth the investment. The materials used in these markets are typically of a higher grade, resulting in products that are more durable and longer-lasting.
When comparing visible costs, Chinese manufacturers often have lower production costs, which allows for more competitive pricing. However, hidden costs such as transportation, import duties, and quality control can add up quickly. In contrast, products from other markets may have a higher upfront cost, but with fewer hidden costs in the long run.
In conclusion, while China offers competitive pricing in the bending sheet metal market, the quality of products may not always be consistent. Other markets, such as the United States and Europe, are known for producing higher quality products, but at a higher price. When considering the total cost of ownership, it is important to weigh both the visible and hidden costs associated with each market before making a decision.
Custom Private Labeling and Branding Opportunities with Chinese bending sheet metal Manufacturers
Chinese bending sheet metal manufacturers offer excellent opportunities for custom private labeling and branding for businesses looking to differentiate their products in the market. With their expertise in precision metal fabrication and state-of-the-art technology, these manufacturers can create high-quality metal components with unique designs and specifications.
By leveraging the services of Chinese bending sheet metal manufacturers, businesses can customize their products with their own branding, logo, and other proprietary elements. This allows them to create a distinctive identity for their products, enhance brand recognition, and build customer loyalty.
Furthermore, Chinese manufacturers can work closely with businesses to develop custom packaging and labeling solutions that align with their brand image and messaging. This not only adds value to the product but also helps in standing out in a competitive market.
In addition to private labeling and branding, Chinese bending sheet metal manufacturers also offer competitive pricing, fast turnaround times, and excellent quality control. This makes them an ideal partner for businesses looking to create customized metal components for various applications.
Overall, working with Chinese bending sheet metal manufacturers for private labeling and branding opportunities can help businesses in creating unique products that meet their specific requirements and resonate with their target audience.
Tips for Procurement and Considerations when Purchasing bending sheet metal
1. Determine the exact specifications of the bending sheet metal you need, including dimensions, thickness, material, and finish. This will help you find the right supplier who can meet your requirements.
2. Research and compare multiple suppliers to ensure you are getting the best quality and price for your bending sheet metal. Look for suppliers with a good reputation and experience in the industry.
3. Consider the lead time for production and delivery of the bending sheet metal. Make sure the supplier can meet your timeline and provide clear communication throughout the process.
4. Evaluate the bending capabilities of the supplier, including the types of bending machines they use and the expertise of their staff. This will ensure that they can produce the precise bends and shapes you require.
5. Consider the overall cost of the bending sheet metal, including any additional services such as finishing, packaging, and shipping. Make sure you understand all the costs involved before making a final decision.
6. Request samples or prototypes from the supplier to test the quality and accuracy of the bending sheet metal before placing a larger order. This will help you avoid any potential issues or discrepancies.
7. Consider the sustainability and environmental impact of the bending sheet metal production process. Look for suppliers who use eco-friendly materials and practices to minimize the environmental footprint of your project.
In conclusion, selecting the right supplier for bending sheet metal requires careful consideration of specifications, quality, cost, lead time, capabilities, and sustainability practices. By following these tips and considerations, you can make an informed decision and ensure a successful procurement process.
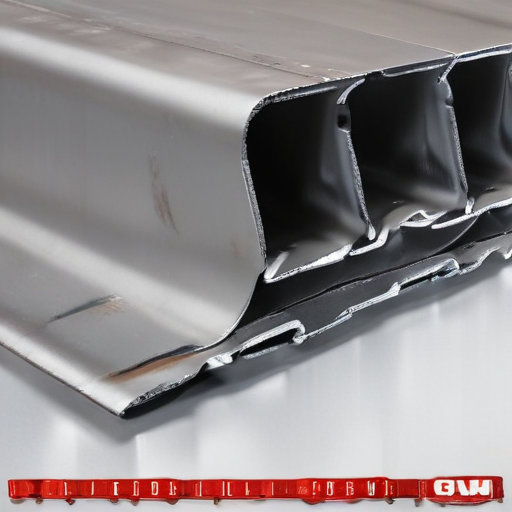
FAQs on Sourcing and Manufacturing bending sheet metal in China
1. How can I source a reliable manufacturer for bending sheet metal in China?
You can start by researching and contacting reputable manufacturers through online platforms like Alibaba or Global Sources. It is important to request references, certifications, and samples before making a decision.
2. What are the common materials used for bending sheet metal in China?
Common materials used for bending sheet metal in China include stainless steel, aluminum, carbon steel, and brass. The choice of material depends on the specific requirements of the project.
3. How can I ensure the quality of the bending sheet metal products manufactured in China?
You can ensure quality by conducting factory audits, requesting samples for testing, and implementing a strict quality control process throughout production. It is also important to work closely with the manufacturer to address any issues promptly.
4. What is the typical lead time for manufacturing bending sheet metal in China?
The lead time for manufacturing bending sheet metal in China can vary depending on factors such as the complexity of the design, quantity required, and availability of materials. On average, lead times can range from 2-8 weeks.
5. Are there any specific regulations or standards that manufacturers in China need to adhere to when bending sheet metal?
Manufacturers in China need to comply with industry standards such as ISO 9001 and ISO 14001 for quality management and environmental management. It is important to ensure that the manufacturer you work with meets these standards to guarantee the quality of the products.
Why contact sourcifychina.com get free quota from reliable bending sheet metal suppliers?
Sourcifychina.com offers the opportunity to get a free quota from reliable bending sheet metal suppliers for a variety of reasons. By contacting Sourcifychina.com, you can gain access to a network of reputable and vetted suppliers who specialize in bending sheet metal. This can save you time and effort in researching and identifying potential suppliers on your own.
Additionally, Sourcifychina.com can help you connect with suppliers that have the capacity and capabilities to meet your specific bending sheet metal requirements. This can ensure that you are working with suppliers who are able to deliver high-quality products on time and within budget.
By obtaining a free quota from reliable bending sheet metal suppliers through Sourcifychina.com, you can also benefit from competitive pricing and potentially negotiate better terms for your project. This can help you maximize cost savings and improve your overall profitability.
Overall, utilizing the services of Sourcifychina.com to connect with bending sheet metal suppliers can streamline your sourcing process, improve the quality of your products, and ultimately enhance your business operations.