Top sheet metal bending techniques in China introduce,list main products and website if have
Sheet metal bending is a common technique used in the manufacturing industry, especially in China where there is a high demand for precision metal products. Some of the top sheet metal bending techniques used in China include:
1. Press Brake Bending: This technique uses a press brake machine to apply force to bend the metal sheet at specific angles. It is widely used for creating complex shapes and precise bends.
2. Roll Bending: In this technique, the metal sheet is passed through a series of rollers to achieve a curved or round shape. It is commonly used for producing cylindrical or conical components.
3. Rotary Bending: Also known as rotary draw bending, this technique involves clamping the metal sheet at both ends and rotating it around a die to create bends. It is suitable for producing tight radius bends.
Some of the main products produced using sheet metal bending techniques in China include automotive parts, electronic enclosures, household appliances, and construction components.
One of the leading sheet metal bending manufacturers in China is Suzhou Huahong Precision Metal Co., Ltd. Their website, https://www.szhhm.com/, showcases their range of products and services in precision sheet metal bending and fabrication.
Another prominent company specializing in sheet metal bending in China is Shenzhen Runze Hardware Technology Co., Ltd. They offer a wide range of sheet metal bending services for various industries. Their website, https://www.runzehardware.com/, provides more information on their capabilities and products.
Overall, sheet metal bending techniques play a crucial role in the manufacturing sector in China, and companies like Suzhou Huahong Precision Metal Co., Ltd. and Shenzhen Runze Hardware Technology Co., Ltd. are at the forefront of providing high-quality bending solutions to meet the diverse needs of their customers.
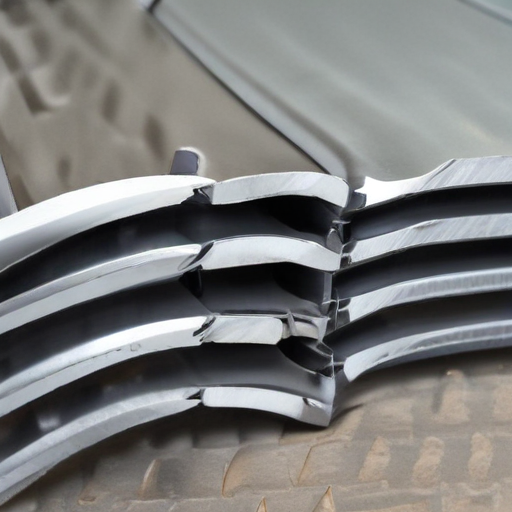
Types of sheet metal bending techniques
Sheet metal can be bent using various techniques to form different shapes and structures. Some common sheet metal bending techniques include:
1. V-bending: In this technique, a V-shaped die is used to bend the metal sheet at a specific angle. The metal is placed between the die and a punch that presses the metal into the die to create the bend.
2. U-bending: Similar to V-bending, this technique uses a U-shaped die to bend the sheet metal into a U-shaped curve. The metal is placed between the die and a punch and then pressed to form the desired shape.
3. Roll bending: This technique involves passing the sheet metal through a series of rollers that gradually bend the metal into a curved or cylindrical shape. Roll bending is often used to create tubes, cylinders, or curved sections.
4. Air bending: In this technique, the sheet metal is placed between a punch and a die, but the punch does not touch the metal. Instead, the metal is bent by applying pressure to the sides of the sheet, allowing for greater flexibility in bending angles.
5. Press brake bending: Press brake bending involves using a press brake machine to bend the sheet metal at precise angles. The metal is clamped between a punch and a die, and a hydraulic press exerts pressure on the metal to create the bend.
Other techniques include hammering, folding, and rotary bending, each with its own advantages and applications. The choice of bending technique depends on factors such as the desired bend angle, bend radius, material thickness, and production volume.
Overall, sheet metal bending techniques play a crucial role in manufacturing processes, allowing for the creation of a wide range of structural components and products. Proper selection and execution of bending techniques are essential for achieving accurate and high-quality bends in sheet metal fabrication.
Pros and Cons of Using sheet metal bending techniques
Pros:
1. Versatility: Sheet metal bending can be used to create a wide variety of shapes and components, making it a versatile technique for a range of applications.
2. Cost-effective: Sheet metal bending is a cost-effective manufacturing process, as it requires minimal tooling and equipment compared to other manufacturing methods.
3. Strength and durability: Bending sheet metal increases its strength and durability, making it a suitable choice for applications that require sturdy and long-lasting components.
4. Precision: With the use of computer numerical control (CNC) machines, sheet metal bending can achieve high levels of precision, ensuring consistent and accurate results.
5. Speed: Sheet metal bending can be a fast process, allowing for quick turnaround times and efficient production.
Cons:
1. Limitations in shape complexity: Sheet metal bending may not be suitable for creating highly intricate or complex shapes, as it is primarily used for forming simple bends and curves.
2. Material limitations: Certain types of sheet metal may be difficult to bend or may not be suitable for bending techniques, limiting the range of materials that can be used.
3. Tooling costs: While sheet metal bending is generally cost-effective, there may be initial costs associated with purchasing or setting up the necessary tooling and equipment.
4. Risk of deformation: Improper bending techniques or incorrect tooling settings can lead to deformation or defects in the sheet metal, requiring rework or additional manufacturing processes.
5. Environmental impact: Sheet metal bending produces waste material in the form of scrap metal, which may need to be disposed of properly to minimize environmental impact.
sheet metal bending techniques Reference Specifications (varies for different product)
Sheet metal bending is a common technique used in metal fabrication to create a variety of products such as enclosures, brackets, and components for various industries. There are several bending techniques that can be used to achieve different angles and shapes in sheet metal.
One of the most commonly used bending techniques is V-bending, where the sheet metal is bent between a punch and a die to create a V-shaped bend. This technique is often used for creating sharp angles and precise bends. Another technique is edge bending, where the sheet metal is bent along the edge of a flat surface to create a straight bend. This technique is commonly used for creating flanges and channels in sheet metal.
Other bending techniques include roll bending, where the sheet metal is passed through a series of rollers to create a curved bend, and rotary bending, where the sheet metal is bent around a rotary die to create complex shapes and curves. Each bending technique has its own advantages and limitations, depending on the specific requirements of the product being fabricated.
When working with sheet metal bending, it is important to refer to the specifications provided for the product being fabricated. These specifications may include the desired bend angle, radius, and tolerances that need to be achieved. By following these specifications and using the appropriate bending techniques, sheet metal fabricators can produce high-quality products with accurate and consistent bends.
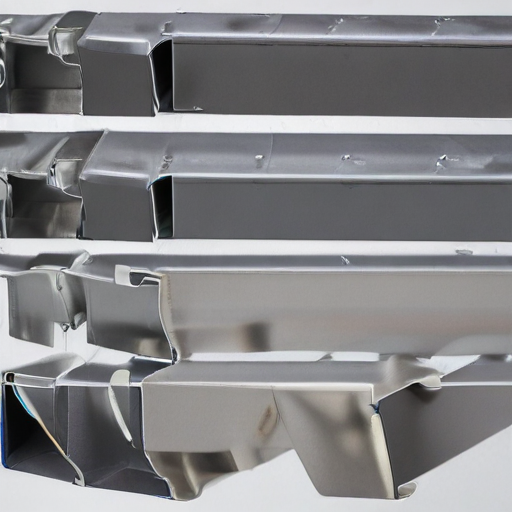
Applications of sheet metal bending techniques
Sheet metal bending techniques are commonly used in the manufacturing industry for a variety of applications. One common application is in the fabrication of metal enclosures, such as those used in electrical enclosures, control panels, and machinery housings. By bending sheet metal into specific shapes and angles, manufacturers can create custom enclosures that meet the specific requirements of their products.
Another application of sheet metal bending techniques is in the production of automotive components. Sheet metal parts such as brackets, brackets, brackets, brackets, brackets, brackets, brackets, brackets, brackets, and brackets, brackets, brackets, brackets, brackets, brackets, brackets, brackets, brackets, brackets.
Sheet metal bending techniques are also used in the construction industry for making architectural elements such as metal roofing, siding, and flashing. By bending sheet metal into precise shapes and profiles, architects and designers can create unique and visually appealing building components that enhance the overall aesthetic of a structure.
In addition, sheet metal bending techniques are used in the production of furniture, appliances, and other consumer goods. By bending sheet metal into specific shapes and configurations, manufacturers can create durable and functional products that meet the demands of consumers.
Overall, sheet metal bending techniques are versatile and widely used in various industries for a wide range of applications. Whether it’s for creating custom enclosures, automotive components, architectural elements, or consumer goods, sheet metal bending techniques play a crucial role in the manufacturing process.
Material of sheet metal bending techniques
Sheet metal bending is a common fabrication technique used to create various products such as enclosures, brackets, and panels. The most common materials for sheet metal bending include steel, aluminum, and stainless steel.
There are several techniques used for bending sheet metal, each offering different advantages and limitations. The most common methods include:
1. Air bending: Air bending is a versatile method that uses a punch and die to bend the metal around a radius. This technique is ideal for creating simple bends with a wide range of angles.
2. Coining: Coining is a precise bending technique that uses a punch and die to bend the metal with high accuracy. This method is often used for creating complex, precise bends with tight tolerances.
3. Bottoming: Bottoming is a technique that uses a die with a V-shaped groove to bend the metal to a specific angle. This method is ideal for creating sharp, straight bends.
4. Roll bending: Roll bending is a method that uses a series of rollers to gradually bend the metal into a curved shape. This technique is often used for creating cylindrical or conical shapes.
Regardless of the bending technique used, it is important to ensure that the sheet metal is properly supported and clamped during the bending process to prevent deformation. Additionally, choosing the right tooling and equipment for the specific material and thickness of the sheet metal is crucial for achieving accurate and consistent results.
In conclusion, there are several techniques for bending sheet metal, each offering unique advantages depending on the desired outcome. By understanding the properties of the material and selecting the appropriate bending technique, manufacturers can create high-quality products with precision and efficiency.
Quality Testing Methods for sheet metal bending techniques and how to control the quality
There are several quality testing methods that can be used to ensure the accuracy and precision of sheet metal bending techniques.
One common method is visual inspection, where the bent part is compared to a template or drawing to check for any deviations in dimensions or angles. This can be done using tools such as calipers or protractors.
Another method is using a coordinate measuring machine (CMM) to accurately measure the dimensions and angles of the bent parts. This can provide precise data on the accuracy of the bending technique.
Additionally, a bend test can be performed to check the ductility and strength of the bent part. This involves bending a sample piece to a specified angle or radius and checking for any cracks or defects.
To control the quality of sheet metal bending techniques, it is important to establish and follow strict guidelines and procedures. This includes using the correct tools and equipment, as well as ensuring that the operators are properly trained and skilled in the bending process.
Regular maintenance and calibration of bending equipment is also essential to ensure consistent results. Additionally, performing regular quality checks and inspections throughout the bending process can help to identify any issues or defects early on.
Overall, by using a combination of quality testing methods and implementing strict quality control measures, sheet metal bending techniques can be effectively monitored and controlled to ensure high-quality and accurate results.
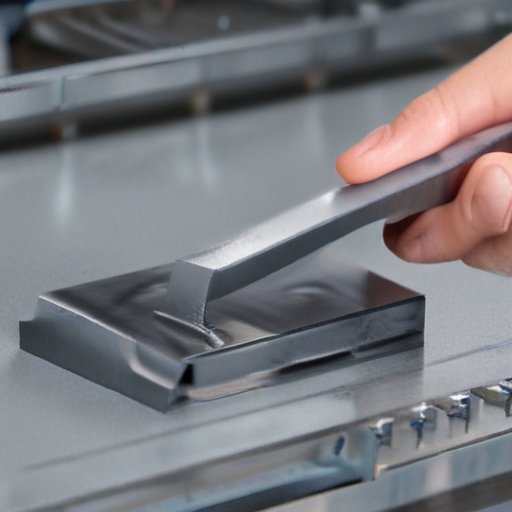
The Work Process and how to use sheet metal bending techniques
Sheet metal bending is a common process used to create various shapes and forms from flat metal sheets. The process involves folding or forming the metal along a straight axis to create bends, angles, curves, and complex shapes.
To begin the bending process, you will need a few essential tools and equipment including a metal brake, which is a machine used to bend the metal, as well as measuring tools, clamps, and safety equipment such as gloves and goggles.
The first step is to measure and mark the bending lines on the metal sheet using a ruler and a scribe. Make sure to make accurate measurements and marks to ensure precise bending.
Next, place the metal sheet into the metal brake, aligning the bending line with the bending edge of the brake. Secure the metal sheet in place using clamps to prevent it from shifting during the bending process.
Using the handles of the metal brake, slowly apply pressure to gradually bend the metal sheet along the bending line. Check the angle and shape of the bend frequently to ensure it meets your desired specifications.
Once the bending process is complete, release the clamps and remove the bent metal sheet from the brake. Use a deburring tool or sandpaper to smooth out any rough edges or burrs left from the bending process.
Sheet metal bending techniques can vary based on the complexity and shape of the desired form. Practice and experiment with different bending methods and angles to achieve the desired results.
Overall, sheet metal bending is a versatile and essential process in metalworking, allowing for the creation of a wide range of structures and components. With the right tools and techniques, you can achieve precise and professional-looking bends in your sheet metal projects.
sheet metal bending techniques Importing questions including Cost,Supplier,Sample,Certification and Market
When considering sheet metal bending techniques, there are several important factors to keep in mind.
Cost: The cost of sheet metal bending can vary depending on the complexity of the bend, the thickness and grade of the metal, and the equipment needed for the job. It is important to get quotes from multiple suppliers to ensure you are getting the best price.
Supplier: Finding a reliable and high-quality supplier for your sheet metal bending needs is crucial. Look for a supplier with a good reputation, experience in the industry, and a track record of meeting deadlines.
Sample: Before committing to a large order, it is a good idea to request a sample of the bent metal to ensure it meets your specifications and requirements. This will also give you a chance to test the quality and durability of the bend.
Certification: Depending on the industry you are in, you may require certification for the sheet metal bending process. Make sure your supplier is able to provide the necessary certifications and meets any specific industry standards.
Market: Understanding the market demand for your sheet metal products is important when considering sheet metal bending techniques. Make sure there is a market for the products you are producing and that you can compete effectively with other suppliers.
In conclusion, when considering sheet metal bending techniques, it is important to consider factors such as cost, supplier reliability, sample testing, certification requirements, and market demand. By carefully evaluating these factors, you can ensure that your sheet metal bending process is successful and meets your specific needs and requirements.
How to find and select check reliable sheet metal bending techniques manufacturers in China
When looking for reliable sheet metal bending techniques manufacturers in China, you can start by doing some research online. Look for manufacturers with a good reputation and positive reviews from previous customers. You can also check with industry specific directories and trade shows to find potential manufacturers.
Once you have identified a few potential manufacturers, it is important to verify their credentials. Make sure they have the necessary certifications and qualifications to produce quality sheet metal bending techniques. You can also ask for samples of their work to assess the quality of their products.
When selecting a manufacturer, it is important to consider factors such as pricing, lead times, and communication. Make sure you are comfortable with their terms and conditions before making a decision. It is also a good idea to visit the manufacturer in person if possible to get a better understanding of their operations and capabilities.
Overall, it is important to do thorough research and due diligence when selecting a sheet metal bending techniques manufacturer in China to ensure you are working with a reliable and trustworthy partner.
Background Research for sheet metal bending techniques manufacturers Companies in China, use qcc.com archive.org importyeti.com
Sheet metal bending is a common manufacturing process that involves shaping a metal sheet into a desired angle or shape using equipment like press brakes or other bending machines. In China, there are several companies specializing in sheet metal bending techniques.
One such company is Shenzhen Runze Hardware Technology Co., Ltd. This company has expertise in precision sheet metal fabrication, including bending techniques. They offer services such as laser cutting, punching, bending, and welding, catering to various industries like electronics, telecommunications, and automotive.
Another notable company is Dongguan Fuzhan Electronic Technology Co., Ltd. They provide custom sheet metal bending solutions for a wide range of applications, utilizing advanced equipment and techniques to ensure high precision and quality. Their services include sheet metal cutting, bending, welding, and surface treatment.
Yantai Yogy Precision Metal Products Co., Ltd. is also a prominent player in the sheet metal bending industry in China. They specialize in precision sheet metal fabrication, offering services like CNC punching, bending, welding, and assembly. Their expertise lies in producing complex and intricate sheet metal components for sectors like aerospace, medical, and electronics.
Overall, these companies are known for their proficiency in sheet metal bending techniques and offer comprehensive solutions to meet the diverse needs of the manufacturing industry in China.
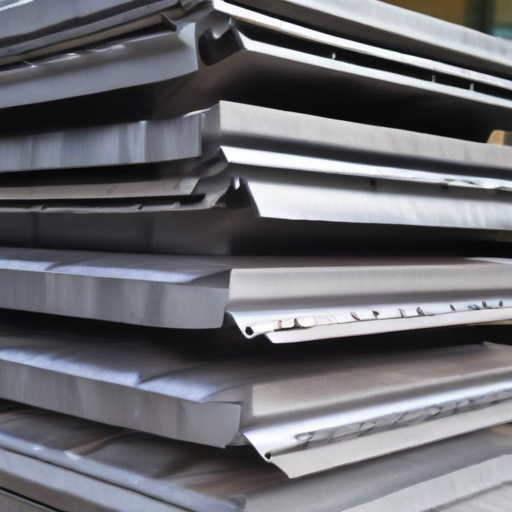
Price Cost Research for sheet metal bending techniques manufacturers Companies in China, use temu.com and 1688.com
When researching price costs for sheet metal bending techniques manufacturers in China, two popular online platforms to use are temu.com and 1688.com. These websites offer a wide range of suppliers and manufacturers specializing in sheet metal bending services.
To begin your search, input specific keywords related to sheet metal bending techniques into the search bar on both websites. You can also filter the results based on your desired location, price range, and other relevant criteria.
Upon finding potential manufacturers, reach out to them directly through the platform’s messaging system to inquire about their pricing structures. Be sure to provide details about your specific project requirements, such as material type, thickness, and quantity, to receive accurate quotes.
In addition, compare quotes from multiple manufacturers to ensure you are getting competitive pricing. Some manufacturers may offer bulk discounts or other incentives depending on the scale of your project.
Overall, using temu.com and 1688.com can provide you with valuable insights into the pricing of sheet metal bending techniques manufacturers in China. By conducting thorough research and reaching out to multiple suppliers, you can find a manufacturer that meets your quality standards and budget requirements.
Shipping Cost for sheet metal bending techniques import from China
When importing sheet metal bending techniques from China, the shipping costs can vary depending on several factors such as the weight and dimensions of the products, the shipping method chosen, and the distance between the supplier in China and the destination.
Typically, for smaller and lighter packages, air shipping is a fast but more expensive option. Prices can range from $5 to $15 per kilogram. For larger and heavier shipments, sea freight is a more cost-effective option, with prices starting at around $800 for a full container.
Additionally, the shipping costs may also include additional charges such as customs duties, import taxes, and handling fees. It is important to factor in these extra costs when calculating the total shipping expenses.
To reduce shipping costs, it is advisable to negotiate with the supplier for better rates or explore different shipping options such as consolidating shipments with other orders or using a freight forwarder to manage the logistics. It is also recommended to plan ahead and place orders well in advance to avoid rush delivery fees.
Overall, by carefully considering the various factors that influence shipping costs and exploring different strategies to reduce expenses, importing sheet metal bending techniques from China can be a cost-effective and efficient process.
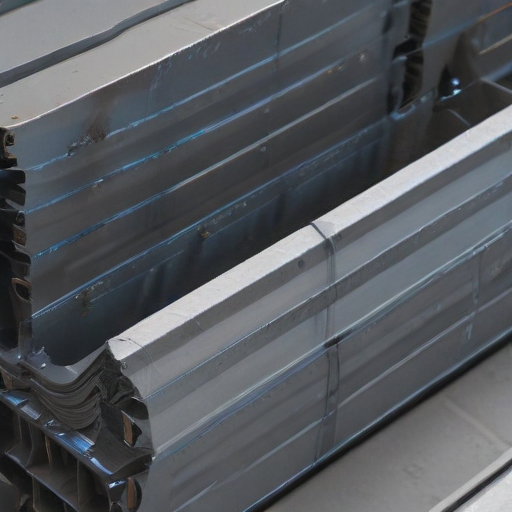
Compare China and Other sheet metal bending techniques Markets: Products Quality and Price,Visible and Hidden Costs
China is known for its competitive sheet metal bending techniques market, offering a wide range of products at varying quality and price points. The country has a strong manufacturing industry and is able to produce large quantities of sheet metal products quickly and affordably. However, the quality of these products can vary, with some Chinese manufacturers offering lower quality materials and finishes compared to other markets.
In terms of price, China generally offers lower cost sheet metal bending techniques compared to other markets such as the United States or Europe. This is due to lower labor costs and economies of scale in China’s manufacturing industry. However, customers should be aware of hidden costs such as shipping fees, import tariffs, and potential delays in production or delivery times when working with Chinese manufacturers.
In comparison, other markets such as the United States or Europe may offer higher quality sheet metal bending techniques at a higher price point. These markets are known for their strict quality control measures and use of higher quality materials, resulting in a more durable and aesthetically pleasing final product. However, customers will likely pay a premium for these products compared to those made in China.
Overall, customers should carefully weigh the trade-offs between product quality, price, and potential hidden costs when considering sheet metal bending techniques from China versus other markets. It is important to conduct thorough research and due diligence when selecting a supplier to ensure that the final product meets the desired specifications and expectations.
Custom Private Labeling and Branding Opportunities with Chinese sheet metal bending techniques Manufacturers
If you are looking for custom private labeling and branding opportunities with Chinese sheet metal bending techniques manufacturers, you have come to the right place. With years of experience in the industry, our manufacturing partners have the expertise and capabilities to help you create a unique and eye-catching product that will stand out in the market.
Whether you are looking to launch a new product line or enhance an existing one, our manufacturers can work with you to develop custom designs that meet your specific requirements. From product development to packaging and branding, we can help you every step of the way to ensure that your vision becomes a reality.
With state-of-the-art equipment and skilled craftsmen, our manufacturers can produce high-quality sheet metal products with precision and efficiency. From simple bends to complex shapes, we have the capabilities to handle a wide range of projects and deliver exceptional results.
By partnering with us, you can take advantage of our extensive network of suppliers and access to cost-effective materials, allowing you to create custom products that are both high-quality and competitively priced.
Don’t miss out on this opportunity to elevate your brand and expand your product offerings with the help of our experienced manufacturers. Contact us today to learn more about our private labeling and branding services and how we can help you achieve your business goals.
Tips for Procurement and Considerations when Purchasing sheet metal bending techniques
When purchasing sheet metal bending techniques, there are several factors to consider to ensure you get the best value for your money:
1. Quality of the equipment: It is important to invest in high-quality sheet metal bending equipment that is durable and long-lasting. Look for machines that are made from high-grade materials and have a reputation for reliability.
2. Precision and accuracy: The accuracy of the bending techniques is critical in producing high-quality finished products. Look for equipment that offers precise bending angles and consistent results.
3. Capacity and size: Consider the size and capacity of the sheet metal bending equipment to ensure it can handle the size of the metal sheets you will be working with. Make sure the machine can bend the required thickness of the metal.
4. Ease of use: Choose equipment that is user-friendly and easy to operate. Look for machines with intuitive controls and features that simplify the bending process.
5. Cost: Consider your budget and look for sheet metal bending techniques that offer the best value for money. Compare prices from different manufacturers and suppliers to find the most cost-effective option.
6. Maintenance and support: Ensure that the equipment you purchase comes with a warranty and that there is adequate support and maintenance services available. This will help ensure the longevity and reliability of your bending equipment.
By taking these considerations into account, you can make an informed decision when purchasing sheet metal bending techniques that meet your production needs and budget requirements.
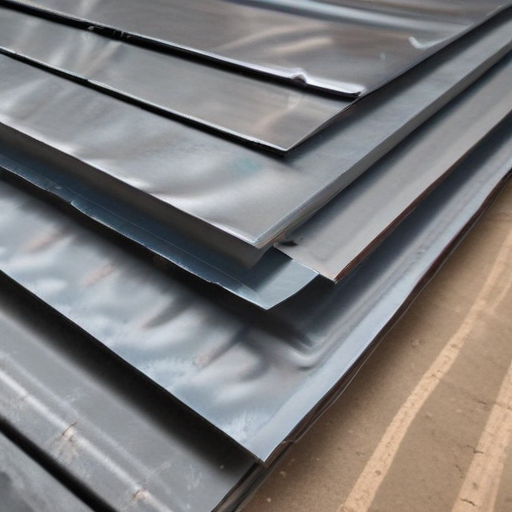
FAQs on Sourcing and Manufacturing sheet metal bending techniques in China
1. What are the common sheet metal bending techniques used in China?
In China, the most common sheet metal bending techniques include press brake bending, roll bending, and stretch bending. Press brake bending is widely used for simple bends, while roll bending is suitable for cylindrical shapes. Stretch bending is employed for forming complex shapes with tight tolerances.
2. How can I source sheet metal bending services in China?
To source sheet metal bending services in China, you can start by researching and contacting reputable manufacturers or suppliers. Online platforms such as Alibaba, Made-in-China, and Global Sources can also help you connect with potential partners. It is essential to communicate your specific requirements and quality standards to ensure the chosen supplier can meet your needs.
3. What factors should I consider when selecting a sheet metal bending manufacturer in China?
When selecting a sheet metal bending manufacturer in China, factors to consider include the manufacturer’s experience and expertise in sheet metal bending, their production capacity, quality control measures, pricing, lead times, and communication skills. It is also essential to inquire about their equipment, certifications, and past projects to evaluate their capabilities.
4. Can I visit the manufacturer’s facility in China before placing an order?
Yes, many manufacturers in China welcome site visits from potential customers. Visiting the manufacturer’s facility allows you to assess their production capabilities, quality control processes, and working conditions. It also helps build trust and establish a strong relationship with the supplier before placing an order.
5. How can I ensure quality control when manufacturing sheet metal bending products in China?
To ensure quality control when manufacturing sheet metal bending products in China, it is crucial to establish clear specifications and quality standards from the beginning. Regular communication with the manufacturer, conducting factory inspections, and implementing third-party quality inspections can help maintain product quality and consistency. Collaboration with reliable suppliers and maintaining open communication throughout the production process is key to achieving satisfactory results.
Why contact sourcifychina.com get free quota from reliable sheet metal bending techniques suppliers?
Sourcifychina.com is a highly reputable platform that connects businesses with trustworthy and reliable sheet metal bending techniques suppliers in China. By contacting Sourcifychina.com, you can access a free quota from these suppliers, allowing you to benefit from their expertise and cost-effective solutions.
Sheet metal bending techniques are crucial in the manufacturing industry, as they are used to shape metal sheets into various components and products. Working with reliable suppliers ensures that you receive high-quality results that meet your specifications and standards.
When you request a free quota from Sourcifychina.com, you can tap into their network of experienced suppliers who specialize in sheet metal bending techniques. These suppliers have the necessary equipment, skills, and knowledge to deliver precise bends and shapes with quick turnaround times.
By partnering with reputable suppliers through Sourcifychina.com, you can streamline your production process, reduce costs, and improve the overall quality of your products. With a free quota from reliable suppliers, you can make informed decisions about your sheet metal bending needs and achieve your business objectives efficiently.
In conclusion, contacting Sourcifychina.com to get a free quota from reliable sheet metal bending techniques suppliers is a smart move for any business looking to enhance their manufacturing capabilities. Don’t miss out on this valuable opportunity to access top-notch services and expertise in sheet metal bending.