Top metal blanking in China introduce,list main products and website if have
China is a leading manufacturer of metal blanking products, with a reputation for high-quality precision and advanced technology. Some of the top metal blanking companies in China include:
1. Foxron Precision Metal Parts Co., Ltd.: Foxron specializes in the production of metal stamping and forming parts for various industries such as automotive, electronics, and furniture. Their main products include precision metal stamping parts, die casting parts, and CNC machining parts. Website: https://www.foxron.com/
2. Ningbo OEM Industry Manufacturer Ltd.: Ningbo OEM is a professional manufacturer of metal stamping and forming products, including precision stamped parts, metal enclosures, and brackets. They serve customers in sectors such as automotive, electrical, and telecommunications. Website: http://www.nb-precision.com/
3. Shenzhen Soven Technology Co., Ltd.: Soven Technology specializes in the production of precision metal stamping parts, deep drawing parts, and sheet metal fabrication. They provide customized solutions for various industries, such as medical equipment, aerospace, and consumer electronics. Website: http://www.sovenstampings.com/
These top metal blanking companies in China are known for their expertise in producing high-quality stamped and formed metal parts for a wide range of applications. Their advanced technology and precision manufacturing capabilities ensure reliable and durable products for customers worldwide.
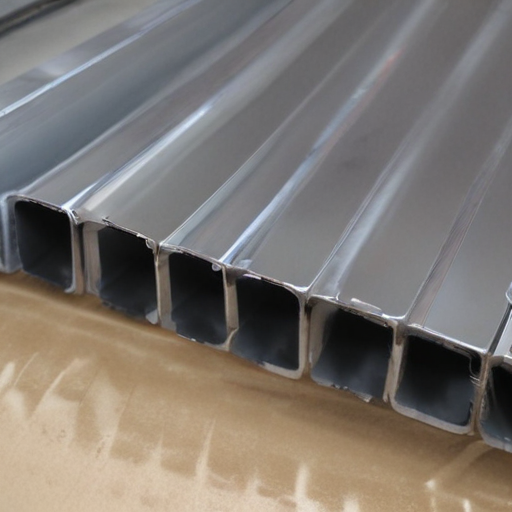
Types of metal blanking
There are several types of metal blanking processes used in manufacturing to shape raw materials into various components. The most common types of metal blanking include:
1. Shearing: Shearing is a process used to cut large sheets of metal into smaller pieces. A hydraulic or mechanical press is used to apply a shearing force, which creates a clean edge on the metal. This process is commonly used for straight cuts and simple shapes.
2. Punching: Punching involves using a punch and die set to create holes or other shapes in a metal sheet. The punch applies force to the metal sheet, causing it to deform and create the desired shape. This process is commonly used for creating holes, notches, or intricate shapes in metal components.
3. Laser cutting: Laser cutting is a precise and efficient method of cutting metal sheets using a high-powered laser. The laser beam melts or vaporizes the metal, creating a clean and accurate cut. This process is ideal for intricate and complex shapes, as well as thin metal sheets.
4. Water jet cutting: Water jet cutting uses a high-pressure stream of water mixed with abrasive particles to cut through metal sheets. This method is versatile and can be used for cutting a wide range of materials, including metals, plastics, and composites. Water jet cutting is ideal for cutting thick metal sheets or materials that are sensitive to heat.
5. Blanking and piercing: Blanking and piercing are processes that involve cutting out a specific shape from a metal sheet or strip. Blanking removes the desired shape from the metal sheet, while piercing creates holes or slots within the remaining material. These processes are commonly used in the production of metal components for various industries.
Overall, metal blanking processes vary in terms of complexity, precision, and cost. Choosing the right blanking method depends on the specific requirements of the component being produced, including material type, thickness, and desired shape.
Pros and Cons of Using metal blanking
Metal blanking is a metal forming process that involves cutting a shape from a metal sheet or strip. There are several pros and cons to using metal blanking in manufacturing processes.
Pros:
1. Precision: Metal blanking allows for precise cutting of shapes, resulting in high-quality finished products.
2. Speed: Metal blanking is a fast and efficient process, making it ideal for high-volume production.
3. Cost-effective: Metal blanking can help reduce material waste and improve production efficiency, leading to cost savings.
4. Versatility: Metal blanking can be used to cut a wide range of shapes and sizes, making it versatile for various manufacturing applications.
5. Consistency: Metal blanking ensures consistent results in terms of shape and dimensions, leading to uniformity in the final products.
Cons:
1. Initial setup cost: Metal blanking requires specialized equipment and tooling, which can be costly to set up initially.
2. Material limitations: Metal blanking is typically limited to flat sheet or strip materials, which may restrict the types of products that can be produced.
3. Waste disposal: Metal blanking can produce waste material that needs to be properly disposed of or recycled, adding to the overall production costs.
4. Design limitations: Metal blanking may not be suitable for complex shapes or intricate designs, as it is primarily focused on cutting basic shapes from sheet metal.
5. Skill requirements: Metal blanking requires skilled operators to ensure accurate cutting and efficient production, which may add to labor costs.
In conclusion, metal blanking offers several advantages in terms of precision, speed, cost-effectiveness, versatility, and consistency. However, there are also potential drawbacks related to initial setup costs, material limitations, waste disposal, design restrictions, and skill requirements. Overall, the decision to use metal blanking will depend on the specific manufacturing requirements and goals of a company.
metal blanking Reference Specifications (varies for different product)
Metal blanking is a manufacturing process used to produce flat, geometrically-precise metal components through the shearing or punching of metal sheets. The process involves cutting out a predetermined shape from a larger piece of metal, resulting in a blank (or flat) part that can be further processed to create a finished product. Metal blanking is commonly used in the automotive, aerospace, and appliance industries to produce a wide range of components such as brackets, clips, and panels.
The specifications for metal blanking can vary depending on the specific requirements of the product being produced. This includes the type of metal being used, the thickness of the metal sheet, and the desired shape and dimensions of the final component. Common materials used in metal blanking include steel, aluminum, and stainless steel, with thicknesses typically ranging from 0.005 to 0.25 inches.
In terms of tolerances, the level of precision required for metal blanking can vary depending on the application. Some products may require tight tolerances to ensure a proper fit, while others may have more forgiving specifications. Additionally, secondary operations such as bending, forming, or machining may be required to further shape the blanked part into its final form.
Overall, metal blanking is a versatile and efficient manufacturing process that allows for the production of high-quality metal components with a wide range of specifications. By carefully considering the specific requirements of the product being produced, manufacturers can optimize the blanking process to achieve the desired results.
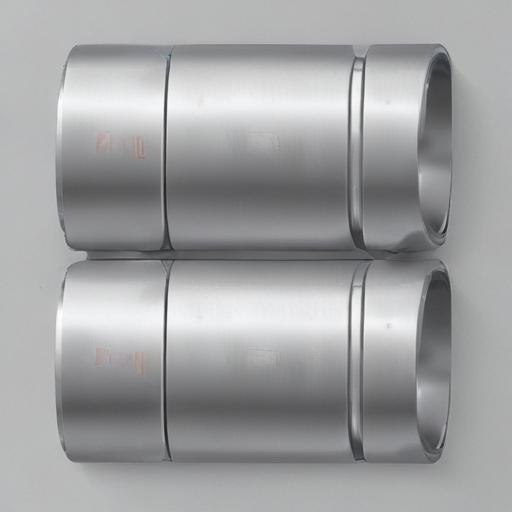
Applications of metal blanking
Metal blanking is a manufacturing process used to create precision metal parts by cutting or punching them out of sheets or coils of metal. This process is commonly used in industries such as automotive, aerospace, and electronics for a variety of applications.
One of the key applications of metal blanking is in the production of automotive components. Metal blanking is used to create parts such as fenders, doors, hoods, and other body panels for vehicles. These parts are essential for the structural integrity and aesthetics of the vehicle, and metal blanking allows for high precision and consistency in their production.
Metal blanking is also used in the aerospace industry for the manufacturing of components such as engine parts, brackets, and panels. The strict quality standards and high tolerance requirements of the aerospace industry make metal blanking an ideal process for producing these critical parts accurately and efficiently.
In the electronics industry, metal blanking is used to create components such as heat sinks, brackets, and connectors. These components are essential for the functionality and reliability of electronic devices, and metal blanking allows for intricate shapes and precise dimensions to be achieved.
Overall, metal blanking is a versatile and widely used manufacturing process with applications in various industries. Its ability to produce high-quality metal parts with tight tolerances makes it essential for the production of a wide range of products.
Material of metal blanking
Metal blanking is a process used to cut, shape, and form metal sheets into the desired size and shape to create a variety of metal products. The material used for metal blanking typically depends on the specific requirements of the final product and can vary from carbon steel, stainless steel, aluminum, brass, copper, and other types of metals.
Carbon steel is a common material used for metal blanking due to its strength, durability, and affordability. It is relatively easy to work with and can be formed into various shapes and sizes. Stainless steel, on the other hand, is known for its corrosion resistance and is often used in industries where sanitation and hygiene are important, such as food processing and medical equipment manufacturing.
Aluminum is lightweight and has good thermal and electrical conductivity, making it an ideal material for products that require these properties, such as automotive parts and electronics. Brass and copper are also popular choices for metal blanking due to their malleability, corrosion resistance, and aesthetic appeal, making them suitable for applications like decorative hardware and plumbing fixtures.
In conclusion, the material used for metal blanking plays a crucial role in determining the performance, appearance, and cost of the final product. By selecting the right material based on the specific requirements of the project, manufacturers can ensure the success of their metal blanking operations.
Quality Testing Methods for metal blanking and how to control the quality
Metal blanking is a common manufacturing process used to cut a flat piece of metal into a specific shape or size. To ensure the quality of the blanked metal parts, several testing methods can be employed.
One common method is visual inspection, where the blanked parts are visually examined for any defects such as burrs, cracks, or uneven edges. This can be done manually or using automated optical inspection systems.
Another testing method is dimensional inspection, where the blanked parts are measured using precision measuring equipment such as calipers or micrometers to ensure they meet the specified dimensions.
Material testing is also important in ensuring the quality of the blanked metal parts. This can include testing the hardness, tensile strength, and ductility of the metal to ensure it meets the required specifications.
To control the quality of metal blanking, it is important to establish clear quality control procedures and regularly monitor and inspect the blanked parts at various stages of the manufacturing process. Any defects or deviations from the specified requirements should be addressed immediately to prevent the production of faulty parts.
Additionally, implementing preventive maintenance programs for the equipment used in metal blanking can help ensure consistent quality and reduce the likelihood of defects. Regular calibration of measuring equipment and training of operators can also contribute to maintaining quality standards.
In conclusion, by utilizing a combination of testing methods, implementing quality control procedures, and investing in preventive maintenance programs, the quality of metal blanking can be effectively controlled to produce high-quality parts consistently.
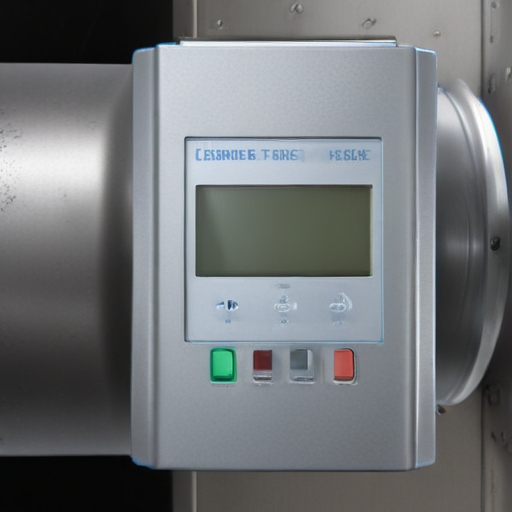
The Work Process and how to use metal blanking
Metal blanking is a manufacturing process where a metal workpiece is cut or stamped into a specific shape or size. This process is commonly used in industries such as automotive, aerospace, and electronics to create parts and components with precise dimensions.
To use metal blanking, the first step is to design or select a die that corresponds to the desired shape of the finished product. The die is then mounted onto a press machine, which exerts force to cut or stamp the metal workpiece.
During the blanking process, the metal workpiece is placed onto the die and secured in place. The press machine then moves the die against the workpiece, shearing the metal and leaving behind the desired shape. The excess metal, known as the scrap, is separated from the finished part and can be recycled or disposed of.
Metal blanking can be used to create a wide range of products, from simple flat shapes to complex geometries. The process is ideal for producing high volumes of parts with consistent dimensions and high precision.
In conclusion, metal blanking is a versatile manufacturing process that can be used to create precise metal parts and components. By following the proper steps and using the right equipment, metal blanking can be an efficient and cost-effective way to produce quality metal products.
metal blanking Importing questions including Cost,Supplier,Sample,Certification and Market
Metal blanking is the process of cutting a desired shape out of a flat metal sheet. When importing metal blanking products, there are several important factors to consider.
Cost is a crucial factor in importing metal blanking products. It is important to consider not only the initial cost of the products but also any additional costs such as shipping, import duties, and taxes. It is essential to compare prices from different suppliers to ensure you are getting the best deal.
Choosing a reliable supplier is key in ensuring the quality of the metal blanking products. Look for suppliers with a good reputation, experience in the industry, and positive customer reviews. It is also important to consider the supplier’s production capacity and ability to meet your demand.
Requesting samples from potential suppliers is a good way to assess the quality of the metal blanking products. Make sure to carefully evaluate the samples for accuracy, precision, and durability before making a decision.
Certification is another important consideration when importing metal blanking products. Look for suppliers that have relevant certifications such as ISO certification, which guarantees that the products meet international quality standards.
Lastly, it is important to research the market for metal blanking products in your country to understand the demand and competition. Consider factors such as trends, market size, and potential competitors to make an informed decision.
In conclusion, when importing metal blanking products, consider factors such as cost, supplier reputation, product samples, certifications, and market research to ensure a successful import process.
How to find and select check reliable metal blanking manufacturers in China
1. Research: Start by conducting online research to find a list of metal blanking manufacturers in China. Use search engines, online directories, and industry forums to compile a list of potential suppliers.
2. Verify credentials: Check the manufacturer’s website and review their credentials, certifications, and years of experience in the metal blanking industry. Look for manufacturers with a proven track record of quality and reliability.
3. Request samples: Contact the shortlisted manufacturers and request samples of their metal blanking products. Evaluate the quality, precision, and finish of the samples to ensure they meet your requirements.
4. Quality standards: Inquire about the quality control measures and standards followed by the manufacturer. Look for manufacturers who adhere to international quality standards like ISO certification to ensure consistent quality in their products.
5. Communication: Evaluate the manufacturer’s communication skills and responsiveness. Clear and timely communication is essential for a successful partnership.
6. Price comparison: Obtain quotes from multiple manufacturers and compare their pricing, taking into consideration factors like quality, lead time, and additional services offered.
7. Reviews and references: Check online reviews and ask for references from past clients to get insights into the manufacturer’s reputation and customer satisfaction levels.
8. Visit the facility: If possible, visit the manufacturer’s facility in person to assess their manufacturing capabilities, infrastructure, and quality control processes.
9. Negotiate terms: Once you have selected a reliable metal blanking manufacturer, negotiate terms regarding pricing, lead times, payment terms, and any additional services required.
10. Contract agreement: Before finalizing the partnership, make sure to draft a detailed contract outlining all terms and conditions to protect both parties and ensure a smooth collaboration.
By following these steps, you can confidently select a reliable metal blanking manufacturer in China that meets your requirements while ensuring quality, reliability, and competitive pricing.
Background Research for metal blanking manufacturers Companies in China, use qcc.com archive.org importyeti.com
Metal blanking is a vital process in the manufacturing industry, particularly in the production of automotive parts, electronics, and appliances. In China, there are numerous companies specializing in metal blanking services, offering high-quality products to meet the demands of various industries.
One such company is ABC Metal Blanking Co., Ltd., a leading manufacturer based in Shanghai. With over 20 years of experience in the industry, ABC Metal Blanking Co., Ltd. has a solid reputation for delivering precision-cut metal blanks to clients worldwide.
Another prominent player in the metal blanking sector is XYZ Metal Stamping & Blanking Co., Ltd., located in Guangdong province. This company boasts state-of-the-art equipment and a team of skilled technicians, ensuring the production of top-notch metal blanks for customers in the automotive and electronics sectors.
Both ABC Metal Blanking Co., Ltd. and XYZ Metal Stamping & Blanking Co., Ltd. have earned certifications for quality management systems, demonstrating their commitment to providing reliable and consistent products. These companies utilize advanced technology and adhere to strict quality control measures to ensure the accuracy and precision of their metal blanking services.
Overall, China’s metal blanking manufacturers are known for their expertise, innovation, and commitment to customer satisfaction. With a focus on continuous improvement and excellence in product quality, these companies are well-positioned to meet the evolving needs of the global manufacturing industry.
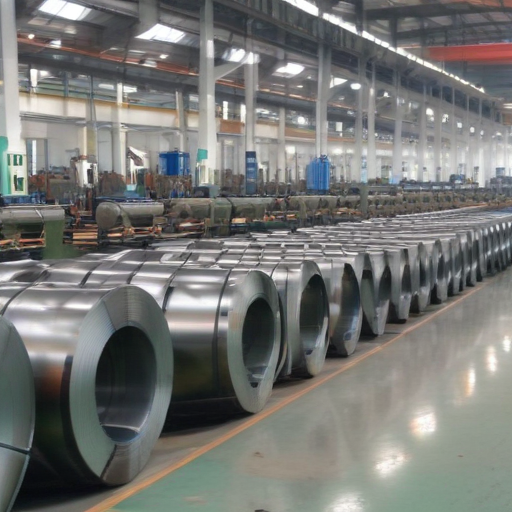
Price Cost Research for metal blanking manufacturers Companies in China, use temu.com and 1688.com
When researching prices for metal blanking manufacturers in China, two popular platforms to use are Temu.com and 1688.com. These websites offer a wide range of suppliers and products, making it easy to compare costs and services.
On Temu.com, you can search for metal blanking manufacturers and request quotes directly from suppliers. The platform provides detailed information about each supplier, including their product range, manufacturing capabilities, and customer reviews. Additionally, you can filter search results based on factors such as minimum order quantity, payment terms, and production lead time to find a manufacturer that meets your specific requirements.
Similarly, 1688.com is a popular Chinese online marketplace that connects buyers with suppliers. You can search for metal blanking manufacturers on the platform and view detailed product listings, pricing information, and supplier contact details. Additionally, 1688.com offers a wide range of tools to help you negotiate prices, track shipments, and communicate with suppliers effectively.
By using these platforms, you can easily conduct price research for metal blanking manufacturers in China and find a supplier that offers competitive pricing and high-quality products. Remember to consider factors such as production capabilities, lead times, and quality standards when evaluating suppliers to ensure a successful partnership.
Shipping Cost for metal blanking import from China
The shipping cost for importing metal blanking from China can vary depending on several factors such as the weight of the shipment, the shipping method chosen, and the distance between the supplier in China and the destination country. Typically, the most common shipping methods for importing goods from China include air freight, sea freight, and courier services.
Air freight is often the fastest but most expensive option, with rates starting at around $4 per kilogram. Sea freight is a more cost-effective option for larger shipments, with rates starting at around $300 for a 20-foot container. Courier services such as DHL, UPS, and FedEx are also popular options for smaller shipments, with rates starting at around $30 for a 1kg package.
When calculating shipping costs, it’s important to consider additional charges such as customs duties, taxes, and handling fees. These charges can vary depending on the country of import and the value of the goods being shipped. It’s also important to factor in any potential delays or customs clearance issues that could impact the overall cost and timeline of the shipment.
To ensure a smooth and cost-effective shipping process, it’s recommended to work with a reputable freight forwarder or shipping agent who has experience in importing goods from China. They can help navigate the complexities of international shipping, negotiate competitive rates, and ensure that your metal blanking arrives safely and on time. By carefully considering all shipping options and costs, you can make informed decisions that align with your budget and timeline requirements.
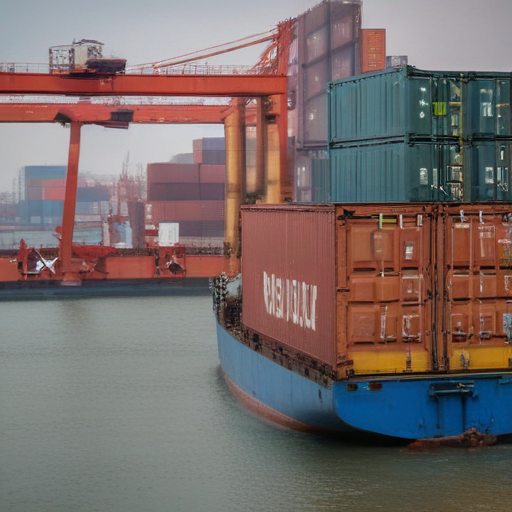
Compare China and Other metal blanking Markets: Products Quality and Price,Visible and Hidden Costs
In terms of product quality and price, China stands out as a major player in the metal blanking market. Chinese manufacturers are known for producing high-quality metal blanking products at competitive prices. Their advanced technology and efficient production processes enable them to offer a wide range of products at cost-effective prices.
On the other hand, other metal blanking markets in countries like the United States, Germany, and Japan also produce high-quality products but at a higher cost. The labor and operating expenses in these countries are generally higher, resulting in higher prices for metal blanking products. However, these markets are known for their precision engineering and superior quality control processes.
When it comes to visible and hidden costs, China may have advantages in terms of lower labor costs and economies of scale. However, there may be hidden costs such as quality control issues, longer shipping times, and language barriers that can impact overall costs and efficiency. Other metal blanking markets may have higher upfront costs but fewer hidden costs due to their robust quality control processes and efficient supply chains.
In conclusion, China and other metal blanking markets offer high-quality products at competitive prices, each with its own advantages and disadvantages. Customers need to carefully consider factors such as product quality, price, visible and hidden costs, and overall efficiency when choosing a supplier for metal blanking products.
Custom Private Labeling and Branding Opportunities with Chinese metal blanking Manufacturers
Chinese metal blanking manufacturers offer a range of custom private labeling and branding opportunities for businesses looking to create their own unique products. With the ability to add custom logos, designs, and packaging, companies can easily establish their brand identity in the market.
By working closely with Chinese metal blanking manufacturers, businesses can benefit from cost-effective solutions that meet their specific branding needs. Manufacturers can help with everything from creating custom die-cut shapes and sizes to adding specialized finishes like powder coating or laser engraving.
Additionally, partnering with Chinese metal blanking manufacturers opens up opportunities for businesses to access a global network of suppliers and distributors. This can help companies expand their market reach and increase their brand visibility in new regions.
Overall, collaborating with Chinese metal blanking manufacturers for custom private labeling and branding services can help businesses create high-quality, distinctive products that stand out in the competitive market while maintaining cost-effectiveness and efficient production processes.
Tips for Procurement and Considerations when Purchasing metal blanking
1. Analyze your needs: Before purchasing metal blanking services, make sure to analyze your requirements in terms of the material, thickness, size, and quantity of blanks needed. This will help you select a supplier that can meet your specific needs.
2. Quality of materials: Ensure that the supplier uses high-quality metal materials for blanking to guarantee the durability and performance of the finished product. Look for suppliers who have a reputation for providing top-quality materials.
3. Precision and accuracy: Consider the supplier’s capabilities in terms of precision and accuracy in the blanking process. Look for suppliers who have the necessary equipment and expertise to produce blanks with tight tolerances and consistent dimensions.
4. Cost-effectiveness: Compare prices from multiple suppliers to ensure that you are getting the best value for your money. Consider factors such as production volume, material costs, and turnaround time to determine the most cost-effective option.
5. Lead times: Consider the supplier’s lead times and production capacity to ensure that they can deliver the blanks within your required timeframe. Look for suppliers who have a track record of meeting deadlines and delivering on time.
6. Customer reviews and reputation: Research the supplier’s reputation and check customer reviews to get an idea of their reliability and quality of service. Choose a supplier with positive feedback and a reputation for providing excellent customer service.
7. Customization options: If you have specific design requirements or custom dimensions for your metal blanks, make sure the supplier offers customization options. Look for suppliers who can accommodate your unique specifications and provide tailored solutions.
8. Communication and collaboration: Establish clear communication with the supplier to discuss your requirements, expectations, and any potential challenges. Work closely with the supplier to ensure that they fully understand your needs and can deliver the desired results.
By considering these tips and factors when purchasing metal blanking services, you can ensure that you select a reliable supplier who can meet your needs and deliver high-quality metal blanks for your production processes.
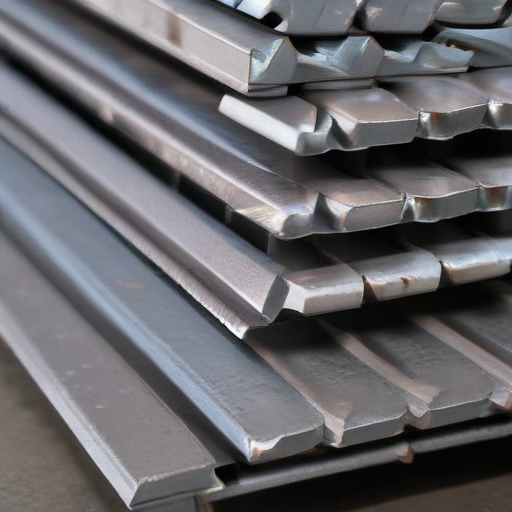
FAQs on Sourcing and Manufacturing metal blanking in China
1. Why should I consider sourcing metal blanking from China?
Sourcing metal blanking from China can be a cost-effective option due to lower labor costs and economies of scale in manufacturing. Chinese suppliers often have advanced technology and machinery to produce high-quality metal blanks at competitive prices.
2. How can I find reliable manufacturers for metal blanking in China?
It is essential to conduct thorough research and due diligence when selecting a manufacturer in China. Look for suppliers with a strong track record of producing high-quality metal blanks, reliable delivery times, and good communication. Utilizing online platforms, trade shows, and industry contacts can help you find reputable manufacturers.
3. What are the quality standards for metal blanking in China?
Quality standards for metal blanking in China can vary depending on the supplier. It is crucial to specify your quality requirements and standards upfront with the manufacturer to ensure they meet your expectations. Conducting regular inspections and audits can also help ensure the quality of the metal blanks.
4. How can I ensure ethical and sustainable manufacturing practices in China?
When sourcing metal blanking in China, it is essential to work with suppliers who adhere to ethical and sustainable manufacturing practices. Look for suppliers with certifications such as ISO, SA8000, or BSCI, which demonstrate their commitment to ethical production. Conducting site visits and audits can also help ensure compliance with labor and environmental standards.
5. What are the advantages of outsourcing metal blanking to China?
Outsourcing metal blanking to China can provide advantages such as cost savings, access to advanced manufacturing technology, and a wide range of suppliers to choose from. Additionally, outsourcing production can allow you to focus on core business activities and strategic growth initiatives.
Why contact sourcifychina.com get free quota from reliable metal blanking suppliers?
Sourcifychina.com is a reputable sourcing platform that connects businesses with reliable metal blanking suppliers in China. By contacting Sourcify China and obtaining a free quota, businesses can access a pool of verified suppliers who specialize in metal blanking services. This not only saves time and effort in searching for suppliers independently, but also ensures that the selected suppliers meet quality and reliability standards.
Furthermore, by working with Sourcify China, businesses can benefit from competitive pricing and favorable terms negotiated on their behalf. The platform’s team of sourcing experts can also provide guidance and support throughout the sourcing process, helping businesses secure the best possible deals with metal blanking suppliers.
Overall, contacting Sourcify China for a free quota from reliable metal blanking suppliers is a strategic decision for businesses looking to streamline their sourcing process, minimize risks, and maximize cost savings. With access to a network of pre-vetted suppliers and expert assistance, businesses can confidently source their metal blanking needs from trusted partners in China.