Top sheet-metal-punching in China introduce,list main products and website if have
China is a top destination for sheet metal punching services, offering a wide range of products and capabilities. Some of the main products that can be obtained from top sheet metal punching companies in China include custom metal enclosures, brackets, panels, housings, and various other components. These companies use advanced equipment and technology to ensure precise and high-quality punching of sheet metals, catering to various industries such as automotive, aerospace, electronics, and more.
One of the top sheet metal punching companies in China is Shenzhen Sheng Lin Precision Metal Products Co., Ltd. Their main products include custom sheet metal enclosures, brackets, and panels, all of which are manufactured with precision and attention to detail. You can learn more about their services and products by visiting their website at www.slprecisionmetal.com.
Another leading sheet metal punching company in China is Shenzhen HSJ Metal Fabrication Co., Ltd. They specialize in producing custom sheet metal housings, components, and assemblies for a wide range of industries. Their website, www.hsjfabrication.com, provides more information on their capabilities and products.
Overall, China offers a range of top sheet metal punching companies that deliver high-quality products and services. These companies leverage advanced technology and expertise to meet the unique needs of their customers, making them a preferred choice for sheet metal punching services.
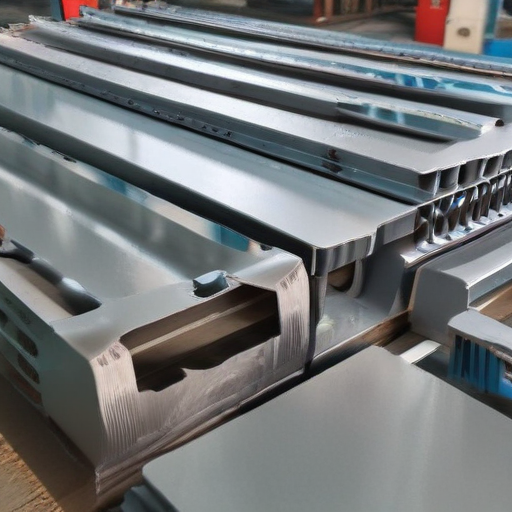
Types of sheet-metal-punching
Sheet metal punching is a process used in metal fabrication to create holes, slots, or other shapes in a metal sheet. There are several types of sheet metal punching techniques that can be used, each with its own advantages and applications.
1. Perforating: This involves creating a series of closely spaced holes in a metal sheet. Perforating is commonly used in applications where airflow or light transmission is desired, such as in air conditioning vents or speaker grilles.
2. Notching: Notching is the process of cutting out a small piece of metal to create a slot or groove. Notching is often used in applications where two pieces of metal need to fit together, such as in sheet metal joints or brackets.
3. Louvering: Louvering is the process of creating a series of angled slits or grooves in a metal sheet to control airflow or light transmission. Louvered panels are commonly used in applications such as ventilation systems or sunshades.
4. Embossing: Embossing involves creating raised or sunken patterns in a metal sheet. Embossed metal sheets are often used in decorative applications such as signage, nameplates, or architectural elements.
5. Coining: Coining is a precision punching technique used to create detailed designs or logos in a metal sheet. Coining can produce intricate patterns or text, making it ideal for applications such as jewelry, packaging, or branding.
Overall, sheet metal punching is a versatile and efficient technique that can be used in a variety of metal fabrication applications. By choosing the right punching technique for the job, manufacturers can create custom metal parts with precision and accuracy.
Pros and Cons of Using sheet-metal-punching
Sheet metal punching is a widely used method for creating holes or shapes in sheet metal. It involves using a punch and die to shear the metal and create the desired cutout. This process has several pros and cons to consider.
Pros:
– Cost-effective: Sheet metal punching is a cost-effective method for creating holes and shapes in sheet metal. It requires minimal tooling and can be done quickly and efficiently.
– High precision: Sheet metal punching allows for high precision and accuracy in creating holes and shapes. This is important for ensuring a tight fit and proper alignment in the final product.
– Fast production: Sheet metal punching is a fast process, making it ideal for high-volume production runs. This can help to reduce lead times and increase overall efficiency.
– Versatile: Sheet metal punching can be used to create a wide range of hole sizes and shapes, making it a versatile option for a variety of applications.
– Clean edges: Sheet metal punching produces clean, burr-free edges, reducing the need for additional finishing processes.
Cons:
– Limited to certain shapes: Sheet metal punching is best suited for creating simple holes and shapes. Complex geometries may require other methods such as laser cutting or waterjet cutting.
– Material thickness limitations: Sheet metal punching is most effective on thin to medium thickness materials. Thicker materials may require a more robust punching machine or a different cutting method.
– Tool wear: The punch and die used in sheet metal punching can wear out over time, leading to reduced precision and increased tooling costs.
– Deformation: Sheet metal punching can cause some deformation or distortion in the metal, especially near the edges of the cutout. This may require additional forming or straightening processes.
Overall, sheet metal punching is a cost-effective and efficient method for creating holes and shapes in sheet metal. However, it has limitations in terms of shape complexity and material thickness, and may result in some deformation or tool wear. It is important to consider these factors when deciding whether sheet metal punching is the right method for your project.
sheet-metal-punching Reference Specifications (varies for different product)
Sheet metal punching is a process used to create holes, notches, or other shapes in sheet metal material. The specifications for sheet metal punching can vary depending on the specific product being manufactured. However, some common reference specifications for sheet metal punching include:
– Material thickness: The thickness of the sheet metal being punched is an important factor in determining the type of punching equipment and process that should be used. Thicker materials may require more force or a different punching tool to create clean, precise holes.
– Hole size and shape: The size and shape of the holes being punched will be specified in the design drawings or product requirements. Punching equipment can be set up to create round, square, oval, or other shapes depending on the needs of the product.
– Hole spacing: The distance between holes, known as spacing, must also be carefully controlled to ensure that the final product meets dimensional requirements. The spacing of holes can impact the strength and appearance of the sheet metal part.
– Tolerance: Tolerance refers to the allowable deviation from the specified dimensions in the design drawings. Tolerance levels for sheet metal punching must be closely monitored to ensure that the finished product meets quality standards.
– Tooling and equipment: The type of punching tool and equipment used in the process will depend on the specific requirements of the product. Different types of punches, dies, and press machines may be used to achieve the desired results.
In summary, sheet metal punching requires careful attention to detail in order to meet the specifications for the product being manufactured. By considering factors such as material thickness, hole size and shape, tolerance, and tooling, manufacturers can produce high-quality sheet metal parts for a wide range of applications.
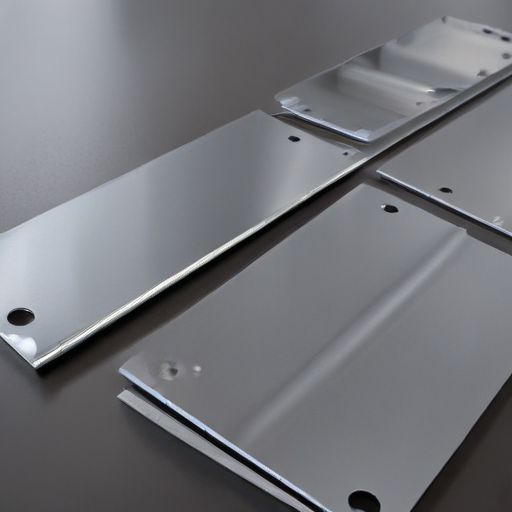
Applications of sheet-metal-punching
Sheet metal punching is a versatile process used in a wide range of applications. One common application is in the manufacturing of electronic enclosures, where precision punching is used to create holes for connectors, switches, and display panels. This process also allows for the creation of intricate patterns and designs, adding a decorative element to the finished product.
Sheet metal punching is also commonly used in the automotive industry for creating components such as brackets, panels, and trim pieces. The ability to quickly and accurately create holes and slots in sheet metal allows for efficient production of these parts, contributing to the overall quality and durability of the final product.
In the construction industry, sheet metal punching is used for creating structural components such as joist hangers, brackets, and supports. The precision of the punching process ensures that these components fit together seamlessly, facilitating quick and easy assembly on-site.
Sheet metal punching is also utilized in the production of household appliances, where it is used to create ventilation holes, mounting brackets, and other essential features. The ability to produce these components with high accuracy and consistency ensures that the appliances function properly and last for a long time.
Overall, sheet metal punching is a crucial process in a variety of industries, enabling the efficient production of high-quality components and products. Its versatility and precision make it an essential tool for manufacturers looking to create durable, functional, and aesthetically pleasing products.
Material of sheet-metal-punching
Sheet metal punching is a process used to create holes, notches, or other shapes in sheet metal using a machine called a punch press. The material of the sheet metal being punched plays a crucial role in determining the success and efficiency of the punching process.
One of the most common materials used for sheet metal punching is carbon steel. Carbon steel is a versatile and durable material that is relatively inexpensive and easy to work with. It is suitable for a wide range of applications and can be punched with precision and accuracy using a punch press.
Another popular material for sheet metal punching is stainless steel. Stainless steel is known for its corrosion resistance and durability, making it an ideal choice for applications where strength and aesthetic appeal are crucial. However, stainless steel is a harder material than carbon steel, which can make punching more challenging and require special tools and techniques.
Aluminum is another commonly used material for sheet metal punching. Aluminum is lightweight, corrosion-resistant, and easy to work with, making it suitable for a variety of applications. However, like stainless steel, aluminum is a softer material than carbon steel, which can affect the punching process and require adjustments to the punch press settings.
In conclusion, the material of the sheet metal being punched is an important factor to consider when using a punch press. Carbon steel, stainless steel, and aluminum are all popular choices for sheet metal punching, each with its own advantages and challenges. By selecting the right material and using proper techniques, sheet metal punching can be a cost-effective and efficient way to create precision-cut shapes in sheet metal.
Quality Testing Methods for sheet-metal-punching and how to control the quality
There are several quality testing methods for sheet-metal-punching that can be utilized to ensure the desired level of quality is achieved. These methods include visual inspection, dimensional inspection, hardness testing, and surface roughness measurement.
Visual inspection involves visually examining the punched sheet metal for any defects such as burrs, cracks, or uneven edges. Dimensional inspection involves measuring the dimensions of the punched holes or features to ensure they meet the specified tolerances. Hardness testing involves measuring the hardness of the punched sheet metal to ensure it meets the required hardness specifications. Surface roughness measurement involves measuring the surface finish of the punched sheet metal to ensure it meets the specified surface roughness requirements.
To control the quality of sheet-metal-punching, it is important to establish clear quality control procedures and standards. This includes setting specific tolerance limits for dimensions, hardness, and surface roughness, as well as implementing regular quality checks throughout the punching process. Additionally, training operators on proper punching techniques and maintenance of punching equipment can help ensure consistent quality.
Using statistical process control methods can also help to monitor and control the quality of sheet-metal-punching. By tracking key quality metrics and analyzing trends over time, manufacturers can identify potential issues and take corrective action to prevent defects from occurring.
Overall, implementing a combination of quality testing methods, clear quality control procedures, operator training, and statistical process control can help to ensure the quality of sheet-metal-punching is maintained at a high level.
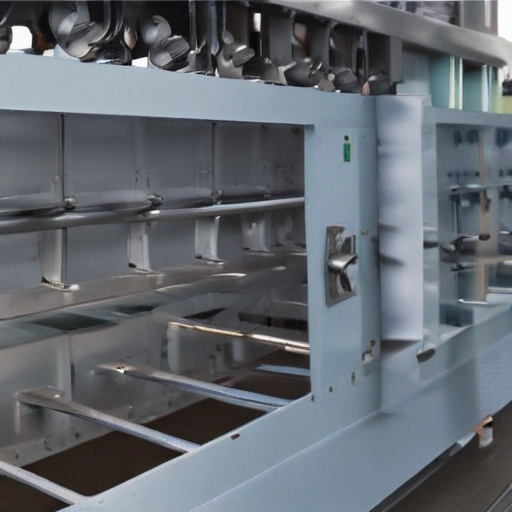
The Work Process and how to use sheet-metal-punching
Sheet metal punching is a common process used in the manufacturing industry to create holes or shapes in sheet metal. This process involves using a punch and die set to cut through the sheet metal and create the desired shape.
To use sheet metal punching, first, the sheet metal is placed on a flat surface and secured with clamps. The punch and die set is then positioned over the area where the hole or shape is to be created. The punch is aligned with the die, and pressure is applied to the punch, forcing it through the sheet metal and cutting out the desired shape.
It is important to choose the right punch and die set for the job, as different materials and thicknesses of sheet metal require different tools. The size and shape of the hole or shape to be created will also determine the type of punch and die set needed.
The work process for sheet metal punching involves careful planning, precise measurements, and attention to detail. It is important to ensure that the sheet metal is properly secured and that the punch and die set are aligned correctly before applying pressure. Safety precautions should also be taken, such as wearing protective eyewear and gloves.
In conclusion, sheet metal punching is a versatile and efficient process for creating holes and shapes in sheet metal. By following the correct steps and using the right tools, sheet metal punching can be done quickly and accurately.
sheet-metal-punching Importing questions including Cost,Supplier,Sample,Certification and Market
When importing sheet metal punching equipment, there are several important factors to consider. The first consideration is cost – it is important to research and compare prices from different suppliers to ensure you are getting a competitive price. Additionally, be sure to factor in shipping and import duties when calculating the total cost of importing the equipment.
In terms of suppliers, it is crucial to choose a reputable and reliable supplier with a track record of providing high-quality products. Look for suppliers that have experience in the industry and positive reviews from other customers.
Before making a bulk purchase, it is advisable to request samples from potential suppliers to test the quality of the equipment. This will give you a better idea of the product before making a larger investment.
Certification is another vital consideration when importing sheet metal punching equipment. Ensure that the equipment meets all necessary certifications and standards to guarantee its safety and performance.
Finally, consider the market for sheet metal punching equipment in your country. Research the demand for this type of equipment and any potential competitors in the market. Understanding the market will help you make more informed decisions about importing and selling the equipment.
In conclusion, when importing sheet metal punching equipment, it is essential to consider factors such as cost, supplier reputation, sample testing, certification, and market demand. By carefully evaluating these factors, you can make informed decisions and ensure a successful import process.
How to find and select check reliable sheet-metal-punching manufacturers in China
When looking for reliable sheet-metal-punching manufacturers in China, there are a few key steps to consider:
1. Research: Start by researching different manufacturers online and reading reviews from other customers. Look for manufacturers that have a good reputation for quality and reliability.
2. Verify credentials: Make sure the manufacturer is certified and has the necessary qualifications to produce sheet-metal-punching products. Check if they have ISO certifications or other industry-specific accreditations.
3. Request samples: Ask for samples of their work to evaluate the quality of their products. This will give you a better idea of the manufacturer’s capabilities and standards.
4. Evaluate communication: Communication is key when working with a manufacturer overseas. Make sure they are responsive, clear, and willing to answer any questions you may have.
5. Factory visit: If possible, visit the manufacturer’s factory in person to see their facilities and meet their team. This will give you a better sense of their capabilities and working conditions.
6. Check pricing: While cost is important, it should not be the only factor in your decision. Look for manufacturers that offer competitive pricing without compromising on quality.
7. Negotiate terms: Discuss payment terms, lead times, and any other important details before making a final decision. Make sure you have a clear understanding of the terms of the agreement.
By following these steps, you can find and select a reliable sheet-metal-punching manufacturer in China that meets your specific requirements and ensures a successful partnership.
Background Research for sheet-metal-punching manufacturers Companies in China, use qcc.com archive.org importyeti.com
Sheet metal punching is a common manufacturing process used to create holes or cutouts in sheet metal material. In China, there are numerous manufacturers specializing in sheet metal punching services. Some of the notable companies include:
1. Jiangsu Dasheng Metal Products Co., Ltd: This company is known for its expertise in sheet metal fabrication and punching services. They offer a wide range of capabilities, including CNC punching, laser cutting, and precision bending. With a commitment to quality and customer satisfaction, Jiangsu Dasheng Metal Products Co., Ltd has established a strong reputation in the industry.
2. Guangzhou Shuntai Metal Products Co., Ltd: This company is a leading sheet metal punching manufacturer in China. They have a state-of-the-art facility equipped with advanced punching machines to handle various sheet metal punching projects. Guangzhou Shuntai Metal Products Co., Ltd is known for its efficient production processes and quick turnaround times.
3. Suzhou Ace Tech Co., Ltd: Specializing in precision sheet metal punching, Suzhou Ace Tech Co., Ltd offers cutting-edge solutions for a wide range of industries. They have a team of skilled engineers and technicians who ensure high-quality products and services. With a focus on continuous improvement and innovation, Suzhou Ace Tech Co., Ltd is a trusted partner for sheet metal punching needs.
These companies can be found on online platforms such as qcc.com, archive.org, and importyeti.com, where their profiles, capabilities, and contact information are readily available for potential customers to access. By leveraging these resources, businesses can make informed decisions when sourcing sheet metal punching services in China.
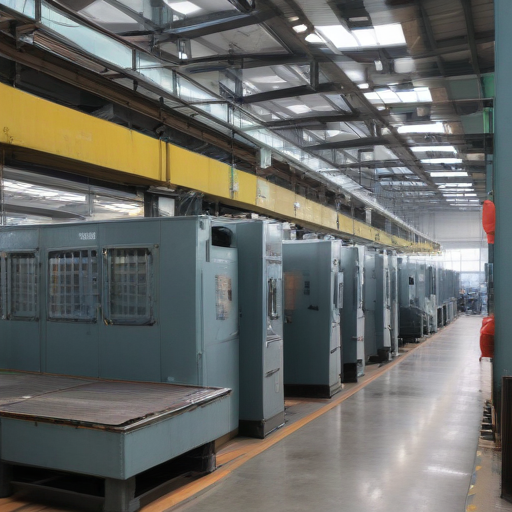
Price Cost Research for sheet-metal-punching manufacturers Companies in China, use temu.com and 1688.com
When conducting price cost research for sheet metal punching manufacturers in China, two popular websites to utilize are temu.com and 1688.com. These platforms provide a wide range of suppliers and manufacturers in the metalworking industry, allowing for easy comparison of prices and services.
By browsing through the listings on these websites, you can find a variety of sheet metal punching manufacturers in China that offer competitive pricing. Factors that may influence the cost of sheet metal punching services include the complexity of the design, the type of material used, the volume of production, and additional finishing services.
It is essential to reach out to multiple manufacturers to collect quotes and compare pricing. Additionally, consider factors such as production lead times, quality control processes, and payment terms when evaluating potential suppliers.
By leveraging these online resources, you can efficiently gather pricing information and find the best sheet metal punching manufacturer in China that meets your requirements. Remember to ask relevant questions and request samples before making a final decision to ensure that you are getting the best value for your investment.
Shipping Cost for sheet-metal-punching import from China
The shipping cost for importing sheet-metal-punching products from China can vary depending on several factors. These factors include the size and weight of the shipment, the shipping method chosen, the shipping distance, and any additional services required (such as insurance or expedited shipping).
Typically, for smaller shipments of sheet-metal-punching products, air freight is the preferred shipping method. Air freight is faster than sea freight and is best suited for smaller, more urgent shipments. The cost of air freight can range from $2 to $5 per kilogram, depending on the exact weight and size of the shipment.
For larger shipments, sea freight may be a more cost-effective option. Sea freight is cheaper than air freight but generally takes longer to arrive. The cost of sea freight can vary widely depending on the volume of the shipment, the shipping distance, and the chosen shipping method (such as FCL or LCL). On average, sea freight costs can range from $1,000 to $5,000 per container.
In addition to the transportation costs, it is important to consider other expenses such as customs duties, taxes, insurance, and handling fees. These costs can add up and should be factored into the overall shipping cost.
To ensure a smooth and cost-effective importing process, it is recommended to work with a reliable freight forwarder or shipping company that specializes in importing goods from China. They can provide guidance on the best shipping method, handle all documentation, and help navigate any potential customs issues.
Overall, the shipping cost for importing sheet-metal-punching products from China can vary depending on a variety of factors, but with careful planning and the right partners, it can be a manageable expense.
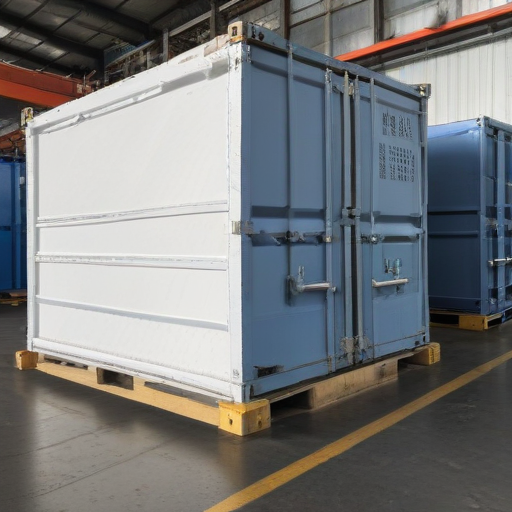
Compare China and Other sheet-metal-punching Markets: Products Quality and Price,Visible and Hidden Costs
China is known for its cost-effective sheet metal punching services due to the abundance of skilled labor and advanced manufacturing technology. However, there have been concerns about the quality of products produced in China, as some manufacturers prioritize lower costs over product quality. This has led to instances of inconsistent product quality and reliability.
On the other hand, other markets such as Europe and the United States are known for producing high-quality sheet metal punching products. Manufacturers in these markets typically adhere to stringent quality control standards, resulting in more reliable and durable products. However, the higher labor and operational costs in these markets often translate to higher prices for customers.
In terms of visible costs, China generally offers lower prices compared to other markets due to lower labor and operational costs. This makes China an attractive option for cost-conscious customers looking to maximize their budget. However, hidden costs such as shipping, transportation, and import tariffs can sometimes offset the initial cost savings, especially for customers located outside of China.
In contrast, other markets may have higher upfront costs, but customers can benefit from more transparent pricing structures and fewer hidden costs. Additionally, products from these markets are more likely to meet quality and safety standards, reducing the risk of defects or recalls that could result in additional costs down the line.
Ultimately, the choice between China and other sheet metal punching markets comes down to balancing price and quality considerations. While China may offer lower prices, customers should carefully evaluate the overall costs, including potential hidden costs and the long-term impact of product quality on their operations. Customers seeking high-quality, reliable products may find better value in other markets despite the higher upfront costs.
Custom Private Labeling and Branding Opportunities with Chinese sheet-metal-punching Manufacturers
Chinese sheet-metal-punching manufacturers offer excellent opportunities for custom private labeling and branding for companies looking to establish their own unique products in the market. With their advanced technology and expertise in precision metal fabrication, these manufacturers can create customized products according to your specifications and branding requirements.
By working closely with the manufacturers, you can choose the materials, design, and finishes that best represent your brand identity. This allows you to create a distinct and recognizable product that sets you apart from competitors. From logo engraving to custom packaging, there are a wide range of branding options available to help you create a cohesive and professional image for your products.
Furthermore, partnering with Chinese sheet-metal-punching manufacturers can also help streamline your production process and reduce costs. By sourcing directly from manufacturers, you can take advantage of their cost-effective production capabilities and benefit from competitive pricing. This allows you to maximize your profit margins while offering high-quality products to your customers.
Overall, working with Chinese sheet-metal-punching manufacturers on custom private labeling and branding can help you establish a strong presence in the market and build a loyal customer base. With their expertise and resources, you can create products that reflect your brand values and resonate with your target audience. Contact a manufacturer today to explore the possibilities for custom branding and take your products to the next level.
Tips for Procurement and Considerations when Purchasing sheet-metal-punching
1. Define your project requirements: Before purchasing sheet metal punching equipment, clearly define your project requirements including the type of materials you will be working with, the thicknesses of the materials, the size of the sheets, and the frequency of use.
2. Research different types of sheet metal punching machines: There are various types of sheet metal punching machines available on the market including manual, hydraulic, and CNC machines. Research and compare the features, capabilities, and prices of different machines to determine which type is best suited for your needs.
3. Consider the capacity and capabilities of the machine: When purchasing a sheet metal punching machine, consider the capacity and capabilities of the machine in terms of the maximum sheet size it can handle, the thickness of materials it can punch, and the speed and accuracy of the punching process.
4. Look for quality and durability: Investing in a high-quality and durable sheet metal punching machine will ensure long-term performance and productivity. Look for machines made from robust materials and from reputable manufacturers with a track record of producing reliable equipment.
5. Consider your budget and ROI: Determine your budget for purchasing a sheet metal punching machine and consider the return on investment (ROI) that the machine will provide. Compare the cost of the machine with the benefits it will bring to your business in terms of increased efficiency, productivity, and quality of work.
6. Evaluate the after-sales support: Look for suppliers who offer after-sales support including installation, training, maintenance, and warranty services. This will ensure that you can get assistance and support when needed to keep your machine running smoothly.
7. Get feedback from other users: Before making a decision, try to get feedback from other users of the same sheet metal punching machine to learn about their experiences, satisfaction levels, and any potential issues they have encountered. This will help you make an informed decision.
8. Consider space and power requirements: Make sure to consider the space and power requirements of the sheet metal punching machine and ensure that you have adequate space and power supply to accommodate the machine in your facility.
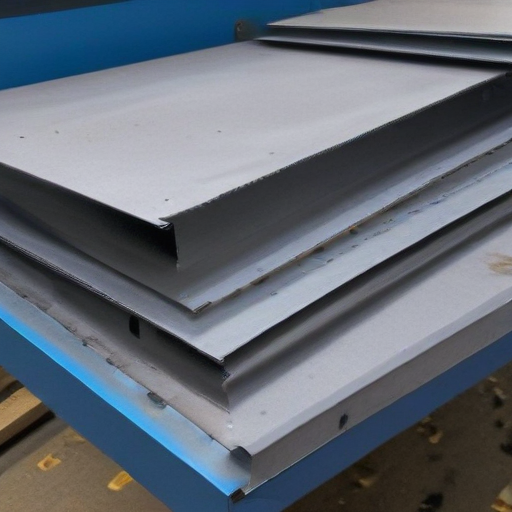
FAQs on Sourcing and Manufacturing sheet-metal-punching in China
Q: What are the benefits of sourcing sheet metal punching in China?
A: Sourcing sheet metal punching in China offers cost advantages, as labor and material costs are typically lower compared to Western countries. Additionally, China has a large pool of skilled workers and advanced manufacturing facilities, ensuring high-quality products at competitive prices.
Q: What factors should I consider when selecting a manufacturer in China for sheet metal punching?
A: When selecting a manufacturer in China for sheet metal punching, consider factors such as the manufacturer’s experience and reputation, quality control measures, production capabilities, pricing, lead times, and communication abilities. It is also important to visit the manufacturer’s facilities in person to assess their capabilities and quality control processes.
Q: How can I ensure quality control when sourcing sheet metal punching in China?
A: To ensure quality control when sourcing sheet metal punching in China, work with manufacturers that have certifications such as ISO 9001, and conduct regular inspections and audits of their facilities. It is also important to clearly communicate your quality requirements and specifications to the manufacturer, and conduct thorough testing and inspection of the finished products before shipping.
Q: What are common challenges when sourcing sheet metal punching in China?
A: Common challenges when sourcing sheet metal punching in China include language barriers, cultural differences, intellectual property protection, and logistical issues. It is important to work with a reputable sourcing partner or agent in China who can help navigate these challenges and ensure a smooth sourcing process.
Q: How can I mitigate risks when sourcing sheet metal punching in China?
A: To mitigate risks when sourcing sheet metal punching in China, conduct thorough due diligence on potential manufacturers, negotiate clear contracts with agreed-upon terms and quality standards, and consider implementing a quality control and inspection process throughout the production cycle. It is also important to have open communication with the manufacturer and address any issues promptly.
Why contact sourcifychina.com get free quota from reliable sheet-metal-punching suppliers?
Sourcifychina.com provides a simple and convenient platform for businesses to connect with reliable sheet-metal-punching suppliers in China. By contacting Sourcifychina.com, businesses can easily get a free quota from these suppliers, allowing them to quickly assess their capabilities and pricing before committing to a partnership.
Sheet-metal punching is a critical process in manufacturing, and it is essential to find a reliable supplier who can consistently deliver high-quality products on time. By partnering with reputable sheet-metal-punching suppliers through Sourcifychina.com, businesses can ensure that they are working with trusted professionals who have the expertise and resources to meet their specific needs.
In addition to providing a hassle-free way to connect with suppliers, Sourcifychina.com also offers valuable insights and guidance to businesses looking to outsource their sheet-metal-punching needs. Their team of experts can help businesses navigate the complexities of sourcing from China, ensuring a smooth and efficient process from start to finish.
Overall, contacting Sourcifychina.com to get a free quota from reliable sheet-metal-punching suppliers is a smart and practical decision for businesses looking to streamline their supply chain and access cost-effective manufacturing solutions. With their expertise and industry connections, Sourcifychina.com can help businesses find the right supplier for their specific needs, saving time and resources in the process.