Top casted brass in China introduce,list main products and website if have
Some of the top casted brass manufacturers in China include Luyi Forge Ltd, Qingdao Tianluli Industrial Co., Ltd, and Ningbo Joyometal Industrial Co., Ltd.
Luyi Forge Ltd specializes in the production of brass castings for a wide range of industries including automotive, machinery, and construction. Their main products include brass fittings, brass valves, and brass hardware. You can find more information about their products and services on their website at www.luyiforge.com.
Qingdao Tianluli Industrial Co., Ltd is another leading manufacturer of casted brass products in China. They offer a variety of brass casting parts such as brass handles, brass knobs, and brass hinges. For more details about their products and capabilities, you can visit their website at www.tlcasting.com.
Ningbo Joyometal Industrial Co., Ltd is known for producing high-quality brass castings for various applications. Their product range includes brass connectors, brass bushings, and brass brackets. To learn more about their products and offerings, you can visit their website at www.joyometal.com.
These top casted brass manufacturers in China offer a wide range of products for different industries and applications. Customers can expect high-quality brass castings that meet their specific requirements and standards.
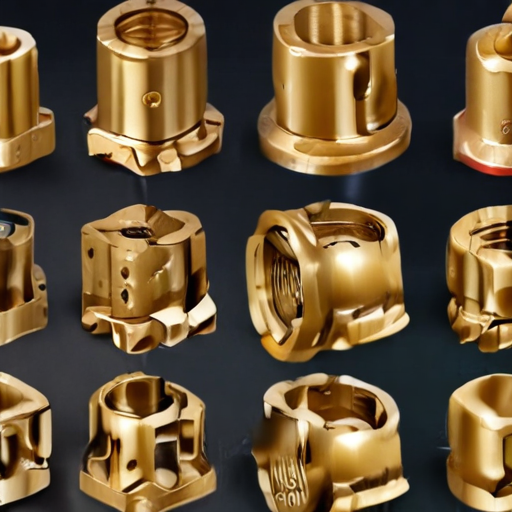
Types of casted brass
There are several types of casted brass that are commonly used in a variety of applications. One of the most common types is red brass, which is made up of approximately 85% copper and 15% zinc. Red brass is known for its reddish color and is often used in plumbing fixtures, electrical components, and decorative hardware.
Another type of casted brass is yellow brass, which has a higher zinc content than red brass, typically around 40-45%. Yellow brass is a popular choice for musical instruments, floor drains, and automotive parts due to its bright yellow color and corrosion resistance.
Naval brass is a type of casted brass that contains approximately 60% copper, 39% zinc, and 1% tin. This type of brass is commonly used in marine applications due to its resistance to corrosion in saltwater environments.
Gunmetal is another type of casted brass that contains approximately 88% copper, 10% tin, and 2% zinc. Gunmetal is known for its high strength and durability, making it a popular choice for components in firearms and other mechanical applications.
Casting brass is a versatile material that can be used in a wide range of industries and applications. By understanding the different types of casted brass available, manufacturers can choose the best type for their specific needs and requirements.
Pros and Cons of Using casted brass
Casted brass, also known as cast brass, is a common type of brass that is formed by pouring molten brass into a mold and allowing it to cool and solidify. This manufacturing process gives casted brass several advantages and disadvantages compared to other types of brass.
Pros:
1. Cost-effective: Casted brass is relatively inexpensive to produce, making it a cost-effective material for a variety of applications.
2. Design flexibility: The casting process allows for intricate and complex shapes to be easily formed, giving designers more freedom in their creations.
3. Durability: Casted brass is known for its strength and durability, making it a long-lasting material for use in a wide range of applications.
4. Corrosion resistance: Brass is naturally resistant to corrosion, making casted brass an ideal material for outdoor or high-moisture environments.
5. Aesthetic appeal: Brass has a warm, golden hue that is aesthetically pleasing and adds a touch of elegance to any product or design.
Cons:
1. Porosity: The casting process can result in porosity in the material, which may weaken its structure and make it susceptible to cracking or breakage.
2. Inconsistency: Casted brass products may have variations in density and composition, leading to inconsistencies in the material’s properties.
3. Machinability: Casted brass can be difficult to machine and may require specialized equipment and skills to work with effectively.
4. Limited availability: Casted brass is not as readily available as other forms of brass, which may limit its use in certain applications.
5. Environmental impact: The casting process can be resource-intensive and may have a higher environmental impact compared to other manufacturing methods.
In conclusion, casted brass offers a unique combination of cost-effectiveness, design flexibility, and durability, but it also comes with drawbacks such as porosity, inconsistency, and limited availability. It is important for designers and manufacturers to carefully consider these factors when deciding whether casted brass is the right material for their project.
casted brass Reference Specifications (varies for different product)
Casted brass is a type of brass material that is produced through the process of casting, which involves pouring molten brass into a mold to create a desired shape. Casted brass has a number of specifications that must be followed in order to ensure that the final product meets the necessary standards and requirements.
One key specification for casted brass is its composition. The composition of casted brass typically includes a combination of copper and zinc, with varying ratios depending on the specific requirements of the final product. The composition of casted brass can also include small amounts of other elements such as lead, tin, and aluminum to enhance certain properties of the material.
Another important specification for casted brass is its physical properties, including its hardness, strength, and corrosion resistance. Casted brass is known for its excellent machinability, making it a popular choice for a wide range of applications. In addition, casted brass has good thermal and electrical conductivity, as well as a high resistance to corrosion, making it suitable for use in a variety of environments.
Casted brass also has specific dimensional tolerances that must be met in order to ensure that the final product is of high quality. This includes tolerances for dimensions such as length, width, and thickness, as well as surface finish requirements to ensure that the casted brass has a smooth and uniform appearance.
Overall, casted brass is a versatile material that is used in a wide range of applications due to its excellent mechanical and physical properties. By adhering to the specific specifications for casted brass, manufacturers can ensure that their final products meet the necessary standards and provide reliable performance for their intended purposes.
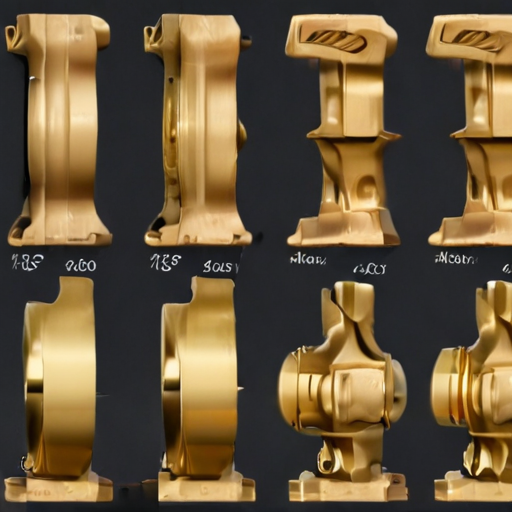
Applications of casted brass
Casted brass is a versatile material that is commonly used in various applications due to its strength, durability, and aesthetic appeal. One of the most common uses of casted brass is in the production of decorative items such as door knobs, hinges, and furniture accents. The beautiful golden hue of brass adds a touch of elegance and sophistication to any space.
In addition to decorative items, casted brass is also commonly used in the production of musical instruments. Brass instruments such as trumpets, trombones, and saxophones are often made with casted brass due to its ability to produce rich and warm tones. The malleability of brass also allows for intricate designs to be created, enhancing the overall appearance of the instrument.
Another important application of casted brass is in the plumbing industry. Brass fittings and valves are commonly used in plumbing systems due to their corrosion resistance and durability. Brass is also a good conductor of heat, making it an ideal material for use in heating and cooling systems.
Furthermore, casted brass is often used in the production of marine hardware and fittings due to its resistance to corrosion in saltwater environments. Items such as boat cleats, propellers, and portholes are commonly made from brass to withstand the harsh conditions of the sea.
Overall, casted brass is a versatile material that is used in various applications ranging from decorative items to musical instruments, plumbing fixtures, and marine hardware. Its strength, durability, and aesthetic appeal make it a popular choice for many industries.
Material of casted brass
Casting brass is a common manufacturing process used to create a wide range of brass components with various complex shapes. Brass, a combination of copper and zinc, is often chosen for its desirable properties such as high strength, corrosion resistance, and malleability.
The process of casting brass involves melting the brass in a crucible or furnace until it reaches a molten state. The molten brass is then poured into a mold cavity, which is typically made of sand or ceramic material. The brass cools and solidifies within the mold, taking on the desired shape of the component being produced.
Once the brass has solidified, the mold is removed, and any excess material is trimmed or machined off. The resulting brass casting can then undergo additional processing, such as finishing, polishing, or plating, to achieve the desired final appearance and surface finish.
Casting brass offers several advantages, including the ability to create intricate and detailed shapes, cost-effectiveness for large production runs, and the ability to produce components with consistent dimensions and quality. However, there are some limitations to casting brass, such as the need for skilled operators, the potential for porosity or other defects in the final casting, and the limitations on the size and complexity of the parts that can be produced.
Overall, casting brass is a versatile and widely used manufacturing process for creating a wide range of components in industries such as automotive, aerospace, plumbing, and construction. By carefully controlling the casting process and quality of the materials used, manufacturers can produce high-quality brass components that meet the requirements of their specific applications.
Quality Testing Methods for casted brass and how to control the quality
There are several quality testing methods that can be used for casted brass, including visual inspection, dimensional inspection, chemical analysis, and mechanical testing. Visual inspection involves examining the surface of the brass for any defects such as cracks, porosity, or surface irregularities. Dimensional inspection ensures that the casting meets the specified dimensions and tolerances. Chemical analysis can be used to verify the composition of the brass and ensure it meets industry standards. Mechanical testing involves testing the strength and hardness of the brass to ensure it is suitable for its intended application.
To control the quality of casted brass, it is important to implement a comprehensive quality control program that includes regular inspections and testing at various stages of the manufacturing process. This can help identify any defects or inconsistencies early on and prevent them from affecting the final product. In addition, proper training and supervision of personnel involved in the casting process can help ensure that best practices are followed and quality standards are met. It is also important to maintain accurate records of all testing and inspection results to track the quality of the casted brass over time and identify any trends or patterns that may indicate issues with the manufacturing process. Continuous improvement efforts, such as implementing new technologies or process improvements, can also help enhance the quality of casted brass products.
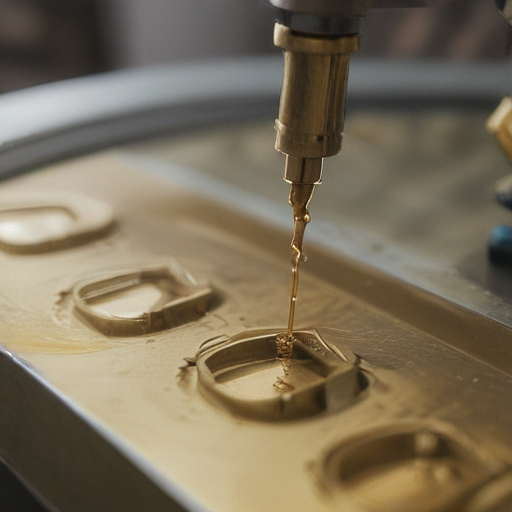
The Work Process and how to use casted brass
Casted brass is a versatile material that can be used in various applications, including the production of hardware, decor pieces, and musical instruments. The work process of using casted brass involves several steps to ensure a high-quality end product.
First, the brass is melted in a furnace at high temperatures to achieve a liquid state. The molten brass is then poured into a mold, which is typically made of sand or ceramic. The mold is designed to create the desired shape of the final product.
After the brass has cooled and solidified in the mold, the casting is removed and any excess material is trimmed away. The casting may then undergo further processing, such as polishing, plating, or machining, to achieve the desired finish and dimensions.
When working with casted brass, it is important to consider its unique properties, such as its strength, corrosion resistance, and malleability. It is also important to follow proper safety precautions, such as using protective gear and working in a well-ventilated area when melting the brass.
Overall, the work process of using casted brass involves melting the brass, pouring it into a mold, removing the casting, and finishing the product. By following these steps and being mindful of the material’s properties, you can create high-quality brass products for various applications.
casted brass Importing questions including Cost,Supplier,Sample,Certification and Market
Importing casted brass can be a profitable venture, but there are some important factors to consider before making a decision.
Cost is a crucial aspect when importing any product. It is important to research the cost of sourcing the brass from different suppliers, as well as the shipping and import taxes that may be involved. This will help in determining the overall cost and potential profit margin for your business.
Supplier selection is also critical when importing brass. It is recommended to work with reputable suppliers who have a track record of delivering quality products on time. Conducting thorough research and possibly visiting the supplier in person can help ensure a successful partnership.
Obtaining a sample of the brass before placing a bulk order is essential to verify the quality and suitability of the product for your market. This will also help in identifying any potential issues early on and avoid surprises once the full order is delivered.
Certification is another important consideration when importing brass. Ensuring that the product meets the required industry standards and regulations will help in avoiding any legal or quality issues down the line. Look for suppliers who can provide certification documents for their products.
Lastly, it is crucial to research the market demand for casted brass in your target region. Understanding the competition, pricing trends, and potential customers will help in developing a successful importing strategy.
In conclusion, importing casted brass can be a lucrative business opportunity, but it requires careful consideration of cost, supplier selection, sample testing, certification, and market research to ensure success.
How to find and select check reliable casted brass manufacturers in China
When looking for reliable casted brass manufacturers in China, it is important to do thorough research and follow these steps:
1. Utilize online resources such as Alibaba, Global Sources, or Made-in-China to search for potential manufacturers. Look for companies that have a good reputation and positive reviews from past customers.
2. Contact the manufacturers directly to inquire about their experience in casting brass, their production capacity, quality control measures, and any certifications they may have.
3. Request samples of their products to evaluate the quality of their casted brass and ensure it meets your specifications.
4. Ask for references from other customers who have worked with the manufacturer to get feedback on their reliability and performance.
5. Consider visiting the manufacturer’s facility in person to see their production process and ensure they have the capabilities to meet your requirements.
6. Compare quotes from multiple manufacturers to ensure you are getting a competitive price without compromising on quality.
7. Choose a manufacturer that has a proven track record of delivering high-quality casted brass products on time and within budget.
By following these steps, you can find and select a reliable casted brass manufacturer in China that meets your needs and exceeds your expectations.
Background Research for casted brass manufacturers Companies in China, use qcc.com archive.org importyeti.com
Casted brass is a popular material used in various industries, including construction, automotive, electronics, and home decor. Companies in China specialize in manufacturing casted brass products, such as fittings, valves, decorative items, and components.
One of the prominent companies in China that manufactures casted brass products is Ningbo Beilun Haikou Die Casting Factory. The company has a strong reputation for producing high-quality brass products using advanced die casting techniques. With years of experience in the industry, Ningbo Beilun Haikou Die Casting Factory has developed a wide range of brass products that meet the needs of different customers.
Another leading company in the casted brass manufacturing industry in China is Zhejiang Longsheng Metal Co., Ltd. The company has a state-of-the-art production facility that is equipped with advanced machinery and technology to produce premium quality casted brass products. Zhejiang Longsheng Metal Co., Ltd. has a team of skilled technicians and engineers who ensure that each product meets international quality standards.
Overall, companies in China that specialize in casted brass manufacturing are known for their expertise, precision, and commitment to delivering top-notch products to customers worldwide. By utilizing platforms such as qcc.com, archive.org, and importyeti.com, businesses can conduct thorough background research on casted brass manufacturers in China to find a reliable and reputable supplier for their brass product needs.
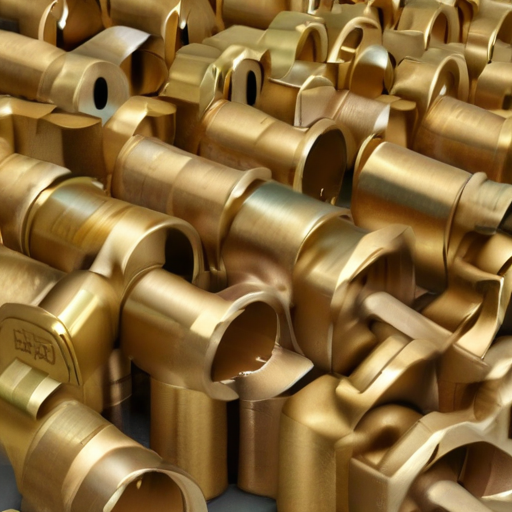
Price Cost Research for casted brass manufacturers Companies in China, use temu.com and 1688.com
When researching the price cost of casted brass manufacturers in China, two popular websites to use are temu.com and 1688.com. These platforms offer a wide range of suppliers and manufacturers, making it easy to compare prices and find the best deal for your needs.
To start your research, simply visit temu.com and 1688.com and search for casted brass manufacturers. You can then browse through the various listings and products to get an idea of the price range. Be sure to pay attention to the price per unit, minimum order quantity, and any additional costs such as shipping or customization fees.
When comparing prices, it’s important to take into account the quality of the product as well. Some manufacturers may offer lower prices, but the quality of their products may not meet your standards. It’s a good idea to reach out to a few different suppliers to request quotes and samples before making a decision.
By using temu.com and 1688.com, you can easily research the price cost of casted brass manufacturers in China and find the best deal for your business. Remember to communicate with the suppliers directly to negotiate prices and discuss any specific requirements you may have.
Shipping Cost for casted brass import from China
The shipping cost for importing casted brass from China can vary depending on several factors. These factors include the weight and size of the shipment, the shipping method chosen, and the final destination of the goods.
Generally, the cost of shipping casted brass from China can range from $1 to $3 per kilogram for sea freight, and $5 to $10 per kilogram for air freight. If you are importing a large quantity of goods, it may be more cost-effective to use sea freight, as it is generally cheaper than air freight for bulk shipments.
Additionally, it is important to consider other costs associated with importing goods from China, such as customs duties, taxes, and import fees. These costs can vary depending on the country of import and the value of the shipment.
To minimize shipping costs, it is recommended to compare prices from different shipping companies and choose the most competitive option. Additionally, consolidating shipments with other importers or using a freight forwarder can help reduce costs by taking advantage of bulk shipping rates.
Overall, when importing casted brass from China, it is important to carefully consider all shipping costs and options to ensure the most cost-effective and efficient delivery of goods.
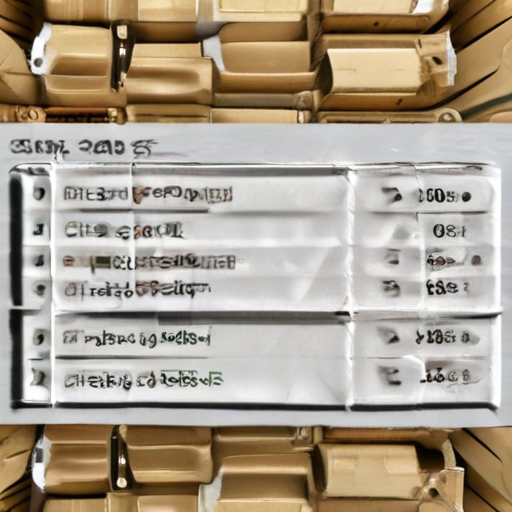
Compare China and Other casted brass Markets: Products Quality and Price,Visible and Hidden Costs
When comparing China with other casted brass markets in terms of product quality and price, it is important to consider both visible and hidden costs.
In terms of product quality, China is known for producing a wide range of casted brass products that meet international standards. The manufacturing industry in China is well-established and has access to advanced technology and skilled labor, which allows for high-quality production. However, the quality of products from other markets may vary depending on the country’s manufacturing standards and regulations.
In terms of price, China is often able to offer competitive prices due to economies of scale, lower labor costs, and government subsidies. This can make Chinese products more affordable compared to products from other casted brass markets. However, it is important to consider the potential risks of lower-priced products, such as lower quality or reliability.
When considering visible costs, China may offer lower upfront prices for casted brass products, making them attractive to buyers. However, hidden costs such as shipping, customs duties, and quality control inspections may add to the overall cost. Other markets may have different cost structures, so it is important to compare all costs before making a purchasing decision.
In conclusion, China is a key player in the casted brass market, offering a combination of quality products and competitive prices. However, buyers should carefully consider both visible and hidden costs when comparing China with other casted brass markets to make an informed decision.
Custom Private Labeling and Branding Opportunities with Chinese casted brass Manufacturers
Chinese casted brass manufacturers offer custom private labeling and branding opportunities for businesses looking to create their own unique products. With their expertise in casting brass, these manufacturers can produce a wide range of items including hardware, décor, and accessories with custom branding and labeling.
By working with a Chinese manufacturer, businesses can create products that stand out in the market and establish a strong brand presence. These manufacturers can help businesses design and produce products that meet their specific requirements and reflect their brand identity. From custom logo engraving to unique packaging options, businesses can create a cohesive and professional look for their products.
In addition to custom branding and labeling, Chinese casted brass manufacturers also offer competitive pricing and high-quality production processes. With their state-of-the-art facilities and skilled technicians, they can ensure that products are produced to the highest standards and meet industry regulations.
Overall, partnering with a Chinese manufacturer for custom private labeling and branding opportunities can help businesses create unique products that resonate with their target audience. By leveraging the expertise and resources of these manufacturers, businesses can bring their vision to life and establish a strong brand presence in the market.
Tips for Procurement and Considerations when Purchasing casted brass
When purchasing casted brass, it is important to consider the following tips and considerations:
1. Quality: Ensure that the brass meets industry standards for quality and durability. Check for any defects or imperfections in the casting that may affect its performance.
2. Cost: Compare prices from different suppliers to ensure you are getting a competitive price for the casted brass. Consider the overall value and quality of the product, rather than just the upfront cost.
3. Supplier reputation: Choose a reputable supplier with a track record of providing high-quality brass products. Ask for references or reviews from previous customers to gauge the supplier’s reliability and customer service.
4. Quantity: Determine the quantity of casted brass needed for your project to ensure you order the right amount. Consider any potential future needs or orders to avoid multiple small purchases.
5. Customization: If you require specific sizes or designs for the casted brass, discuss customization options with the supplier. Ensure they have the capabilities to meet your requirements.
6. Delivery time: Consider the lead time for production and delivery of the casted brass. Plan accordingly to avoid any delays in your project timeline.
7. Material composition: Ask the supplier about the composition of the brass, including the percentage of copper and zinc. Ensure it meets your specific requirements for strength, corrosion resistance, and appearance.
8. Environmental considerations: Consider the environmental impact of the production and disposal of the casted brass. Choose a supplier that follows environmentally friendly practices and offers recycling options.
By keeping these tips and considerations in mind, you can ensure that you make a smart and informed decision when purchasing casted brass for your project.
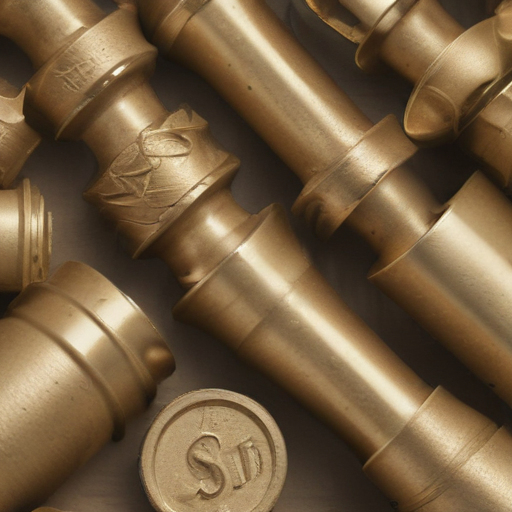
FAQs on Sourcing and Manufacturing casted brass in China
1. What are the benefits of sourcing casted brass from China?
Sourcing casted brass from China offers several benefits, including cost-effectiveness due to lower labor and production costs, access to a wide range of suppliers and manufacturers, and high-quality production capabilities.
2. How can I find reliable manufacturers for casted brass in China?
To find reliable manufacturers for casted brass in China, you can conduct thorough research online, attend trade shows and industry events, ask for recommendations from other businesses or industry professionals, and conduct site visits to assess their manufacturing facilities.
3. What factors should I consider when sourcing casted brass from China?
When sourcing casted brass from China, it’s important to consider factors such as the quality of the products, the production capabilities of the manufacturer, their experience and reputation in the industry, compliance with industry standards and regulations, lead times for production and delivery, and communication and language barriers.
4. How can I ensure the quality of casted brass produced in China?
To ensure the quality of casted brass produced in China, you can work closely with the manufacturer to develop clear specifications and requirements, conduct regular quality inspections and audits, implement a quality control process, and establish open communication channels with the manufacturer.
5. What are the common manufacturing processes used for casting brass in China?
The common manufacturing processes used for casting brass in China include sand casting, die casting, investment casting, and continuous casting. Each process has its own advantages and is suitable for different types of products and production requirements. It is important to select the most appropriate process based on your specific needs and budget.
Why contact sourcifychina.com get free quota from reliable casted brass suppliers?
Sourcifychina.com provides a platform that connects businesses with reliable casted brass suppliers in China. By contacting Sourcifychina.com and obtaining a free quota, businesses can access a network of trusted suppliers who offer high-quality products at competitive prices. This can help businesses streamline their sourcing process, reduce costs, and ensure the timely delivery of products.
Working with reliable casted brass suppliers through Sourcifychina.com can also help businesses benefit from the expertise and experience of these suppliers. They can offer valuable insights and recommendations to help businesses make informed decisions and improve their overall sourcing strategy.
In addition, sourcing through Sourcifychina.com can provide businesses with access to a wider range of suppliers, increasing their options and flexibility. This can help businesses find the right supplier that meets their specific requirements and preferences.
Overall, by obtaining a free quota from reliable casted brass suppliers through Sourcifychina.com, businesses can improve their sourcing process, save time and money, and ultimately enhance their overall competitiveness in the market.