Top brass casting in China introduce,list main products and website if have
Top brass casting in China is a leading manufacturer specializing in the production of high-quality brass castings. Their main products include brass valves, fittings, connectors, and other brass components. With a strong focus on precision engineering and quality control, they have earned a reputation for delivering reliable and durable brass products to their customers.
Top brass casting’s website features a comprehensive catalogue of their products, including detailed specifications and technical information. Customers can easily navigate through the site to find the products they need and place orders online. The website also provides valuable resources such as technical manuals, installation guides, and maintenance tips to help customers get the most out of their brass castings.
With a commitment to customer satisfaction and continuous improvement, top brass casting in China continues to innovate and expand their product line to meet the evolving needs of the market. They are dedicated to delivering exceptional quality brass products at competitive prices, and their experienced team of engineers and technicians ensure that every product meets the highest standards of quality and performance.
Overall, top brass casting in China is a reliable and trusted partner for businesses in need of high-quality brass castings. Their commitment to excellence, attention to detail, and customer-centric approach make them a preferred choice for customers worldwide. Visit their website to learn more about their products and services and see how they can meet your brass casting needs.
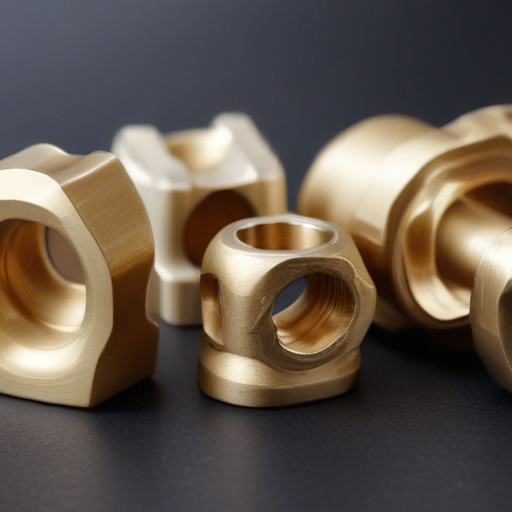
Types of brass casting
Brass casting is a popular method for creating a variety of components and products. There are several types of brass casting techniques used in the industry.
Sand casting is the most common method of brass casting. It involves creating a mold made of sand and then pouring molten brass into the mold. Once the brass has cooled and solidified, the sand mold is broken away to reveal the brass casting.
Investment casting, also known as lost-wax casting, is another popular method for brass casting. This process involves creating a wax pattern of the desired part, coating it in a ceramic shell, and then melting away the wax to leave a cavity. Molten brass is then poured into the cavity to create the final casting.
Continuous casting is a method used for mass producing brass components. In this process, molten brass is poured into a continuous mold and cooled as it travels through the mold. This results in a continuous length of brass that can be cut into smaller pieces.
Die casting is a precision casting method that involves injecting molten brass into a metal mold under high pressure. This method is often used for producing complex and detailed brass components.
Centrifugal casting is a method in which molten brass is poured into a rotating mold. The centrifugal force helps distribute the brass evenly within the mold, resulting in a uniform casting.
Each type of brass casting method has its advantages and disadvantages depending on the specific requirements of the project. However, all of these methods are widely used in the industry for creating high-quality brass components and products.
Pros and Cons of Using brass casting
Brass casting is a popular method of creating intricate and durable metal parts, objects, and sculptures. Like any manufacturing process, brass casting has its own set of pros and cons that should be considered before deciding to use this method.
Pros:
1. Cost-effective: Brass casting can be a cost-effective method of creating metal parts, as it allows for the production of complex shapes and designs at a relatively low cost.
2. Durability: Brass is known for its durability and resistance to corrosion, making it an ideal material for creating long-lasting products.
3. Intricate designs: Brass casting allows for the creation of intricate and detailed designs that may be difficult or impossible to achieve with other manufacturing methods.
4. Versatility: Brass casting can be used to create a wide range of products, from small components to large sculptures, making it a versatile manufacturing method.
5. Customization: Brass casting offers the ability to customize products to meet specific requirements or design preferences.
Cons:
1. Limitations on size: Brass casting may not be suitable for creating very large products or components, as the size of the molds used in the casting process is limited.
2. Time-consuming: The process of brass casting can be time-consuming, as it requires multiple steps including creating molds, pouring molten brass, and cooling the finished product.
3. Environmental impact: The process of brass casting can have a negative impact on the environment, as it requires the use of energy and produces waste materials.
4. Material costs: The cost of brass can fluctuate based on market prices, making it difficult to predict the overall cost of a brass casting project.
5. Skill and expertise required: Brass casting is a specialized skill that requires knowledge and experience to achieve high-quality results, which may make it challenging for beginners or small manufacturers.
In conclusion, brass casting can be a cost-effective and versatile method of creating durable and intricate metal products. However, it also has limitations in terms of size, cost, environmental impact, and required expertise. Careful consideration of these pros and cons is essential when deciding whether to use brass casting for a specific manufacturing project.
brass casting Reference Specifications (varies for different product)
Brass casting is a metalworking process that involves the creation of brass components through the pouring of molten brass into a mold. The process begins with the design of the component, which is then converted into a pattern that will be used to create the mold. The mold is typically made from sand, ceramic, or plaster, depending on the desired finish and complexity of the part.
When the mold is ready, the molten brass is poured into it and left to solidify. Once the brass has cooled and hardened, the mold is removed to reveal the finished brass component. The component may then undergo additional finishing processes, such as grinding, polishing, or plating, to achieve the desired final appearance.
Specifications for brass casting may vary depending on the specific requirements of the product being manufactured. Common reference specifications include ANSI B16.12 for lightweight copper and nickel alloy valves, ASTM B584 for copper and copper alloy sand castings for general applications, and ASTM B22 for brass ingots used for remelting.
Brass casting is a versatile manufacturing process that is commonly used to create a wide range of components, including valves, fittings, and decorative hardware. It offers several advantages, such as the ability to produce complex shapes with tight tolerances, as well as excellent dimensional stability and corrosion resistance. By following specific reference specifications and utilizing the appropriate materials and techniques, manufacturers can ensure the production of high-quality brass castings that meet the required standards and performance criteria.
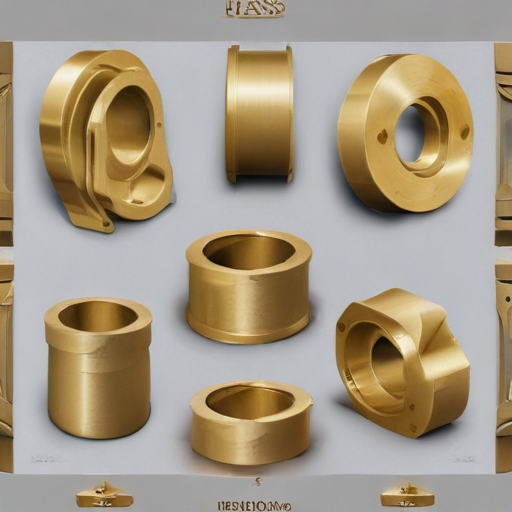
Applications of brass casting
Brass casting, a process that involves pouring molten brass into a mold to create complex shapes, plays a crucial role in various industries. One of the primary applications of brass casting is in the production of decorative items and art pieces. Brass’s golden hue, durability, and ability to be intricately molded make it a popular choice for creating statues, sculptures, and other ornamental pieces.
In the automotive industry, brass casting is commonly used for producing parts such as gears, brackets, and fittings. Brass’s corrosion resistance, strength, and malleability make it an ideal material for components that need to withstand harsh conditions and heavy loads. Additionally, brass parts are often used in plumbing applications due to their resistance to corrosion and ability to maintain tight seals.
Brass casting is also utilized in the manufacturing of musical instruments, particularly brass instruments such as trumpets, trombones, and tubas. The excellent resonance and sound quality of brass make it a preferred material for instrument construction. Moreover, the ability to create intricate designs and details through casting allows for the production of aesthetically pleasing instruments.
In the construction industry, brass casting is used to create various architectural elements, including door handles, hinges, and decorative fittings. Brass’s aesthetic appeal, durability, and ease of maintenance make it a popular choice for adding a touch of elegance to buildings and homes.
Overall, brass casting offers versatility and durability, making it a valuable process in a wide range of applications across different industries. Its ability to create detailed and complex shapes, coupled with its corrosion resistance and aesthetic appeal, makes it a preferred material for manufacturing a diverse array of products.
Material of brass casting
Brass casting is a metalworking process that involves pouring molten brass into a mold to create a specific shape or design. Brass is a versatile alloy that is primarily made up of copper and zinc, with small amounts of other metals such as lead or tin added for different properties.
The first step in brass casting is to create a mold in the desired shape. This can be done using a variety of materials, including sand, plaster, or metal. Sand casting is a common method for producing brass parts, where a pattern is pressed into a sand mixture to create a mold that is then filled with molten brass.
Once the mold is ready, the next step is to melt the brass. Brass has a relatively low melting point of around 900-1000 degrees Celsius, making it relatively easy to work with compared to other metals. The molten brass is then poured into the mold and left to cool and solidify.
After the brass has cooled, the mold is removed to reveal the finished brass casting. The casting may be further processed through cutting, grinding, or polishing to achieve the desired finish.
Brass castings are valued for their durability, corrosion resistance, and aesthetic appeal. They are commonly used in a wide range of applications, including decorative hardware, plumbing fixtures, musical instruments, and automotive parts.
In conclusion, brass casting is a versatile and cost-effective manufacturing process that allows for the production of complex and intricate brass parts. By carefully selecting the appropriate materials and techniques, high-quality brass castings can be achieved with precision and consistency.
Quality Testing Methods for brass casting and how to control the quality
There are several quality testing methods that can be used for brass casting, including visual inspection, dimensional inspection, chemical analysis, mechanical testing, and non-destructive testing.
Visual inspection involves observing the casting for any surface defects such as cracks, porosity, and impurities. Dimensional inspection involves measuring the casting to ensure it meets the specified dimensions. Chemical analysis involves testing the composition of the brass to ensure it meets the required specifications. Mechanical testing involves testing the strength and hardness of the brass casting. Non-destructive testing techniques such as ultrasound, X-ray, and dye penetrant testing can also be used to check for internal defects without damaging the casting.
To control the quality of brass casting, it is important to have stringent quality control procedures in place throughout the casting process. This includes properly preparing the mold, monitoring the pouring temperature and speed, ensuring proper cooling and solidification, and post-casting treatments such as heat treatment and surface finishing.
Regular maintenance of equipment and tools, as well as regular calibration of instruments, is essential to ensure accurate and consistent results. It is also important to train and educate personnel on proper casting techniques and quality control procedures.
By using these quality testing methods and implementing effective quality control measures, the quality of brass casting can be ensured and any defects can be detected and corrected early in the production process. This ultimately leads to higher quality brass castings and greater customer satisfaction.
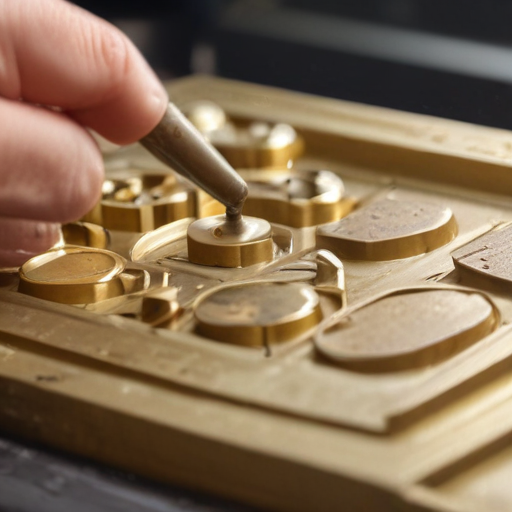
The Work Process and how to use brass casting
Brass casting is a process that involves creating metal objects by pouring molten brass into a mold. The mold is typically made of sand or ceramic, and is shaped in the desired form of the final product.
The process begins by melting the brass in a furnace at high temperatures. Once the brass is in a liquid state, it is poured into the mold through a sprue, which is a channel that allows the metal to flow evenly into the mold.
After the brass has cooled and solidified, the mold is removed to reveal the casting. The casting may then undergo additional finishing processes, such as grinding, polishing, or plating, to achieve the desired appearance and surface texture.
Brass casting is commonly used in the production of decorative items, such as hardware, statues, and jewelry. It is also used in industrial applications, such as in the manufacturing of valves, fittings, and other components.
To successfully carry out brass casting, it is important to have a well-designed mold that can withstand the high temperatures and pressure of the molten metal. Proper safety precautions should also be taken to prevent accidents and injuries during the casting process.
Overall, brass casting is a versatile and cost-effective method for producing high-quality metal objects. By following the correct procedures and using the right equipment, brass casting can be a successful and rewarding process for artisans and manufacturers alike.
brass casting Importing questions including Cost,Supplier,Sample,Certification and Market
When importing brass casting, there are several crucial factors to consider. First and foremost, the cost of the product is a key consideration. It is essential to source from a supplier that offers competitive pricing while maintaining high-quality standards.
Finding a reliable supplier is paramount in ensuring timely delivery and product quality. Conduct thorough research on potential suppliers, checking their track record, customer reviews, and production capabilities. It is also advisable to request samples from multiple suppliers to compare the quality and craftsmanship of their brass casting products.
Certifications play a significant role in guaranteeing the quality and compliance of the brass casting products. Look for suppliers that have relevant certifications such as ISO 9001 or any other industry-specific certifications. This ensures that the products meet international quality standards and have been manufactured under strict guidelines.
Understanding the market demand for brass casting products is vital in making informed import decisions. Conduct market research to identify potential opportunities and competition. Evaluate factors such as pricing, customer preferences, and distribution channels to determine the market potential for brass casting products.
In conclusion, importing brass casting products involves careful consideration of cost, supplier reliability, sample evaluation, certification requirements, and market analysis. By taking these factors into account, importers can make informed decisions that ensure a successful import process.
How to find and select check reliable brass casting manufacturers in China
To find and select reliable brass casting manufacturers in China, the following steps can be taken:
1. Do thorough research: Conduct an online search for brass casting manufacturers in China. Look for manufacturers with a good reputation and positive reviews from previous customers.
2. Check certifications: Verify if the manufacturers have necessary certifications such as ISO 9001:2015, which ensures quality control and management systems are in place.
3. Request samples: Ask for samples of their brass casting products to assess the quality of their workmanship and materials.
4. Visit the factory: If possible, arrange a visit to the manufacturing facility to see firsthand the production process and conditions.
5. Check customer references: Request references from the manufacturer and contact previous clients to inquire about their experiences working with them.
6. Compare quotes: Obtain quotes from multiple manufacturers and compare pricing, lead times, and other terms to ensure you are getting the best value for your money.
7. Communication: Ensure clear and timely communication with the manufacturer to address any concerns or specifications.
By following these steps, you can find and select a reliable brass casting manufacturer in China that meets your quality standards and requirements.
Background Research for brass casting manufacturers Companies in China, use qcc.com archive.org importyeti.com
When looking for brass casting manufacturers in China, some useful resources to consider are qcc.com, archive.org, and importyeti.com. These websites provide valuable information and insights into various companies in the brass casting industry in China.
Qcc.com is a comprehensive business directory that allows users to search for specific companies, products, and services in China. It provides detailed company profiles, contact information, and customer reviews, making it a valuable tool for researching brass casting manufacturers in China.
Archive.org is a digital archive that stores historical snapshots of websites, allowing users to track changes and developments in the brass casting industry over time. By accessing archived websites of different brass casting manufacturers in China, researchers can gain a better understanding of their evolution and market positioning.
Importyeti.com is a database of import and export data that provides insights into the trading activities of various companies. By analyzing the import and export data of brass casting manufacturers in China, researchers can identify key players, market trends, and potential business opportunities in the industry.
Overall, leveraging these resources can help in conducting background research on brass casting manufacturers in China, enabling informed decision-making and selection of the right supplier for specific business needs.
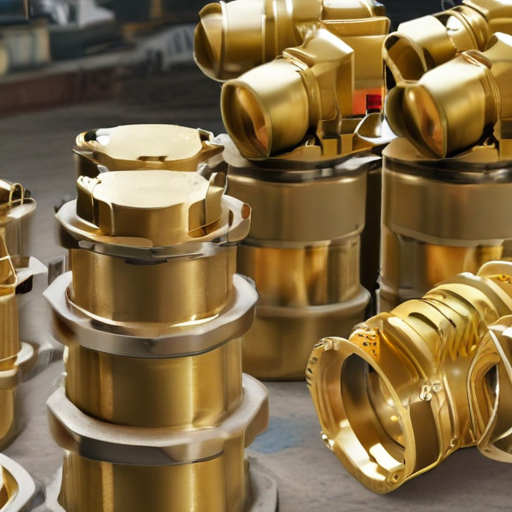
Price Cost Research for brass casting manufacturers Companies in China, use temu.com and 1688.com
Temu.com and 1688.com are two popular platforms for sourcing products from China, including brass casting manufacturers. By browsing these websites, you can easily find information on the prices and costs associated with brass casting services offered by various companies.
On temu.com, you can view detailed product listings from different brass casting manufacturers, along with their prices and minimum order quantities. This allows you to compare prices and find the most cost-effective option for your needs. Additionally, you can contact suppliers directly through the platform to negotiate prices or request a custom quote.
Similarly, on 1688.com, you can search for brass casting manufacturers and view their product listings to get an idea of the price range for different services. The platform also provides information on each supplier’s production capacity, certifications, and other relevant details that can help you make an informed decision.
When researching prices and costs for brass casting services on these platforms, it’s essential to consider factors such as the quality of the products, the supplier’s reputation, and any additional fees or charges that may apply. By carefully reviewing the information available on temu.com and 1688.com, you can find a reliable brass casting manufacturer in China that offers competitive prices and meets your specific requirements.
Shipping Cost for brass casting import from China
When importing brass casting from China, one of the key factors to consider is the shipping cost. The shipping cost for brass casting from China can vary depending on various factors such as the weight of the casting, the volume of the shipment, the mode of transportation, and the shipping route.
Typically, brass casting shipments from China are transported via sea freight or air freight. Sea freight is generally the more cost-effective option for large shipments of brass casting due to lower cost per unit weight. However, sea freight can take longer than air freight, so it is important to consider the shipping timeline when choosing the mode of transportation.
The cost of shipping brass casting from China via sea freight is calculated based on the volume or weight of the shipment. The cost can range from a few hundred dollars to several thousand dollars, depending on the quantity of brass casting being imported.
On the other hand, air freight is a faster but more expensive option for shipping brass casting from China. The cost of air freight is generally higher than sea freight due to the quicker delivery time and the higher cost of air transportation.
When importing brass casting from China, it is essential to work with a reliable shipping company that can provide competitive rates and excellent service. They can help you determine the most cost-effective shipping method based on your specific needs and requirements.
In conclusion, the shipping cost for brass casting import from China can vary based on several factors, including the mode of transportation, shipment volume, and shipping route. It is crucial to carefully consider these factors and work with a reputable shipping company to ensure a smooth and cost-effective shipping process.
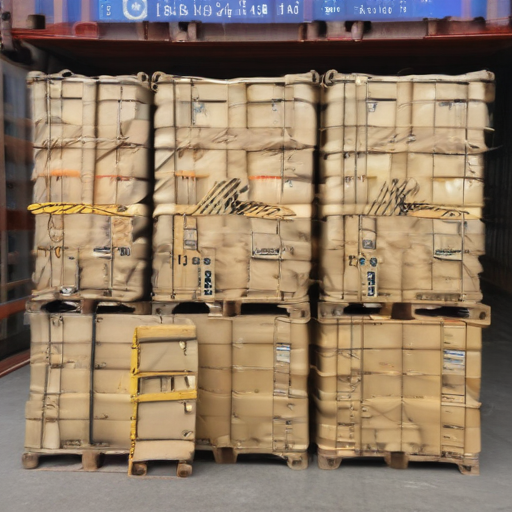
Compare China and Other brass casting Markets: Products Quality and Price,Visible and Hidden Costs
China is one of the largest brass casting markets in the world, known for producing high-quality products at competitive prices. The quality of brass casting products in China is generally good, with manufacturers using advanced technology and skilled labor to achieve consistent results. However, the quality can vary depending on the manufacturer, so it is important for buyers to conduct thorough research before making a purchase.
In terms of price, Chinese brass casting products are often more affordable compared to those from other markets. This is due to factors such as lower labor costs and economies of scale, allowing Chinese manufacturers to offer competitive prices to their customers. Despite the lower prices, many Chinese manufacturers are still able to maintain high standards of quality, making them a popular choice for buyers around the world.
When it comes to visible and hidden costs, buyers should be aware of potential issues such as transportation and import tariffs when sourcing brass casting products from China. While the initial purchase price may be lower, these additional costs can add up and affect the overall cost of the product. It is important for buyers to factor in these costs when evaluating different suppliers and making a final decision.
Overall, China offers a combination of high-quality brass casting products at competitive prices, making it a popular choice for buyers looking for a cost-effective solution. However, buyers should be aware of potential additional costs and research manufacturers carefully to ensure they are getting the best value for their money.
Custom Private Labeling and Branding Opportunities with Chinese brass casting Manufacturers
For businesses looking to establish their own brand and stand out in the market, partnering with Chinese brass casting manufacturers for custom private labeling and branding opportunities can be a strategic choice. These manufacturers have the expertise and resources to produce high-quality brass products that can be customized to your specifications.
With custom private labeling, you can add your logo, company name, and other branding elements to the products, giving them a unique identity that reflects your brand image. This can help increase brand recognition and customer loyalty.
Furthermore, by working with Chinese brass casting manufacturers, you can benefit from cost-effective production processes and competitive pricing. This can give you a competitive edge in the market and help you maximize your profitability.
In addition, collaborating with Chinese manufacturers can also offer you access to a wide range of brass casting options, from traditional to modern designs. This allows you to create products that align with your brand aesthetic and meet the preferences of your target market.
Overall, partnering with Chinese brass casting manufacturers for custom private labeling and branding opportunities can provide your business with the tools and resources needed to succeed in the competitive marketplace. By leveraging their expertise and capabilities, you can create custom-branded products that resonate with your customers and elevate your brand presence.
Tips for Procurement and Considerations when Purchasing brass casting
1. Define your requirements: Before purchasing brass casting, it is important to clearly define your requirements such as the quantity, quality standards, dimensions, and any special requirements. This will ensure that you source the right product that meets your needs.
2. Research suppliers: Conduct thorough research on potential suppliers of brass casting. Look for suppliers with a good reputation in the industry, experience in producing brass casting, and a track record of delivering quality products on time.
3. Quality control: Ensure that the supplier has quality control measures in place to ensure that the brass casting meets your specifications and quality standards. Ask for samples or references to verify the quality of their products.
4. Cost considerations: Compare quotes from different suppliers to ensure that you are getting a competitive price for the brass casting. However, do not compromise on quality for the sake of cost savings.
5. Lead times: Consider the lead times provided by the supplier for producing and delivering the brass casting. Make sure that the supplier can meet your timeline requirements.
6. Communication: Establish clear communication channels with the supplier to ensure that there are no misunderstandings or delays in the procurement process. Regular communication can help in resolving any issues that may arise during the procurement process.
7. Material selection: Consider the type of brass material used for the casting as it can impact the quality and performance of the product. Discuss with the supplier the best material option based on your requirements.
8. Post-sales support: Inquire about the supplier’s after-sales support and warranty policies for the brass casting. It is important to have assurance that the supplier will address any issues or concerns that may arise after the purchase.
Overall, thorough research, clear communication, and attention to quality and cost considerations are essential when purchasing brass casting. By following these tips and considerations, you can ensure a smooth and successful procurement process.
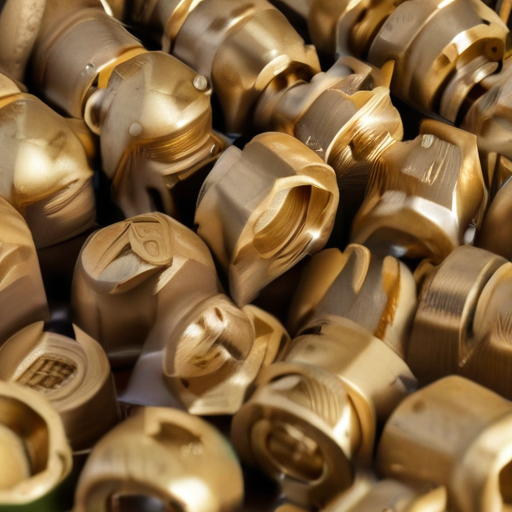
FAQs on Sourcing and Manufacturing brass casting in China
1. How can I find a reliable brass casting manufacturer in China?
To find a reliable brass casting manufacturer in China, you can start by conducting thorough research online and checking for customer reviews and ratings. Additionally, attending trade shows or reaching out to sourcing agents can also help connect you with reputable manufacturers.
2. What factors should I consider when sourcing brass casting in China?
When sourcing brass casting in China, consider factors such as the manufacturer’s experience in the industry, quality control measures, production capacity, pricing, and communication abilities. It is also important to assess the manufacturer’s compliance with environmental and ethical standards.
3. How can I ensure the quality of brass casting produced in China?
To ensure the quality of brass casting produced in China, you can request samples for evaluation, conduct factory visits to inspect the production processes, and implement quality control measures such as product testing and inspections. Additionally, establishing clear communication channels with the manufacturer can help address any quality concerns promptly.
4. What are the common challenges when manufacturing brass casting in China?
Common challenges when manufacturing brass casting in China may include language barriers, cultural differences, logistic issues, and delays in production or shipping. It is essential to have a detailed contract in place, clearly outlining expectations and specifications to mitigate potential challenges.
5. How can I monitor the manufacturing process of brass casting in China?
You can monitor the manufacturing process of brass casting in China by regularly communicating with the manufacturer, requesting progress reports, and conducting quality inspections at different stages of production. Utilizing project management tools and software can also help track the progress of the manufacturing process effectively.
Why contact sourcifychina.com get free quota from reliable brass casting suppliers?
Sourcifychina.com is a trusted platform that connects businesses with reliable brass casting suppliers in China. By contacting Sourcifychina.com, you can get a free quota from these suppliers, allowing you to easily compare prices, quality, and lead times.
Using Sourcifychina.com to connect with brass casting suppliers ensures that you are working with reputable and trustworthy manufacturers. This can help to mitigate the risks often associated with sourcing products from overseas, such as poor quality, delayed deliveries, or hidden fees.
By obtaining a free quota from these suppliers through Sourcifychina.com, you can make informed decisions about which supplier is the best fit for your needs. This can ultimately save you time and money by ensuring that you are working with a reliable partner that can meet your production requirements.
Sourcifychina.com offers a hassle-free way to connect with brass casting suppliers in China, making the sourcing process simple and efficient. By taking advantage of their services and getting a free quota from reputable suppliers, you can streamline your sourcing efforts and find the perfect partner for your brass casting needs.