Top sheet metal fastening in China introduce,list main products and website if have
China is a hub for top sheet metal fastening products, offering a wide range of options to cater to various industrial needs. Some of the main products in this category include:
1. Self-clinching fasteners: These are specialized fasteners designed for permanent and flush mounting in thin metal sheets. They provide strong and reliable connections without the need for additional hardware.
2. Threaded inserts: Threaded inserts are used to create durable threads in metal sheets, allowing for secure fastening of bolts, screws, or other hardware.
3. Rivet nuts: Rivet nuts are similar to threaded inserts but provide a more permanent and robust fastening solution. They are commonly used in automotive and aerospace industries.
4. Standoffs: Standoffs are used to create space between two metal sheets, allowing for proper airflow, insulation, or cable management. They come in various shapes and sizes to suit different applications.
5. Weld nuts: Weld nuts are welded directly onto metal sheets, providing a strong and durable fastening solution. They are commonly used in automotive and construction industries.
One of the leading manufacturers of sheet metal fastening products in China is Dongguan Taimei Metal Products Co., Ltd. They offer a wide range of self-clinching fasteners, threaded inserts, rivet nuts, standoffs, weld nuts, and other sheet metal fastening solutions. Their website, https://www.taimeihardware.com/, provides more information about their products and services. With high-quality products and competitive pricing, Chinese manufacturers like Dongguan Taimei Metal Products Co., Ltd. are a reliable choice for top sheet metal fastening needs.
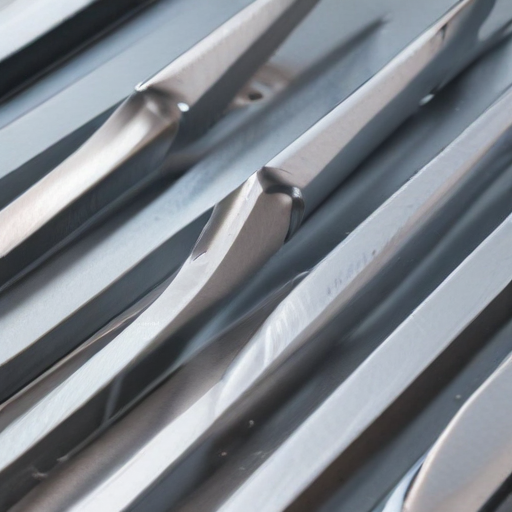
Types of sheet metal fastening
Sheet metal can be fastened in a variety of ways, depending on the specific application and requirements. Some common types of sheet metal fastening methods include:
1. Screws: Screws are a simple and effective way to fasten sheet metal. Self-tapping screws are commonly used for sheet metal applications, as they can create their own threads in the material. They are available in a variety of sizes and materials to suit different applications.
2. Rivets: Rivets are another popular fastening method for sheet metal. They are typically made of metal and consist of a cylindrical shaft with a head on one end. Rivets are inserted through pre-drilled holes in the sheet metal and then deformed to secure the joint. They provide strong and durable connections.
3. Welding: Welding is a permanent fastening method that involves melting the edges of the sheet metal and fusing them together. It creates a strong bond that is often used in structural applications where high strength is required. Different types of welding techniques, such as MIG (Metal Inert Gas) welding and TIG (Tungsten Inert Gas) welding, can be used depending on the specific requirements.
4. Clinching: Clinching is a fastening method that involves deforming the sheet metal to create a mechanical interlock. A special tool is used to press the two sheets of metal together, creating a strong and permanent connection. This method is often used in automotive and aerospace industries.
5. Adhesives: Adhesives can also be used to fasten sheet metal. Structural adhesives have high strength and can bond different materials together. They are often used in lightweight applications where welding or mechanical fasteners are not suitable.
In conclusion, there are various types of sheet metal fastening methods available, each with its own advantages and limitations. The choice of fastening method will depend on factors such as the application, material properties, and required strength of the joint. It is important to carefully consider these factors when selecting a fastening method for a particular sheet metal application.
Pros and Cons of Using sheet metal fastening
Sheet metal fastening is a common method used in various industries for connecting two or more sheet metal pieces together. Like any other technique, it has its pros and cons.
Pros:
1. Strength and durability: Sheet metal fastening creates a strong bond between two or more pieces of sheet metal, ensuring that they remain securely fastened together.
2. Quick and efficient: Sheet metal fastening is typically a faster process compared to welding or other joining methods, making it ideal for mass production.
3. Versatility: There are a variety of fastening options available for sheet metal, including screws, rivets, and bolts, allowing for flexibility in design and assembly.
4. Cost-effective: Sheet metal fastening can be a more cost-effective option compared to welding or other joining methods, as it requires less equipment and labor.
Cons:
1. Weakened material: Fastening can weaken the sheet metal material, as it creates holes or indentations in the metal that can compromise its structural integrity.
2. Limited joint strength: The strength of the joint created by fastening may not be as strong as that of a welded joint, especially in high-stress applications.
3. Corrosion risk: Fastening can create areas where moisture and corrosive substances can accumulate, leading to potential corrosion issues over time.
4. Additional maintenance: Fastened joints may require additional maintenance and inspections to ensure they remain secure and free from issues.
In conclusion, sheet metal fastening is a versatile and cost-effective method for joining sheet metal pieces together, but it may come with some drawbacks such as weakened material, limited joint strength, corrosion risk, and additional maintenance requirements. It is essential to carefully consider the specific requirements of the application when choosing a fastening method for sheet metal.
sheet metal fastening Reference Specifications (varies for different product)
Sheet metal fastening is a crucial process in joining together metal components in various industries such as automotive, aerospace, construction, and electronics. The choice of fastening method depends on the specific application and design requirements. Some common fastening methods for sheet metal include:
– Self-clinching fasteners: These fasteners are permanently installed into the sheet metal through a pressing or punching process, providing a strong and reliable connection. They come in various forms such as nuts, studs, and standoffs.
– Rivets: Rivets are commonly used to join two or more sheets of metal together. They are inserted through pre-drilled holes and then deformed to secure the sheets in place. Solid, blind, and tubular rivets are some of the common types used in sheet metal fastening.
– Screws and bolts: These fasteners are versatile and can be used in various applications to join sheet metal components. Self-tapping screws are commonly used for thin gauge sheet metal, while bolts and nuts are used for thicker sections.
– Welding: Welding is a common method for fastening sheet metal components together by melting and fusing the metal at the joint. Different welding techniques such as MIG, TIG, and spot welding can be used depending on the material and thickness of the sheet metal.
It is important to refer to specific product specifications and guidelines for the appropriate fastening method for a particular application. Factors such as material type, thickness, joint strength, and corrosion resistance should be considered when selecting the right fastening solution. Proper installation and quality control measures are essential to ensure the integrity and durability of the sheet metal joints.
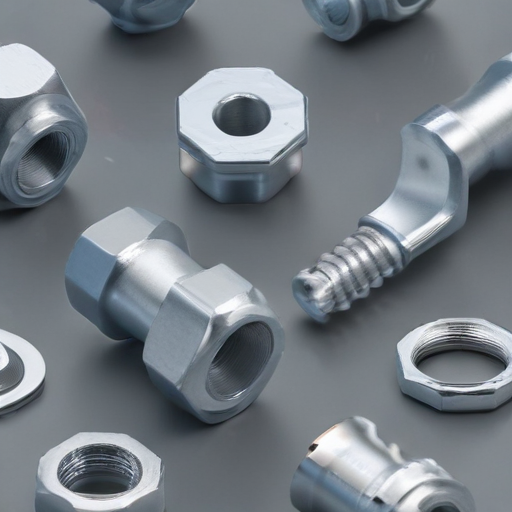
Applications of sheet metal fastening
Sheet metal fastening is a critical process used in many industries for joining two or more pieces of sheet metal together. This process is crucial in construction, automotive, aerospace, and manufacturing industries.
In automotive industry, sheet metal fastening is used for assembling car bodies, joining panels together, securing components, and creating structural components of vehicles. This process ensures that the parts are securely held together, providing strength and stability to the vehicle.
In construction industry, sheet metal fastening is used for joining metal roof panels, walls, and ductwork. Fastening methods such as screws, rivets, and bolts are employed to ensure that the structure is secure and durable.
In aerospace industry, sheet metal fastening is used for assembling aircraft structures, securing panels, and joining components together. The fastening must meet strict safety and performance standards to ensure the integrity of the aircraft.
In manufacturing industry, sheet metal fastening is used for assembling machinery, equipment, and appliances. Fastening methods such as welding, clinching, and adhesive bonding are used to join sheet metal components together efficiently.
Overall, sheet metal fastening plays a crucial role in various industries by providing a reliable and cost-effective method for joining sheet metal components. This process contributes to the strength, durability, and functionality of products, ensuring that they meet the required standards and specifications.
Material of sheet metal fastening
Sheet metal fastening is crucial for ensuring the durability and stability of various structures and products made from sheet metal. There are several common methods for fastening sheet metal, each with its own advantages and limitations.
One of the most popular methods of sheet metal fastening is through the use of screws or bolts. These fasteners are typically made from materials such as stainless steel, carbon steel, or aluminum, which provide excellent strength and corrosion resistance. Screws and bolts are commonly used to join sheets of metal together or to secure sheet metal components to a larger structure.
Another common method of sheet metal fastening is through the use of rivets. Rivets are small metal pins that are inserted into pre-drilled holes in the sheet metal and then deformed to create a tight and secure connection. Rivets are available in a variety of materials, including aluminum, steel, and copper, and offer the advantage of being relatively easy to install and providing a clean and finished appearance.
Welding is another popular method of sheet metal fastening, especially for joining thicker sheets of metal or for creating permanent connections. Welding involves melting the edges of the sheet metal together to create a strong bond. Common welding methods for sheet metal include MIG (Metal Inert Gas) welding, TIG (Tungsten Inert Gas) welding, and spot welding.
In conclusion, the choice of sheet metal fastening material and method will depend on factors such as the thickness of the metal, the required strength of the connection, and the overall aesthetic considerations. By selecting the appropriate fastening materials and techniques, manufacturers can ensure the long-term performance and reliability of sheet metal structures and products.
Quality Testing Methods for sheet metal fastening and how to control the quality
When it comes to quality testing methods for sheet metal fastening, there are several techniques that can be used to ensure the fastenings are strong, secure, and meet the required specifications. Some of the common testing methods include:
1. Tensile testing: This method involves applying a pulling force to the fastened joint to determine the strength of the connection. Tensile testing is commonly used to assess the tensile strength and ductility of the fastened joint.
2. Shear testing: Shear testing involves applying a perpendicular force to the fastened joint to test its resistance to shear stress. This method is often used to evaluate the fastening’s shear strength and durability.
3. Torque testing: Torque testing is used to assess the tightness of the fastened joint by measuring the amount of torque required to loosen or tighten the connection. This method helps ensure that the fastening is securely in place and will not come loose over time.
4. Visual inspection: In addition to mechanical testing, visual inspection is also crucial to ensure the quality of the fastened joint. Inspectors may look for signs of damage, deformation, or improper installation that could compromise the integrity of the connection.
To control the quality of sheet metal fastenings, it is important to establish clear specifications and standards for the fastening process. Regular quality audits and inspections should be conducted to ensure compliance with these standards. Training and certification programs for operators can also help ensure that fastenings are installed correctly and to the required specifications. Additionally, implementing a robust quality control system that includes regular testing, inspection, and documentation can help ensure that the quality of sheet metal fastenings is maintained at a high level.
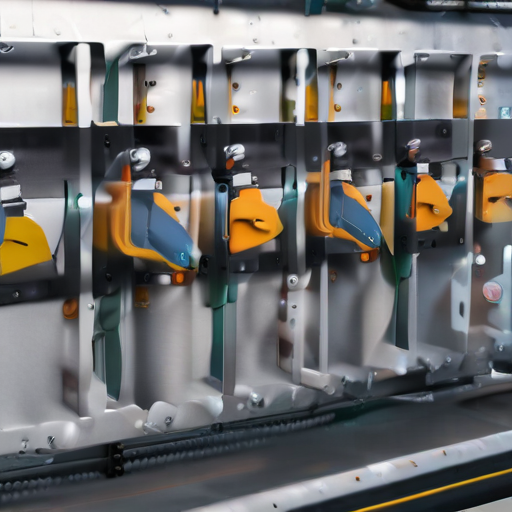
The Work Process and how to use sheet metal fastening
Sheet metal fastening is a crucial process in various industries like construction, automotive, and manufacturing. It is used to securely join two or more pieces of sheet metal together. There are several methods of sheet metal fastening, each with its own pros and cons. Some common methods include riveting, welding, bolting, and adhesive bonding.
To effectively fasten sheet metal, it is important to first ensure that the pieces to be joined are clean and free of any debris or contaminants. This will help create a strong bond between the surfaces. Next, carefully align the pieces and choose the appropriate fastening method based on factors like the metal thickness, joint strength, and aesthetic requirements.
For riveting, use a rivet gun to insert rivets through pre-drilled holes in the sheet metal. The rivet is then compressed to secure the pieces together. Welding involves melting and fusing the metal pieces together using heat. Bolting requires drilling holes and using bolts and nuts to hold the pieces in place. Adhesive bonding involves applying a special adhesive to the surfaces and allowing it to cure, creating a strong bond between the pieces.
Each method has its own advantages and limitations, so it is important to choose the right one for your specific application. Consider factors like the strength of the joint, the appearance of the finished product, and the required assembly time. By following these steps and choosing the appropriate fastening method, you can effectively join sheet metal pieces together for a wide range of applications.
sheet metal fastening Importing questions including Cost,Supplier,Sample,Certification and Market
When importing sheet metal fastening products, there are several important factors to consider:
1. Cost: It is crucial to research and compare prices from different suppliers to ensure you are getting a competitive price without compromising on quality.
2. Supplier: Choosing a reliable supplier is key to ensuring the quality of the products. Look for suppliers with a good reputation, experience in the industry, and positive reviews from other customers.
3. Sample: Before placing a bulk order, it is advisable to request samples from potential suppliers to assess the quality of the products firsthand. This will help you make an informed decision before making a larger investment.
4. Certification: Make sure the sheet metal fastening products you are importing meet the necessary certification standards and regulations for your market. This could include certifications such as ISO, CE, or RoHS.
5. Market: Research the market demand for sheet metal fastening products in your target market to ensure there is a demand for your imported products. Consider factors such as competition, consumer trends, and potential growth opportunities.
In summary, when importing sheet metal fastening products, it is important to consider factors such as cost, supplier reliability, sample assessment, certification requirements, and market demand to make informed decisions and ensure the success of your import venture.
How to find and select check reliable sheet metal fastening manufacturers in China
To find and select reliable sheet metal fastening manufacturers in China, start by conducting thorough research online. Look for reviews, testimonials, and ratings of different manufacturers to gauge their reputation and credibility. You can also use sourcing websites like Alibaba, Made-in-China, and Global Sources to find a list of potential manufacturers.
Once you have a list of potential manufacturers, contact them directly to inquire about their manufacturing capabilities, experience, quality control processes, and certifications. Ask for samples of their products to evaluate their quality and conduct a factory visit if possible to see their facilities firsthand.
When selecting a manufacturer, consider their production capacity, lead times, pricing, communication skills, and reliability. It is also important to discuss terms and conditions, payment terms, and any potential issues that may arise during the production process.
Be sure to ask for references from past clients and check their background to ensure they have a track record of delivering quality products on time. By thoroughly researching and vetting potential manufacturers, you can find a reliable sheet metal fastening manufacturer in China that meets your specific requirements and specifications.
Background Research for sheet metal fastening manufacturers Companies in China, use qcc.com archive.org importyeti.com
Sheet metal fastening manufacturers in China play a crucial role in the global manufacturing industry due to the country’s reputation for producing high-quality and cost-effective products. By utilizing platforms such as qcc.com, archive.org, and importyeti.com, we can gain insight into the background of these manufacturers.
Qcc.com is a comprehensive database that provides information on different companies, including sheet metal fastening manufacturers. By researching on this platform, we can access data such as company background, manufacturing capabilities, certifications, and customer reviews. This information can help us assess the reputation and reliability of the manufacturers.
Archive.org is a digital archive that stores historical data on websites. By accessing archives of the manufacturers’ websites, we can track their business history, evolution, and any changes in their products or services over time. This can give us a better understanding of the manufacturers’ experience and expertise in producing sheet metal fastening products.
Importyeti.com is a platform that provides data on import and export activities. By analyzing the export data of sheet metal fastening manufacturers in China, we can identify key markets, trends, and potential business opportunities. This information can help us assess the manufacturers’ competitive position in the global market and their ability to meet international standards and regulations.
In conclusion, the use of platforms such as qcc.com, archive.org, and importyeti.com can provide valuable background research on sheet metal fastening manufacturers in China. This information can help us make informed decisions when selecting manufacturers for our own business needs.
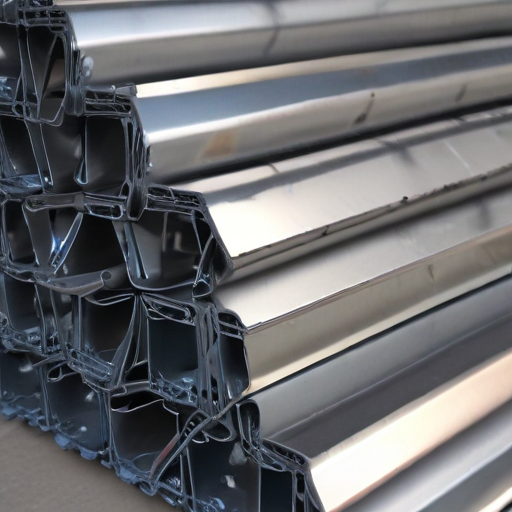
Price Cost Research for sheet metal fastening manufacturers Companies in China, use temu.com and 1688.com
Sheet metal fastening manufacturers in China can conduct price cost research using popular online platforms such as temu.com and 1688.com. These websites offer a wide range of suppliers and products in the manufacturing sector, making them ideal for sourcing and comparing prices.
On temu.com, manufacturers can search for specific sheet metal fastening products and browse through various suppliers to compare prices. The platform also allows users to directly contact suppliers to negotiate prices or inquire about bulk discounts. Additionally, temu.com provides a secure payment system for transactions, ensuring a smooth purchasing process.
1688.com, on the other hand, is a popular wholesale marketplace in China that connects manufacturers with suppliers. Companies can search for sheet metal fastening manufacturers on the platform and view detailed product listings, including pricing information. 1688.com also offers a wide range of suppliers, allowing manufacturers to compare prices and quality before making a purchasing decision.
By utilizing platforms like temu.com and 1688.com, sheet metal fastening manufacturers in China can easily conduct price cost research to find the best deals and suppliers for their business needs. This enables companies to save time and money while ensuring they source high-quality products for their manufacturing processes.
Shipping Cost for sheet metal fastening import from China
When importing sheet metal fastening products from China, the shipping cost will depend on various factors such as the weight of the shipment, the dimensions of the package, the shipping method chosen, and the delivery location.
Generally, when shipping sheet metal fastenings from China, air freight is a common choice for quicker delivery times. Air freight costs can range from $3 to $10 per kilogram, with additional fees for handling and fuel surcharges. For smaller shipments, courier services like DHL, FedEx, or UPS can also be used, with costs varying depending on the weight and size of the package.
For larger shipments, sea freight may be a more cost-effective option. Shipping containers from China to the US, for example, can cost around $800 to $2000 per container, with additional fees for loading and unloading at the ports.
It is important to consider the Incoterm used in the purchase agreement, as it will determine who is responsible for the shipping costs. For example, if the agreement is on a CIF (Cost, Insurance, Freight) basis, the supplier will be responsible for the shipping costs to the agreed-upon destination.
To minimize shipping costs, it is advisable to consolidate shipments, negotiate with multiple shipping providers, and consider different shipping methods based on the urgency of the delivery. Additionally, working with freight forwarders who have established relationships with carriers can help secure better rates and ensure a smoother shipping process.
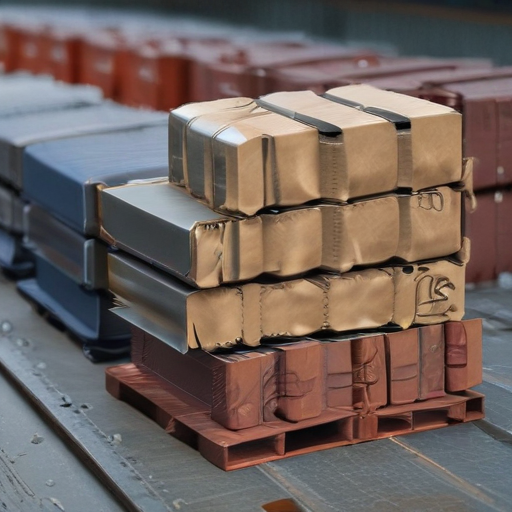
Compare China and Other sheet metal fastening Markets: Products Quality and Price,Visible and Hidden Costs
China is known for its highly competitive sheet metal fastening market, offering a wide range of products with varying quality and price levels. Chinese products have a reputation for being cost-effective, with prices typically lower than those from other markets. However, the quality of Chinese products can vary widely, with some manufacturers producing lower-grade items that may not meet international standards.
On the other hand, markets in countries like the US and Europe tend to offer higher quality sheet metal fastening products at a higher price point. These products are generally manufactured to stricter quality control standards, ensuring better performance and durability. While the prices may be higher, customers can often be more confident in the reliability of these products.
When comparing visible and hidden costs, Chinese products may initially appear more affordable, but additional costs can arise from factors such as shipping, customs duties, and quality control issues. These hidden costs can ultimately negate the initial savings of purchasing Chinese products. In contrast, products from other markets may have a higher upfront cost but often come with more transparent pricing and fewer hidden costs.
In summary, while China’s sheet metal fastening market offers a wide selection of products at competitive prices, customers should consider factors such as product quality and hidden costs when making purchasing decisions. Markets in other countries may offer higher quality products with more predictable pricing, providing a better long-term investment for customers seeking reliable and durable sheet metal fastening solutions.
Custom Private Labeling and Branding Opportunities with Chinese sheet metal fastening Manufacturers
Chinese sheet metal fastening manufacturers offer custom private labeling and branding opportunities for businesses looking to differentiate their products in the market. By partnering with these manufacturers, businesses can create their own unique brand identity by incorporating their logo, color schemes, and packaging designs into the products.
The advantages of private labeling with Chinese sheet metal fastening manufacturers include cost savings, quicker time to market, and the ability to control product quality and branding. Manufacturers can also provide additional services such as design assistance, product customization, and packaging options to meet the specific needs of each business.
With a wide range of sheet metal fastening products available, businesses can choose the right products to align with their brand and target market. Whether it’s screws, nuts, bolts, or clips, manufacturers can produce high-quality fastening solutions that meet the unique specifications and requirements of each business.
Overall, partnering with Chinese sheet metal fastening manufacturers for private labeling and branding opportunities can help businesses stand out in a competitive market, increase brand recognition, and attract more customers. By leveraging the expertise and resources of these manufacturers, businesses can create a strong brand presence and establish themselves as leaders in the industry.
Tips for Procurement and Considerations when Purchasing sheet metal fastening
When purchasing sheet metal fastening products, there are several considerations to keep in mind to ensure you are getting the best quality and value for your money. Here are some tips to help you make an informed decision:
1. Material: Make sure the fasteners are made from high-quality materials that are suitable for use with sheet metal. Common options include stainless steel, aluminum, and zinc-plated steel.
2. Size and Type: Consider the size and type of fastener that will work best for your specific application. Factors such as the thickness of the sheet metal, the load it will need to support, and the environmental conditions it will be exposed to should all be taken into account.
3. Corrosion Resistance: Since sheet metal is often used in outdoor or high-moisture environments, it’s important to choose fasteners that have good corrosion resistance. Look for products that are specifically designed for use with sheet metal and offer protection against rust and other forms of corrosion.
4. Strength and Durability: Ensure that the fasteners you choose are strong enough to securely hold the sheet metal in place without bending or breaking. Look for products that are designed to withstand the specific loads and stresses they will be subjected to.
5. Compatibility: Make sure the fasteners you choose are compatible with the tools and equipment you will be using for installation. This includes ensuring that the size and type of fastener match the requirements of your machinery.
By considering these factors and taking the time to research and compare different options, you can make an informed decision when purchasing sheet metal fastening products. Always remember to prioritize quality, durability, and compatibility to ensure the best results for your project.
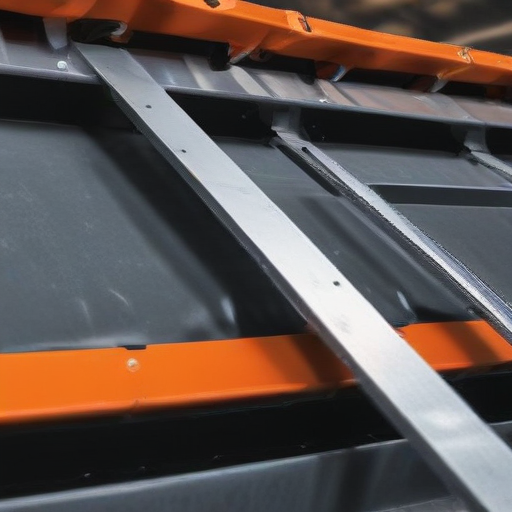
FAQs on Sourcing and Manufacturing sheet metal fastening in China
Q: How can I find reputable suppliers for sheet metal fastening in China?
A: To find reputable suppliers, you can utilize online sourcing platforms like Alibaba, Made-in-China, or Global Sources. It is crucial to conduct due diligence by checking supplier certifications, customer reviews, and requesting samples before making any commitments.
Q: What are the common manufacturing processes used for sheet metal fastening in China?
A: The most common manufacturing processes for sheet metal fastening in China include stamping, bending, welding, and surface finishing like plating or powder coating. China has a strong manufacturing infrastructure that can accommodate various production techniques for high-quality fasteners.
Q: How can I ensure quality control when sourcing sheet metal fastening from China?
A: To ensure quality control, it is essential to have a detailed specification sheet outlining your requirements. Consider working with a third-party inspection company to conduct on-site inspections and quality checks throughout the production process. Build a good relationship with your suppliers and visit their facilities regularly to maintain quality standards.
Q: Are there any challenges or risks associated with sourcing sheet metal fastening from China?
A: Some common challenges include language barriers, cultural differences, logistical issues, and intellectual property concerns. It is crucial to work with experienced sourcing agents or consultants who understand the local market and can help navigate these challenges effectively. Additionally, having a clear contract with your supplier outlining terms and conditions can help mitigate risks.
Q: What is the average lead time for manufacturing sheet metal fastening in China?
A: The average lead time for manufacturing sheet metal fastening in China can vary depending on the complexity of the product and the order quantity. Generally, lead times range from 2-6 weeks for standard fasteners, but it is important to discuss lead times with your supplier upfront to ensure timely delivery.
Why contact sourcifychina.com get free quota from reliable sheet metal fastening suppliers?
Sourcifychina.com is a trusted platform that connects businesses with reliable suppliers in China. By contacting Sourcifychina.com, you can easily get a free quota from reputable sheet metal fastening suppliers without the hassle of searching and vetting suppliers yourself. This saves you time and provides you with access to high-quality suppliers who have been verified for their reliability and product quality.
Additionally, by working with Sourcifychina.com, you can benefit from their expertise in the industry and their network of established suppliers. This ensures that you are connected with suppliers who are experienced in providing sheet metal fastening solutions and are able to meet your specific requirements.
By getting a free quota from reliable sheet metal fastening suppliers through Sourcifychina.com, you can access competitive pricing, high-quality products, and efficient service. This can help streamline your sourcing process, reduce costs, and ensure that you are partnering with trusted suppliers who can meet your business needs.
In conclusion, contacting Sourcifychina.com for a free quota from reliable sheet metal fastening suppliers is a smart choice for businesses looking to source quality products from trusted suppliers in China. Their platform simplifies the sourcing process and connects you with reputable suppliers, saving you time and providing peace of mind in your supplier selection.