Top fabricating brackets in China introduce,list main products and website if have
China is known for its high-quality fabrication of brackets, offering a wide range of hardware products for various industries. Some of the top fabricating bracket manufacturers in China include Shaoxing Shangyu Peijie Import & Export Co., Ltd, Hangzhou Aodi Electronic Control Co., Ltd, and Dongguan Juming Metal Products Co., Ltd.
Shaoxing Shangyu Peijie Import & Export Co., Ltd specializes in the production of metal brackets, shelf brackets, and pipe clamps. Their products are known for their durability and high-quality finish. You can find more information about their products on their website: http://www.peijie-metal.com/
Hangzhou Aodi Electronic Control Co., Ltd specializes in the fabrication of customized metal brackets for electronic equipment, automotive components, and industrial machinery. They also offer precision machining services for complex bracket designs. For more details, visit their website: http://www.aodimetal.com/
Dongguan Juming Metal Products Co., Ltd is a leading manufacturer of metal brackets for the furniture industry, including cabinet brackets, shelf brackets, and support brackets. Their products are known for their innovative design and excellent performance. You can explore their product range on their website: http://www.jumingmetal.com/
These top fabricating bracket manufacturers in China offer a wide range of high-quality products suitable for various industries. Whether you are looking for standard brackets or custom-designed solutions, these companies can meet your requirements with their expertise in metal fabrication.
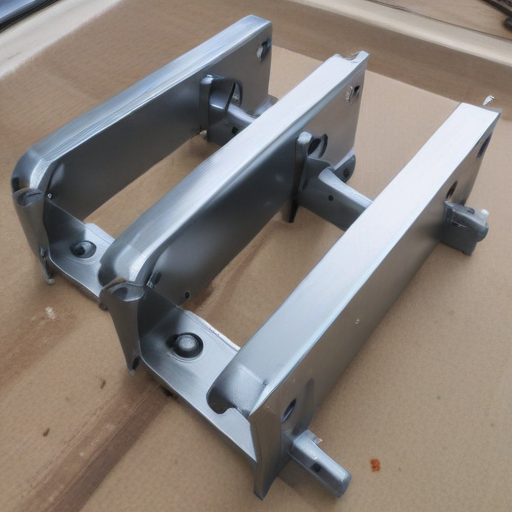
Types of fabricating brackets
Bracket fabrication is a process that involves creating a support or fixture typically used in construction or engineering projects. There are several types of brackets used in various applications, each designed to provide support and stability for different structures.
1. L-shaped brackets: L-shaped brackets are one of the most common types of brackets used in construction and engineering projects. These brackets are shaped like the letter “L” and are used to provide support and reinforcement to shelves, countertops, and other structures. They can be made from various materials, including metal, wood, and plastic.
2. Corner brackets: Corner brackets are used to provide additional support and stability to corners of structures. These brackets are typically made from metal or wood and are used to connect two perpendicular sections or beams together at a right angle. Corner brackets are commonly used in furniture construction, shelving units, and framing projects.
3. Angle brackets: Angle brackets are similar to L-shaped brackets but have a wider range of applications. These brackets are typically made from metal and are used to join two components at an angle. Angle brackets are commonly used in construction projects, such as securing beams or connecting framing elements.
4. T-plates: T-plates are used to connect two components in a T-shaped configuration. These brackets are typically made from metal and are used to provide additional support and reinforcement to structures. T-plates are commonly used in woodworking projects, furniture construction, and framing applications.
5. U-shaped brackets: U-shaped brackets are used to provide support and reinforcement to pipes, tubes, and other cylindrical structures. These brackets are shaped like the letter “U” and are typically made from metal. U-shaped brackets are commonly used in plumbing, HVAC, and electrical applications.
Overall, bracket fabrication involves the creation of various types of brackets that provide support and stability to different structures. The type of bracket used will depend on the specific requirements of the project and the materials being used.
Pros and Cons of Using fabricating brackets
Fabricating brackets has several advantages. First and foremost, it allows for a custom fit, ensuring that the bracket matches the specific dimensions and requirements of the project. This can result in improved accuracy and functionality of the final product. Additionally, fabricating brackets can be cost-effective, especially for one-off or small batch production runs, as they can be made to order without the need for expensive tooling or molds.
Another benefit of fabricating brackets is the ability to choose from a wide range of materials, including steel, aluminum, and stainless steel, depending on the specific needs of the project. This flexibility allows for the selection of the most appropriate material for the application, whether it be strength, corrosion resistance, or weight considerations.
However, there are also some drawbacks to consider when using fabricating brackets. One potential downside is the time and skill required to fabricate brackets, especially for complex designs or materials. This can result in longer lead times and potentially higher costs compared to off-the-shelf bracket options.
Additionally, the quality of the final product may vary depending on the skill and experience of the fabricator. Inexperienced or low-quality fabricators may produce brackets that do not meet the necessary specifications or standards, leading to potential issues down the line.
In conclusion, fabricating brackets can offer numerous benefits, including a custom fit, cost-effectiveness, and material flexibility. However, it is important to weigh these advantages against the potential drawbacks of time, skill, and quality concerns when considering fabricating brackets for a project.
fabricating brackets Reference Specifications (varies for different product)
When fabricating brackets, it is important to refer to the specific Reference Specifications provided for the particular product being manufactured. These specifications may vary depending on the material, size, and intended use of the brackets.
Typically, Reference Specifications will include information on the required dimensions, tolerances, material composition, and any additional requirements for the brackets. It is important to adhere to these specifications to ensure that the brackets meet the necessary standards for strength, durability, and functionality.
When fabricating brackets, it is recommended to carefully review the Reference Specifications before beginning the manufacturing process. This will help ensure that the brackets are fabricated according to the necessary guidelines and will perform as intended once installed.
In addition, it is advisable to use high-quality materials and precision manufacturing techniques when fabricating brackets. This will help to ensure the durability and reliability of the brackets, as well as minimize the risk of any defects or failures.
By following the Reference Specifications and utilizing proper manufacturing techniques, fabricators can produce brackets that meet the required standards and provide reliable support for a wide range of applications.
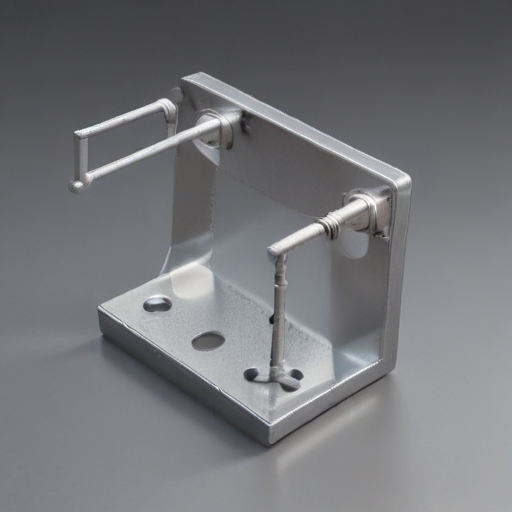
Applications of fabricating brackets
Brackets are commonly used in various industries for a wide range of applications. One of the most common uses of fabricating brackets is in the construction industry. Brackets are used to support beams, joists, and other structural elements in buildings. By fabricating brackets to specific sizes and shapes, they can provide essential structural support, ensuring the stability and safety of buildings.
In the automotive industry, brackets are used for mounting various components such as engine parts, exhaust systems, and suspension components. Fabricating brackets allows for custom designs that can meet the specific requirements of different vehicles and improve overall performance.
Brackets are also commonly used in the furniture industry for attaching legs, shelves, and other components to furniture pieces. By fabricating brackets with precision and quality materials, furniture manufacturers can ensure durability and stability of their products.
In the electronics industry, brackets are used for mounting components such as circuit boards, screens, and panels. The fabrication of brackets allows for customized designs that can accommodate specific electronic components and ensure proper positioning and alignment.
In the aerospace industry, brackets are used for mounting various instruments, controls, and components in aircraft. Fabricating brackets to meet strict quality and safety standards is crucial in ensuring the reliability and performance of aircraft systems.
Overall, the applications of fabricating brackets are diverse and widespread across different industries. By utilizing brackets in various applications, manufacturers can optimize the functionality, durability, and safety of their products.
Material of fabricating brackets
There are various materials that can be used for fabricating brackets, each offering unique properties and advantages. Some of the common materials used for brackets include:
1. Stainless steel: Stainless steel is a popular choice for brackets due to its corrosion resistance, durability, and strength. It is easy to clean and maintain, making it ideal for applications where hygiene is important. Stainless steel brackets are commonly used in medical devices, automotive parts, and construction.
2. Aluminum: Aluminum is a lightweight and corrosion-resistant material that is commonly used for brackets in aerospace, automotive, and electronics industries. It is also easily machined and formed, making it a versatile option for various applications.
3. Carbon steel: Carbon steel is a strong and durable material that is often used for heavy-duty brackets. It is cost-effective and readily available, making it a popular choice for industrial and construction applications.
4. Plastics: Certain types of plastics, such as nylon, acetal, and polycarbonate, can also be used for fabricating brackets. Plastics are lightweight, durable, and resistant to corrosion, making them suitable for applications where metal brackets may not be ideal.
5. Composite materials: Composite materials, such as fiberglass-reinforced plastics or carbon fiber, offer a combination of strength, durability, and lightweight properties. These materials are commonly used in high-performance brackets for aerospace, automotive, and sports equipment applications.
When selecting a material for fabricating brackets, it is important to consider the specific requirements of the application, such as load-bearing capacity, corrosion resistance, weight, and cost. By carefully evaluating these factors, engineers and designers can choose the most suitable material for their bracket fabrication needs.
Quality Testing Methods for fabricating brackets and how to control the quality
There are a variety of quality testing methods that can be used to ensure that brackets are fabricated to meet the desired specifications. Some common methods include:
1. Dimensional testing: This involves measuring the dimensions of the brackets to ensure they meet the required specifications. This can be done using tools such as calipers, micrometers, and gauges.
2. Visual inspection: Visual inspection can help to identify any visible defects such as cracks, scratches, or surface imperfections that may affect the quality of the brackets. This can be done using magnifying glasses or cameras.
3. Load testing: This involves applying a specific load to the brackets to test their strength and durability. This can be done using equipment such as hydraulic or mechanical testing machines.
4. Metallurgical testing: This type of testing involves analyzing the metallurgical properties of the material used to fabricate the brackets. This can help ensure that the material meets the required standards for strength, durability, and corrosion resistance.
To control the quality of the brackets, it is important to establish a quality control system that includes regular inspection and testing at various stages of the fabrication process. This can help to identify any potential issues early on and ensure that the brackets meet the desired specifications. Additionally, it is important to train and educate staff members on quality control procedures and the importance of producing high-quality brackets.
By implementing these quality testing methods and control measures, manufacturers can produce brackets that meet the desired specifications and ensure the overall quality and reliability of the final product.
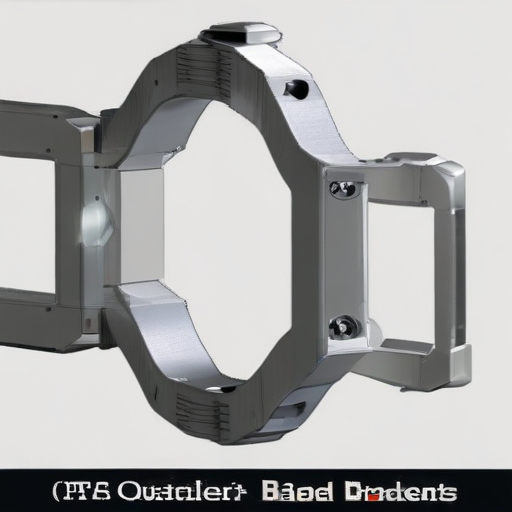
The Work Process and how to use fabricating brackets
The work process of fabricating brackets involves several steps. First, the material for the brackets, typically aluminum or stainless steel, is chosen based on the specific requirements of the project. The material is then cut to the appropriate size using a bandsaw or laser cutting machine.
Next, the brackets are shaped and formed using a variety of techniques such as bending, stamping, or welding. Precision is crucial in this step to ensure that the brackets fit properly and perform their intended function.
Once the brackets are formed, they may undergo additional processes such as drilling holes for mounting hardware, painting or powder coating for corrosion resistance, or adding protective coatings for specific applications.
To use fabricating brackets effectively, it is important to carefully follow the design specifications and instructions provided. Properly aligning the brackets with the components they are intended to support is crucial to ensure structural integrity and longevity.
Furthermore, it is essential to use the appropriate tools and equipment for the job, such as clamps, welding machines, and measuring devices. Safety precautions should always be observed to prevent injuries and accidents.
In conclusion, fabricating brackets involves a series of precise steps to create functional and durable components. By following the work process diligently and using the proper techniques, fabricating brackets can be an efficient and effective way to support various structures and equipment.
fabricating brackets Importing questions including Cost,Supplier,Sample,Certification and Market
When fabricating brackets, there are several important considerations to keep in mind.
Cost: It is important to determine the cost of fabricating the brackets, including the materials and labor involved. This will help in setting the right price for the brackets to ensure profitability.
Supplier: Finding a reliable supplier for the materials needed for fabricating brackets is crucial. It is recommended to do thorough research and choose a supplier that offers high-quality materials at competitive prices.
Sample: Before fabricating brackets in bulk, it is advisable to create a sample to test the design and functionality. This will help in making any necessary adjustments before mass production.
Certification: It is important to ensure that the brackets meet all necessary certification requirements. This may include safety certifications or quality control standards. It is recommended to work with a reputable testing facility to certify the brackets.
Market: Before mass-producing the brackets, it is important to conduct market research to understand the demand for the product. This will help in determining the target market and setting sales goals.
In conclusion, fabricating brackets involves several important considerations such as cost, supplier selection, creating samples, obtaining certifications, and understanding the market. By carefully addressing these factors, you can ensure the success of your bracket fabrication business.
How to find and select check reliable fabricating brackets manufacturers in China
To find and select reliable fabricating brackets manufacturers in China, you can start by researching online directories such as Alibaba, Made-in-China, or Global Sources. Look for manufacturers with a good reputation, positive reviews, and years of experience in producing fabricating brackets.
You can also ask for recommendations from other businesses or industry contacts who have sourced products from China. Once you have a shortlist of potential manufacturers, reach out to them to inquire about their production capabilities, quality control measures, and pricing.
Request samples of their fabricating brackets to assess their quality and durability. Additionally, ask for references from their current or past clients to get a better understanding of their reliability and customer service.
Make sure the manufacturer complies with international quality standards and certifications. It’s also important to visit their factory in person or conduct a virtual factory tour to ensure they have the necessary equipment and expertise to meet your requirements.
Negotiate the terms of the contract, including pricing, lead times, payment terms, and quality control processes. Request a detailed written agreement outlining all specifications and expectations to avoid any misunderstandings down the line.
By following these steps and conducting thorough due diligence, you can find and select a reliable fabricating brackets manufacturer in China to meet your business needs.
Background Research for fabricating brackets manufacturers Companies in China, use qcc.com archive.org importyeti.com
Fabricating brackets manufacturers in China can be found through various sources such as QCC.com, which provides a comprehensive database of companies and their products. Archive.org is another useful resource for finding information on past projects and the reputation of manufacturers in the industry. Importyeti.com can also be utilized to track imports and exports of brackets from China to get an idea of the market demand and competition.
By utilizing these resources, businesses can gather valuable background research on fabricating brackets manufacturers in China. This information can help in evaluating the quality, pricing, and reliability of potential suppliers, as well as comparing their capabilities and offerings. It is important to consider factors such as production capacity, certification, and customer reviews when selecting a manufacturer.
Additionally, conducting thorough research can help in identifying trends in the industry, potential challenges, and opportunities for collaboration or improvement. By staying informed and informed on the market landscape, businesses can make more strategic decisions and build stronger partnerships with manufacturers in China.
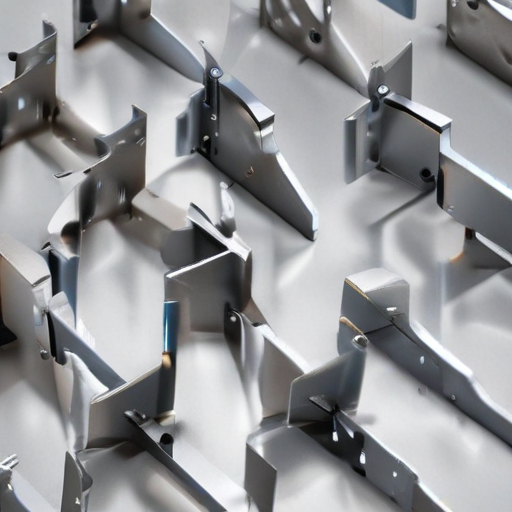
Price Cost Research for fabricating brackets manufacturers Companies in China, use temu.com and 1688.com
When seeking price and cost research for fabricating brackets manufacturers in China, two popular platforms to visit are temu.com and 1688.com. These websites offer a wide range of options for sourcing products and connecting with manufacturers in China.
On temu.com, users can search for specific manufacturers of brackets and request quotes directly from suppliers. The platform allows for easy communication and negotiation with potential suppliers, helping to ensure competitive pricing for fabricating brackets.
Similarly, 1688.com is a leading Chinese e-commerce platform that provides access to a multitude of fabricating brackets manufacturers. Users can browse through different suppliers and compare prices and quality of products. This platform also allows for direct communication with manufacturers to discuss specific requirements and negotiate pricing.
By utilizing these platforms, businesses can conduct thorough research on price and costs associated with fabricating brackets from manufacturers in China. It is recommended to reach out to multiple suppliers, compare quotes, and negotiate pricing to ensure the best deal possible. With the wide range of options available on temu.com and 1688.com, businesses can easily find the right manufacturer that meets their budget and quality requirements.
Shipping Cost for fabricating brackets import from China
When importing fabricating brackets from China, the shipping costs will depend on various factors such as the size and weight of the brackets, the shipping method chosen, and the distance they need to travel.
For smaller orders, air freight may be the quickest option but it can also be more expensive compared to sea freight. Sea freight is the most cost-effective option for larger orders as it allows for bulk shipping and economies of scale.
The shipping cost for fabricating brackets from China typically includes various charges such as freight charges, handling fees, customs clearance, and import duties. It is important to factor in all these costs when calculating the total shipping cost.
To try to keep the shipping cost under $300, it is recommended to work with a freight forwarder who can negotiate better rates with shipping companies. Consolidating orders to ship in bulk can also help reduce shipping costs. Additionally, choosing a slower shipping option or opting for less-urgent delivery times can also lower the shipping cost.
It is important to compare quotes from different shipping companies and consider all factors such as transit time, reliability, and additional services offered. By planning ahead and optimizing the shipping process, it is possible to keep the shipping cost for fabricating brackets import from China within the $300 budget.
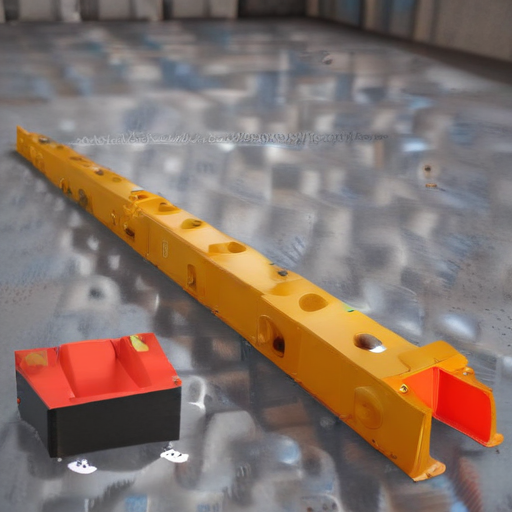
Compare China and Other fabricating brackets Markets: Products Quality and Price,Visible and Hidden Costs
China is known for its low-cost manufacturing, which often results in lower priced products compared to other fabricating brackets markets. However, this lower price point can sometimes come at the expense of product quality. In some cases, the durability and performance of Chinese-made fabricating brackets may not match those produced in other markets, leading to potential issues with product longevity and reliability.
In terms of visible costs, Chinese fabricating brackets typically offer a more affordable option for consumers looking to save money on their purchases. However, there may be hidden costs associated with sourcing products from China, such as shipping fees, import duties, and longer lead times. These additional expenses can eat into the initial cost savings and impact the overall value proposition for customers.
On the other hand, fabricating brackets from other markets, such as the US or Europe, may come with a higher price tag but often offer superior quality and performance. These products are typically manufactured to higher standards and may be more reliable in the long run. While the upfront cost may be higher, customers may see a better return on investment due to the product’s durability and longevity.
Overall, the choice between Chinese fabricating brackets and those from other markets will ultimately come down to a balancing act between price and quality. Customers who prioritize cost savings may opt for Chinese-made products, while those looking for top-notch performance may be willing to pay a premium for brackets from other markets. It’s important for buyers to carefully weigh the visible and hidden costs associated with each option to make an informed decision based on their specific needs and budget constraints.
Custom Private Labeling and Branding Opportunities with Chinese fabricating brackets Manufacturers
Chinese fabricating brackets manufacturers offer custom private labeling and branding opportunities for businesses looking to enhance their brand identity and stand out in the market. By partnering with these manufacturers, businesses can create their own unique branded products, tailored to their specific design and branding requirements.
Through private labeling, businesses can add their logo, brand name, and other custom design elements to the fabricating brackets, creating a cohesive and professional look for their products. This helps to build brand recognition and loyalty among customers, as well as differentiate their products from competitors.
Additionally, partnering with Chinese fabricating brackets manufacturers for custom branding allows businesses to take advantage of cost-effective manufacturing processes and high-quality materials. This enables them to offer top-notch products to their customers, while maintaining competitive pricing in the market.
Overall, custom private labeling and branding opportunities with Chinese fabricating brackets manufacturers provide businesses with the ability to create unique, branded products that resonate with their target audience. This can help drive sales, strengthen brand identity, and establish a strong presence in the market.
Tips for Procurement and Considerations when Purchasing fabricating brackets
When purchasing fabricating brackets, there are several considerations to keep in mind to ensure successful procurement:
1. Quality: The quality of the brackets is crucial to ensure their durability and functionality. Look for brackets made from high-quality materials such as steel or aluminum that are designed to withstand various types of loads and stress.
2. Compatibility: Make sure that the brackets are compatible with the specific materials and equipment they are intended to support. Consider factors like size, weight capacity, and mounting options when selecting brackets for a particular project.
3. Cost: While it is important to ensure high quality, also consider the cost of the brackets. Compare prices from different suppliers to find the best value for your budget. Remember to factor in any additional costs such as shipping or installation fees.
4. Supplier reliability: Choose a reputable supplier with a track record of providing high-quality products and excellent customer service. Check reviews and testimonials from previous customers to ensure you are dealing with a reliable supplier.
5. Customization options: If standard brackets do not meet your project requirements, look for suppliers that offer customization options. This can include modifying the size, shape, or material of the brackets to better suit your needs.
6. Environmental considerations: If sustainability is important to you, consider purchasing brackets made from recycled materials or from suppliers with eco-friendly practices. Look for certifications such as ISO 14001 to ensure the brackets meet environmental standards.
Remember to communicate clearly with your supplier about your project requirements and specifications to ensure you receive the right fabricating brackets for your needs. By considering these tips and factors, you can make an informed decision when purchasing fabricating brackets for your project.
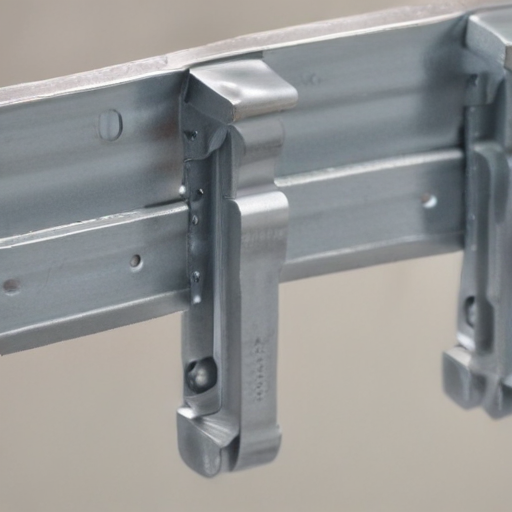
FAQs on Sourcing and Manufacturing fabricating brackets in China
1. How can I find a reliable manufacturer for fabricating brackets in China?
You can start by researching online, attending trade shows, or working with sourcing agents who have experience in the Chinese manufacturing industry. Verify the manufacturer’s credentials, quality control processes, and track record before finalizing any agreements.
2. What factors should I consider when sourcing brackets from China?
Consider the manufacturer’s production capacity, lead times, pricing, quality standards, and communication abilities. Also, ensure they comply with any regulatory or safety requirements for your specific market.
3. How can I ensure the quality of brackets manufactured in China?
Insist on samples and prototypes before mass production begins. Implement regular quality control checks throughout the manufacturing process and consider conducting independent inspections or audits. Clear communication with the manufacturer is essential to address any issues promptly.
4. What are the typical lead times for fabricating brackets in China?
Lead times can vary depending on the complexity of the brackets, the manufacturer’s capacity, and any customization requirements. Generally, you should factor in at least 4-6 weeks for production and additional time for shipping and customs clearance.
5. What are the common challenges when sourcing and manufacturing brackets in China?
Challenges may include language barriers, cultural differences, quality control issues, intellectual property concerns, and logistics challenges. Working closely with a reputable sourcing partner or consultant can help navigate these obstacles effectively.
Why contact sourcifychina.com get free quota from reliable fabricating brackets suppliers?
SourcifyChina.com is a trusted platform that connects businesses with reliable fabricating brackets suppliers in China. By contacting SourcifyChina.com, you can get a free quota for your bracket fabrication needs.
SourcifyChina.com works with a network of pre-vetted and quality-assured suppliers, ensuring that you have access to top-tier manufacturers for your bracket fabrication requirements. This helps you save time and effort in sourcing and verifying suppliers on your own.
By obtaining a free quota through SourcifyChina.com, you can easily compare quotes from different fabricating brackets suppliers and choose the one that best fits your budget and quality requirements. This allows you to make an informed decision and ensure that you are getting the best value for your money.
Additionally, SourcifyChina.com’s team of experts can assist you throughout the sourcing and manufacturing process, providing guidance and support to ensure a smooth and successful collaboration with the chosen supplier.
Overall, contacting SourcifyChina.com for a free quota from reliable fabricating brackets suppliers is a convenient and efficient way to streamline your sourcing process and secure high-quality products at competitive prices.